
Temperature Transmitters & Transducers
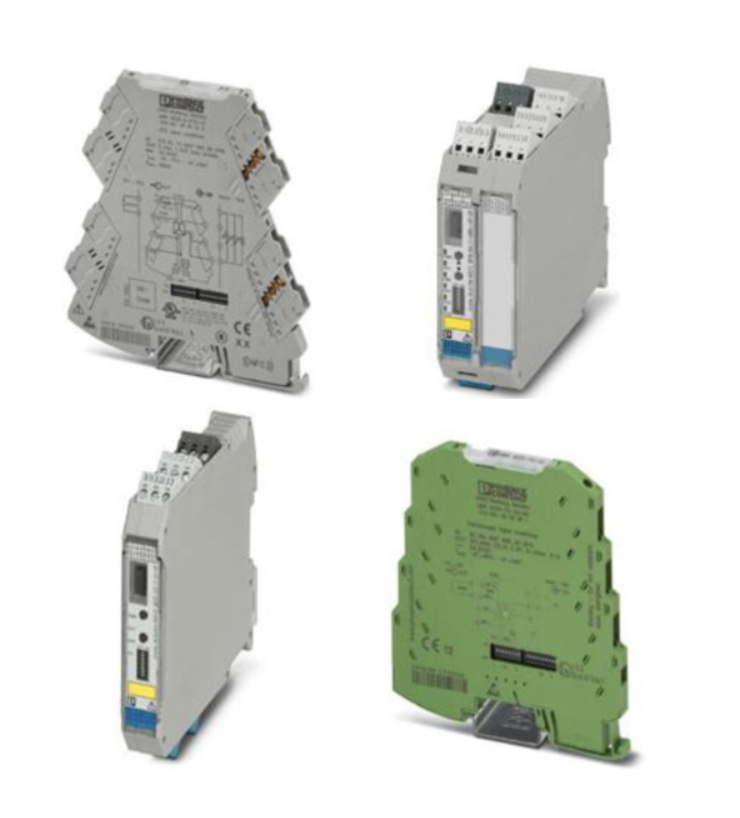
Temperature transmitters and transducers are electronic devices used to measure and transmit temperature readings in various industrial and commercial applications. They are commonly used in process control systems, automation systems, and heating, ventilation, and air conditioning (HVAC) systems.
A temperature transmitter is a device that converts a temperature sensor's electrical signal into a standardized 4-20 mA output signal, which can be easily transmitted over long distances to a control system or a display device. Temperature transmitters are often used in industrial environments where the temperature measurement needs to be accurate and stable over long distances.
On the other hand, temperature transducers are devices that convert a physical temperature measurement into an electrical signal that can be used by a control system or display device. Temperature transducers are often used in HVAC and building automation systems, where they measure temperature and humidity to control heating, cooling, and ventilation systems.
Products
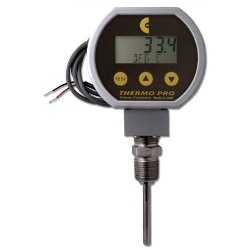
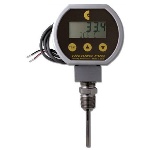
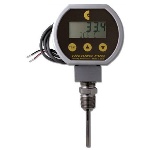
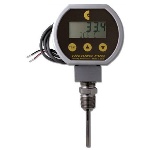
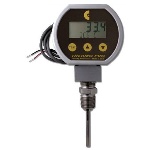
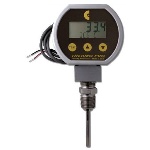
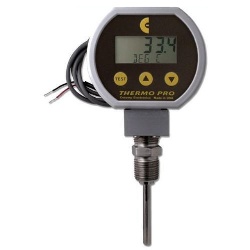
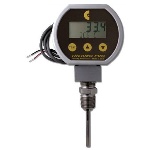
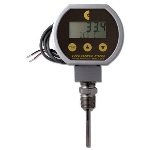
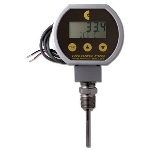
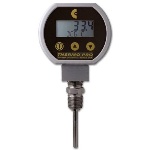
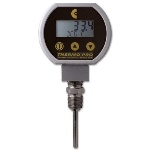
More Information about Temperature Transmitters and Transducers
Temperature transmitters and transducers are available in various types, depending on the application requirements. Some common types of temperature transmitters and transducers include:
Resistance Temperature Detectors (RTDs)
RTDs, also known as resistance thermometers, are temperature sensors that are made of a metal wire or film, and their resistance changes with temperature. RTD sensors are highly accurate and stable over a wide temperature range, making them suitable for use in industrial environments.
Thermocouples
Thermocouples are temperature sensors that use the voltage produced by two dissimilar metals to measure temperature. Thermocouples are highly durable and can withstand high temperatures, making them suitable for use in high-temperature industrial applications.
Infrared Temperature Sensors
Infrared temperature sensors use non-contact infrared technology to measure temperature. They are ideal for use in applications where the temperature needs to be measured without making contact with the object being measured, such as in food processing or medical applications.
Digital Temperature Sensors
Digital temperature sensors are microchip-based sensors that provide accurate temperature measurements and can communicate with digital systems.
FAQs
What is the difference between an analog signal and a digital signal?
The main difference between an analog signal and a digital signal is that an analog signal is continuous, while a digital signal is discrete. Analog signals can vary in an infinite number of ways, while digital signals can only represent a finite number of values.
What is the standardized output signal for temperature probes?
The standardized output signal for temperature probes varies depending on the type of sensor being used, but in all cases, the signal is proportional to the temperature being measured.
Transmitters vs Transducers
Some of the most common types of transmitters and transducers can be found on pressure instruments. Examples of these include: drop-in well pressure devices and devices that measure the pressure in a pipe or gas chamber. Transmitters and transducers can also be found on flow and speed measurement devices.
What is the difference between transmitters and transducers?
The main difference is the way they send data to the monitoring device, like a PLC. In terms of measurement, the transmitter will reference a measuring unit by sending a milliamp signal (such as 4-20 mA). A transducer will reference a measuring unit by sending a voltage signal, typically in volts or millivolts.
Why have the two different types of transmission methods?
The method will depend on the application. If the electrical connection in the application travels a short distance, a pressure transducer is the better choice. Pressure transducers are smaller with fewer active electronic components that can be upset by electromagnetic interference. Also, the voltage signals transmitted over longer distances are subject to voltage drop and signal corruption. A transmitter is better for transmitting signals over a long distance.