
Plugs & Receptacles
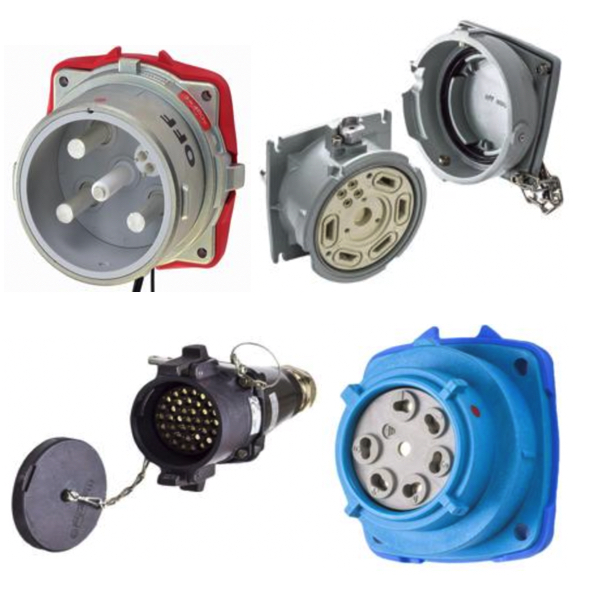
Industrial plugs and receptacles are electrical connectors designed for use in industrial environments where heavy-duty equipment and machinery are used. They are designed to handle higher current and voltage levels than standard residential or commercial connectors, and they are built to withstand harsh environments and rough handling.
Industrial plugs and receptacles are available in various configurations, including voltage ratings, current ratings, and pin configurations. They are typically made from durable materials such as thermoplastic, rubber, or metal, and they have features such as IP (Ingress Protection) ratings, which indicate their resistance to dust and moisture.
The plugs and receptacles are designed to provide secure and reliable electrical connections between the power source and the devices or machinery they are used with. They are available in both male (plug) and female (receptacle) configurations, and they have locking mechanisms that prevent accidental disconnection.
Subcategories
Products
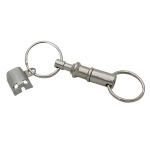
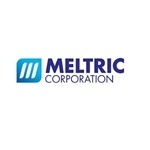
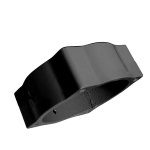
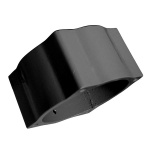
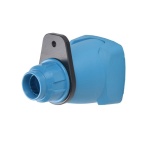
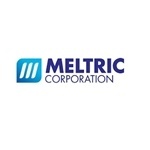
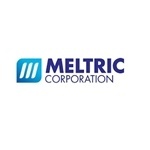
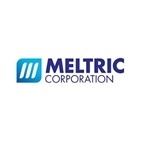
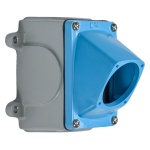
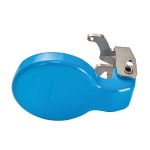
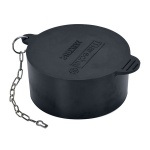
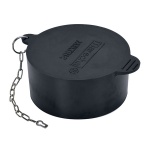
More Information about Industrial Plugs and Receptacles
Switch-Rated Plugs and Receptacles
Switch-Rated plugs and receptacles prevent unintended access to live parts with an integral switching function that ensures that the plug contacts are de-engergized before an operator can remove the plug from the receptacle. Visual verification is provided when the power is off. The operator's safety is assured without the need to perform hazard analysis, use electrical protective equipment or establish flash protection boundaries.
FAQs
What are mechanical interlocks in industrial applications?
Mechanical interlocks are safety devices used in industrial applications to prevent hazardous conditions from occurring due to the inadvertent or unauthorized operation of machinery or equipment. They are designed to ensure that certain actions can only be performed in a specific order, preventing unsafe situations such as accidental start-up or equipment damage.
Are industrial plugs and receptacles safe to use in an outdoor installation?
Industrial plugs and receptacles can be safe to use in an outdoor installation, but it's essential to carefully consider the application, environment, and rating of the connectors, as well as following proper installation and maintenance practices.
AC Grounding Basics: Grounding Series (Part 4)
The National Electrical Code (NEC) states that electrical systems must be grounded to a point that the maximum voltage, to ground underground conductors, does not exceed 150 volts. It also states that any 3-phase 4-wire, Y configurations and Delta configurations have the neutral wire grounded as well. These requirements cover any electrical systems ranging from single-phase 120 volts, all the way to 3-phase 480 volts AC. The conductor that needs to be grounded in these types of systems will always be the neutral wire.
A bonding conductor is needed between the grounded conductor and the equipment, grounding the conductor to the metallic enclosure of the main electrical service. It is important to make sure that a properly sized conductor is used to accommodate the potential surges that may occur in the electrical system. When grounding in a separately derived AC system, which is a system where components such as a generator can have the grounded conductors, where continuity is possibly interrupted by a transfer switch, it is important to make sure that the grounding conductor is bonded to the equipment grounding conductor of the metallic chassis on the load side of the electrical service through the use of a main bonding jumper. When continuity is not being interrupted on the load side, then it is critical to make sure that there is no bond between the neutral wire or grounding conductor and the metallic chassis of the electrical service. This will allow the main bonding to occur at the main service panel entrance point.