
Steel Enclosures & Junction Boxes

Steel enclosures have become a "must-have" that many industries can't do without. They have become so popular mainly for two reasons: steel enclosures are incredibly robust and, therefore, reliable to protect the electrical components they house; and they are versatile. Steel enclosures come in various types of steel, which are chosen based on the demands of the task at hand.
For most industrial applications, carbon steel is the steel of choice. Carbon steel is known for its durable, super-strong properties. If you hit it with a hammer, it will dent and possibly even be punctured, but with normal handling, it doesn't get beaten up.
The protective zinc layer on galvanized steel enclosures makes them even more resistant to rust and corrosion. For this reason, they are perfect for outside equipment requiring rain- and rust-proof enclosures.
If you're looking for a more affordable but still solid option, you can't go wrong with mild steel enclosures. Whether you need an electrical control system for a factory or a basic electronics cabinet, mild steel can do the job without breaking your budget.
Subcategories
Products
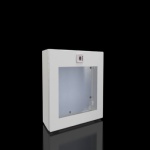
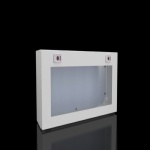
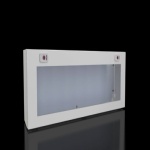
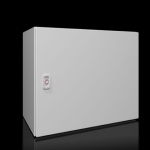
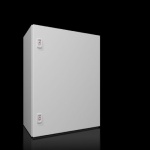
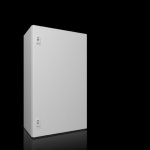
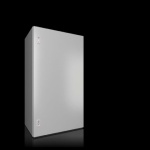
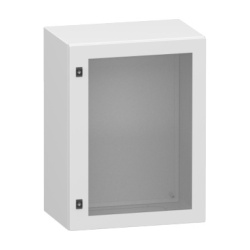
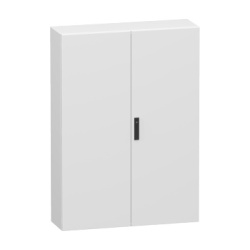
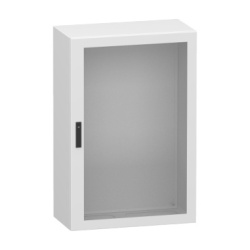
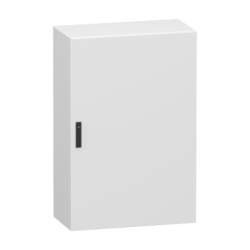
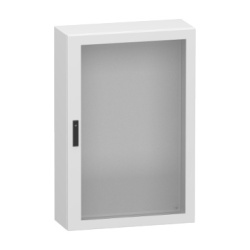
FAQs
What are the benefits of steel enclosures over stainless steel enclosures?
The use of steel industrial enclosures is usually a wise economical decision because they are exceptionally strong and durable. They are suitable for environments where conditions like temperature and humidity are held constant since they efficiently guard electrical components from all the physical forces of their surroundings.
Mounting Electrical Enclosures
Before mounting to any surface, it is important to understand how the hardware will interface with the enclosure. In many cases, the enclosures will have holes at the corners that can be used to attach any mounting hardware. It is common to see a mounting strut, commonly referring to as a Unistrut, being used with these electrical enclosures. The Unistrut can attach to the enclosure and provide a very strong connection point to either a wall, concrete or pole mount.
When mounting to a concrete wall, there are several things that should be considered to ensure it is done correctly. Industrial concrete anchors provide a very strong and reliable connection that can last a very long time. Make sure that the concrete is thick and strong enough for these types of anchors. Once the anchors have been installed, attach them to the mounting strut that is attached to the enclosure using hardware that is designed for that particular type of mounting strut.
When installing heavy duty enclosures on a pole or mass, it is important to make sure that the pole can handle the weight of the enclosure. It is recommended that the pole is made of a very strong rigid material. At least two inch rigid galvanized conduit is recommended. Once the pole has been secured into the ground, strut clamps designed for the size of conduit will attach the enclosure.