
Industrial Electric Motors
.jpg)
The AC induction motor is a workhorse in industrial applications—simple, reliable, and able to operate in all kinds of difficult conditions. It's also really efficient, at least in comparison to some of the other machines commonly found in an industrial setting. There are essentially two kinds: the single-phase and the three-phase. The single-phase motor isn't favored by designers for the kinds of jobs the three-phase motor typically handles. The three-phase motor is preferred when it comes to things like pumps, conveyors, compressors, and blowers.
The power supply frequency determines the constant speed of another type of electric motor: the synchronous motor. These industrial motors are found in applications needing accurate speed control, good timing (recording equipment and certain types of conveyors, for example), and power factor correction. Industrial facilities often use synchronous motors when an operation must be coordinated with other events in a system.
Subcategories
Products
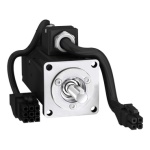
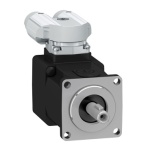
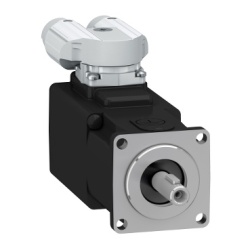
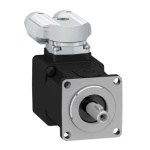
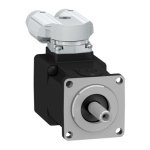
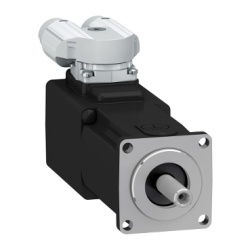
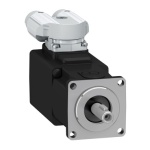
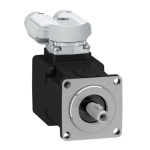
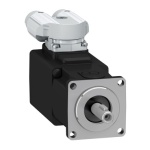
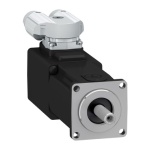
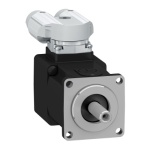
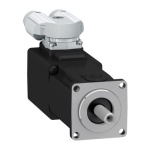
More Information about Industrial Electric Motors
Electric motors convert electrical energy into mechanical energy by using electric current to create a motor's magnetic field within the wire winding. This magnetic field interacts with the motor's magnetic field to generate force, which causes the motor's shaft to rotate. Regular maintenance and high-quality replacement parts are essential to ensure the motor operates efficiently and reliably over time.
Motor Starters, Soft Starters and VFDs
Motor Starters
Motor starters safely start and stop a motor in industrial applications. They are designed with a contactor, overload and circuit protection. They are used when basic motor control is required, where torque on the motor is not a concern and speed control is not needed. The advantages of motor starters include: lower cost, allows for remote operation, allows for monitoring of motor state (with the use of auxiliary contacts) and they are safe and efficient. The disadvantages include: high inrush current that can cause fuses to blow and breakers to trip if the inrush is too high, and the starter will allow a full torque to start the motor which can cause the motor to ramp up to full speed very quickly potentially causing the motor to wear and degrade prematurely.
Soft Starters
Soft starters protect motors from inrush current by gently ramping up the motor to full speed. They provide all of the same functions as a traditional motor starter. The advantages of soft starters include: they are less expensive than a VFD when only startup control is needed, they are a smaller system than a VFD where space is a concern and they prevent unwanted torque upon startup, prolonging the life of the motor. The disadvantages include: they are more expensive than a traditional motor starter and they do not allow for full speed control.
VFDs
A Variable Frequency Drive (VFD) allows for the slow ramp up of a motor during startup and the slowing down of the motor during shutdown. It also allows for full speed control during the entire run cycle of the motor. VFDs provide the same functions as both the traditional motor starters and soft starters. The advantages of VFDs include: full speed control (start, stop and in-between), more custom control and monitoring, energy savings due to efficient motor usage and less wear and tear on the motors. The disadvantages include: they are more expensive and larger than other motor control options and they generate heat that may require fans or AC units.