
Fan Motors
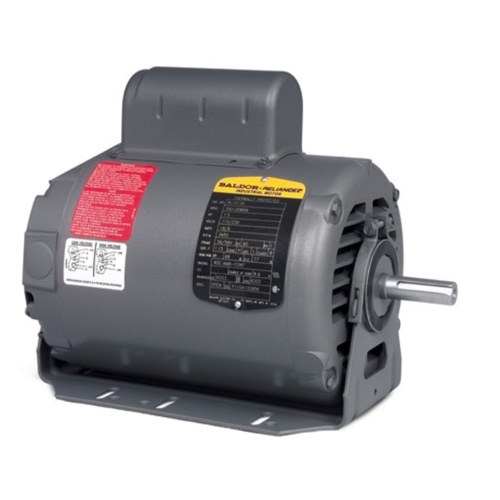
Motors that drive industrial fans are essential parts used in large-scale applications. They supply the necessary airflow for cooling, ventilation, and other forms of air supply and exhaust in various industries. Industrial fan motors, by and large, are built to withstand the kind of continual punishment for which the environments of, say, a manufacturing plant or a data center are famous.
Industrial fans, and their motors, often work continuously. They use large amounts of energy. But when it comes to efficiency, many models have what it takes. For both electric motors and the attached fan, the efficiency is even more important. And a good thing to look for in today's market is whether a motor meets or surpasses the efficiency standards of the NEMA Premium Efficiency or IE3 level.
Products
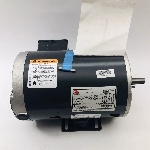











More Information about Fan Motors
Motors that power industrial fans are usually furnished with advanced cooling apparatuses to handle the heat they generate during extended operation. They may have external fans of various types bolted to their outsides. They could be drawing air in through special ventilation systems and distributing it throughout without much issue. Or, they might even have a safe number of heat-generating components pushing heat and safety issues outward to the outside of plastic wall components that form the structures at the ends of the lead wires that allow the currents to flow into the coils of wire that make motors what they are: current converters.
FAQs
Does a single phase motor have the necessary belt drive for continuous air movement to cool a large facility?
No, a single-phase motor typically does not have the necessary power and efficiency for the continuous air movement required to cool a large facility. A three phase blowers would be optimal.
Motor Starters, Soft Starters and VFDs
Motor starters safely start and stop a motor in industrial applications. They are designed with a contactor, overload and circuit protection. They are used when basic motor control is required, where torque on the motor is not a concern and speed control is not needed. Theadvantages of motor starters include: lower cost, allows for remote operation, allows for monitoring of motor state (with the use of auxiliary contacts) and they are safe and efficient. The disadvantages include: high inrush current that can cause fuses to blow and breakers to trip if the inrush is too high, and the starter will allow a full torque to start the motor which can cause the motor to ramp up to full speed very quickly potentially causing the motor to wear and degrade prematurely.
Soft starters protect motors from inrush current by gently ramping up the motor to full speed. They provide all of the same functions as a traditional motor starter. The advantages of soft starters include: they are less expensive than a VFD when only startup control is needed, they are a smaller system than a VFD where space is a concern and they prevent unwanted torque upon startup, prolonging the life of the motor. The disadvantages include: they are more expensive than a traditional motor starter and they do not allow for full speed control.
Variable Frequency Drives (VFDs) allow for the slow ramp up of a motor during startup and the slowing down of the motor during shutdown. They also allow for full speed control during the entire run cycle of the motor. VFDs provide the same functions as both the traditional motor starters and soft starters. The advantages of VFDs include: full speed control (start, stop and in-between), more custom control and monitoring, energy savings due to efficient motor usage and less wear and tear on the motors. The disadvantages include: they are more expensive and larger than other motor control options and they generate heat that may require fans or AC units.