
Pump Motors
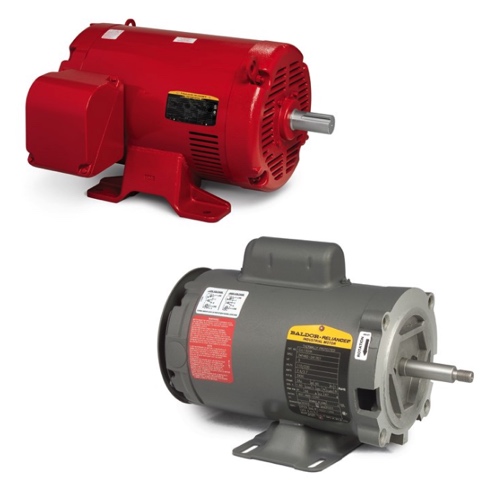
Pump motors are typically used to provide power to pumps that are used to circulate fluids of many kinds (for example, water, air, gas, and other specifically defined liquids) in commercial and industrial applications. They are most commonly used in water-recirculating systems of several types. Agriculture, water treatment, and the petrochemical industry are some of the application areas that use pump motors extensively. Some specific applications include: fire suppression systems, industrial wastewater and commercial pools.
These motors are engineered utilizing energy efficient designs. Unlike most pumps, which are powered by internal combustion engines, electric submersible pumps use no mechanical power train above the surface. This makes them ideal for use in remote or hard-to-reach locations. What these pumps have in common is that they typically use an efficient three-phase induction motor that is cooled by the process fluid being pumped. This motor is not just a run-of-the-mill unit. It is a high-efficiency, sturdy device that turns constantly.
Subcategories
Products
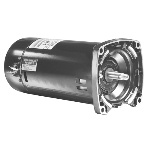



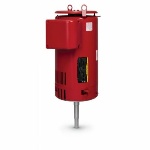







More Information about Pump Motors
Electric motor-driven pumps come in many types and power rating combinations. Commercial pump motor construction uses pressed or formed sheet metal or cast iron. They tend to be efficient, and the motors can run at a great variety of speeds over a range of conditions. Some of the latest specially designed pumps handle the full range of speeds for many different types of power system applications. Certain motors offer a soft start, which requires less inrush current and improves the life of the pump. By controlling the motor, you can decide the speed of the pump and the amount of flow it creates.
FAQs
Does a dynamically balanced rotor help with increasing system reliability and reducing maintenance costs?
Yes, a dynamically balanced rotor helps increase system reliability and reduce maintenance costs by minimizing vibration, wear, and mechanical stress on the motor and associated components.
What are the key features of inverter duty pump motors?
Key features of inverter duty pump motors include enhanced insulation systems, variable speed capability, robust construction for high torque at low speeds, and compatibility with variable frequency drives (VFDs) for precise control and energy efficiency.
Motor Starters, Soft Starters and VFDs
Motor Starters
Motor starters safely start and stop a motor in industrial applications. They are designed with a contactor, overload and circuit protection. They are used when basic motor control is required, where torque on the motor is not a concern and speed control is not needed. The advantages of motor starters include: lower cost, allows for remote operation, allows for monitoring of motor state (with the use of auxiliary contacts) and they are safe and efficient. The disadvantages include: high inrush current that can cause fuses to blow and breakers to trip if the inrush is too high, and the starter will allow a full torque to start the motor which can cause the motor to ramp up to full speed very quickly potentially causing the motor to wear and degrade prematurely.
Soft Starters
Soft starters protect motors from inrush current by gently ramping up the motor to full speed. They provide all of the same functions as a traditional motor starter. The advantages of soft starters include: they are less expensive than a VFD when only startup control is needed, they are a smaller system than a VFD where space is a concern and they prevent unwanted torque upon startup, prolonging the life of the motor. The disadvantages include: they are more expensive than a traditional motor starter and they do not allow for full speed control.
VFDs
A Variable Frequency Drive (VFD) allows for the slow ramp up of a motor during startup and the slowing down of the motor during shutdown. It also allows for full speed control during the entire run cycle of the motor. VFDs provide the same functions as both the traditional motor starters and soft starters. The advantages of VFDs include: full speed control (start, stop and in-between), more custom control and monitoring, energy savings due to efficient motor usage and less wear and tear on the motors. The disadvantages include: they are more expensive and larger than other motor control options and they generate heat that may require fans or AC units.