
Eaton PLCs
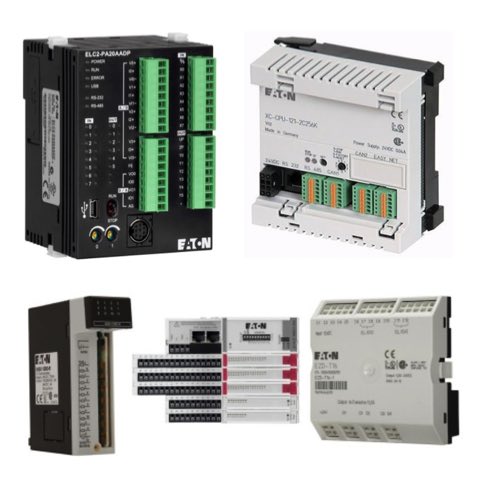
Eaton PLCs are advanced programmable logic controllers (PLCs) designed to provide efficient control solutions for industrial machine or process automation. These PLCs are solid-state devices that can monitor inputs from sources like pressure sensors, temperature sensors, and limit switches auxiliary contacts, making them ideal for applications requiring precise automation. Eaton offers a range of PLCs in action, including nano programmable logic controllers, compact programmable logic controllers, and modular PLCs for scalability. Whether used in wastewater treatment plants or industrial manufacturing, Eaton PLCs are designed to monitor inputs and control various processes efficiently.
Eaton’s easyE4 nano programmable logic, XC compact programmable logic, and XC modular programmable logic controllers provide flexible automation solutions for businesses looking to optimize operation of a machine or facility. These PLCs can be hardwired to devices monitored and hardwired to devices controlled, ensuring reliable performance in critical industrial environments. Eaton also offers the XN300 I/O system, allowing seamless expansion and connectivity for complex automation setups. With a separate CPU module input-output, Eaton PLCs enable precise control, enhancing system efficiency and reducing downtime. Their ability to deliver industrial controls solutions makes them essential in modern automated industries.
Products
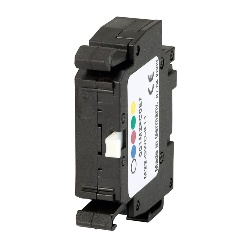
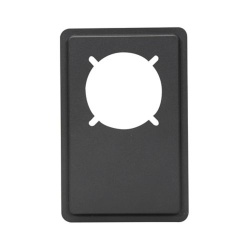
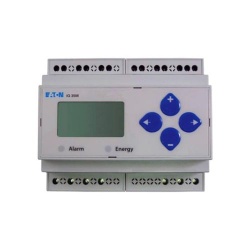
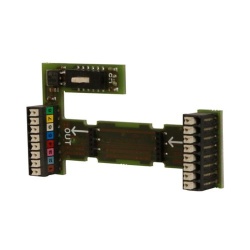
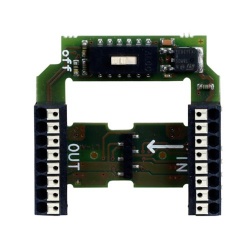
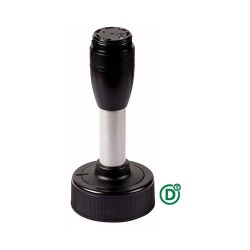
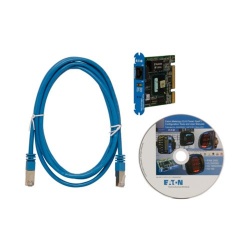
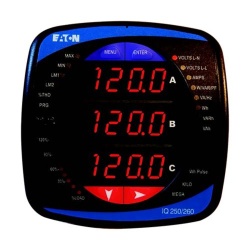
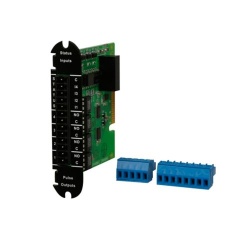
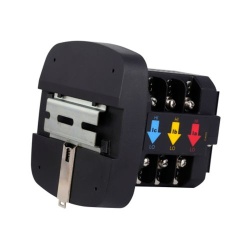
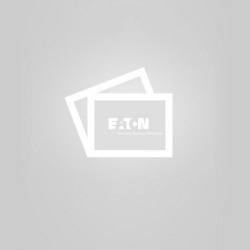
More Information about Eaton PLCs
With a platform, the XC300 shines in high-speed operations, making it one of the world's premier nano programmable logic controllers. The difference between a brick PLC and a modular PLC is that modular designs allow for scalable utilization, meaning businesses can expand their automation systems as needed. Eaton’s brick and modular PLC options ensure compatibility with various industrial settings, from simple temperature sensors limit switches to solid-state electronic devices that control complex machinery. Whether monitoring any industrial machineor optimizing things industrial controls, Eaton PLCs provide intelligent automation with CPU module input-outputconfigurations tailored to a range of applications.
PLCs
Programming Logic Controllers (PLCs) are industrial computer that are designed to monitor and control a series of inputs and outputs.
The program running the PLC evaluates the inputs, and changes the output signals based on the program response to the input signals. Several programming languages are available to program most PLCs. The most common of these is called ladder logic. Ladder logic is a visual programming language that evolved from relay logic diagrams, which visually look like ladders because they consist of two vertical rails with runs between them that contain programmed logic. While ladder logic is the most common programming language used within PLCs, there are others that are also common, including function block diagrams, structured text and sequential function charts.
The hardware included in a PLC includes: a CPU, memory, I/O connections, a power supply and a programming device.
The CPU is a microprocessor that acts as the brains of the PLC. It performs logic operations, controls instruction and performs various other tasks that help keep the PLC running effectively. The memory in a PLC allows data to be stored that is needed to run the program, as well as any data that is collected by the inputs. Depending on the the type of PLC, the section for I/O may have a fixed number of points or it may be modular, allowing for additional I/O to be added. Many PLCs require some type of power supply and it is common to see more modular based systems integrate the power supply. Lastly, the PLC provides a programming device that feeds the program into the PLC's memory, so that it can perform the desired operation. This is most commonly some type of computer.
The PLC is designed to run a program repeatedly over and over again, normally many times a second. Each time a program runs, the PLC goes through some very specific steps.
While the order and the specifics may vary from manufacturer to manufacturer, they all typically follow a pattern similar to the following:
The PLC performs internal self checks to make sure that it is functioning correctly.
The PLC reads the inputs that are connected to it. It will then store the status of each of those inputs in its memory.
The PLC will execute the program logic.
The PLC will write the new values to the hard wired outputs to match those determined during the program execution. At some point in the cycle, communication requests will also be processed.
Following the execution of the last step, the PLC will then cycle back to the beginning of the process and begin all over again.