- Antennas & Radios (Industrial)
- Batteries (Industrial)
- Breakers, Fuses & Circuit Protection
-
Cable, Wire & Assemblies
- Phoenix Contact Cables & Connectors
- Weidmuller Cables & Connectors
- Ericson Cables & Accessories
- Wire
- Ethernet Cable & Accessories
- Coax Cable & Accessories
- Fiber Optic Cables & Accessories
- Audio, Data & Video Cable & Accessories
- AC Power Cords
- Cable Reels
- Cordsets
- Bonding & Grounding
- Sensor Cables & Connectors
- Wire & Cable Accessories
- View All
- Connectors
-
Enclosures
- All Enclosures
- Steel Enclosures & Junction Boxes
- Stainless Steel Enclosures
- Non-Metallic Enclosures
- Aluminum Enclosures
- Commercial Enclosures
- Consolet Enclosures
- Disconnect Enclosures
- Hazardous Location Enclosures
- HMI Enclosure Systems
- Modular Enclosures
- Network Cabinets & Racks
- Push Button Enclosures
- Solar Enclosures
- Wire Management Wireways & Troughs
- View All
-
Enclosure Accessories
- Accessories for Specific Enclosure Models
- Enclosure Air Conditioners & Cooling
- Enclosure Backplates & Panels
- Enclosure Bases & Base Accessories
- Enclosure Cable Management
- Enclosure Corrosion Inhibitors
- Enclosure Door & Door Accessories
- Enclosure Floor Stands, Pedestals, Legs, & Casters
- Enclosure Lighting
- Enclosure Mounting, Hardware & Fasteners
- Enclosure Paint, Patch Kits & Hole Seals
- Enclosure Power Distribution & Grounding
- Enclosure Pressure, Humidity & Condensation
- Enclosure Racks & Rack Mounting
- Enclosure Rain Hoods & Drip Shields
- Enclosure Roof Plates & Canopies
- Enclosure Shelves, Drawers & Trays
- Enclosure Sun-Solar Shields
- Enclosure Thermal Management
- Enclosure Windows & Inspection Windows
- Data Interface
- View All
- Energy & Power Measurement
- Instrumentation
- Labels & Markings
- Lighting
- Motors & Motor Control
- Networking & Communication
- Operator Interface
- Panel Hardware
- Personal Protective Equipment
- PLCs & IO
- Plugs & Receptacles
- Power Supplies & Regulation
-
Push Buttons, Switches & Signaling Devices
- Push Buttons
- Indication & Signaling (Pilot Lights, Beacons, Audibles etc.)
- Selector Switches
- Foot Switches
- Control Stations
- Potentiometers
- Pendant Control Stations
- Biometric Switches
- Joysticks
- Light Switches & Wallplates
- Legend Plates for Switches, Push Buttons & Signaling Devices
- Push Button & Switch Accessories
- View All
- Relays, Timers & Counters
- Safety (Industrial)
- Security & Surveillance
- Sensors
- Signal & Power Conditioning
- Software Services
- Solar
- Structural Aluminum Framing
- Surge Protection & Filters
- Tapes & Adhesives
- Terminal Blocks & Connectors
- Tools & Supplies
- Towers & Direct Embedded Poles
PLCs & IO
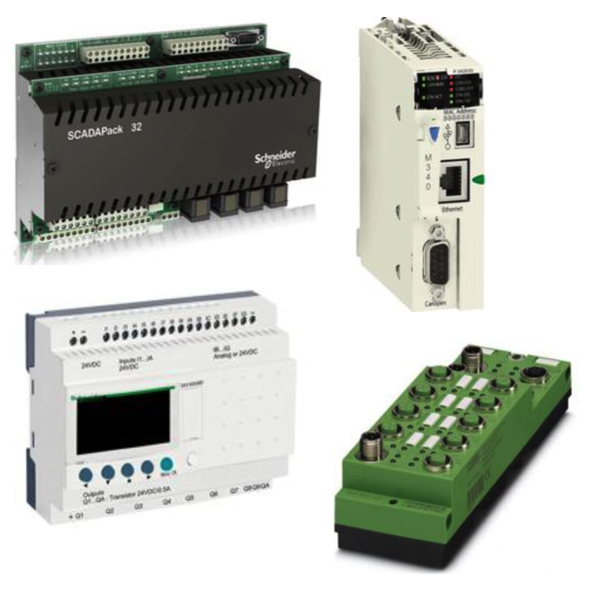
Programmable Logic Controllers (PLCs) are a type of industrial computer system that is used to control and automate processes in manufacturing, assembly lines, and other such industrial automation settings. PLCs are designed to be rugged and reliable, capable of operating in harsh environments with high levels of noise, vibration, and temperature. They consist of a central processing unit (CPU), input and output (I/O) modules, and a programming interface.
PLCs can be programmed to perform a wide range of control functions, such as monitoring sensors, controlling motors and other actuators, and executing logic-based instructions. They use a programming language based on ladder logic, which is similar to the electrical wiring diagrams used in traditional relay-based control systems.
I/O stands for Input/Output and refers to the process of transferring data to and from the PLC, which allows the PLC to receive input signals from sensors and other devices, and send output signals to control actuators and other devices. There are two main types of I/O modules used in PLC systems: digital and analog. Digital I/O modules are used to interface with devices that produce binary signals, such as on/off switches, push buttons, and proximity switches. Analog I/O modules, on the other hand, are used to interface with devices that produce continuous signals, such as temperature sensors, pressure sensors, and flow meters.
Subcategories
More Information about PLCs and IO
Input and Output modules
Input and output (I/O) modules are hardware components of a Programmable Logic Controller (PLC) system that interface with sensors, actuators, and other devices in order to receive input signals and send output signals.
Input Modules
Input modules are used to read signals from sensors and other devices and convert them into digital signals that the PLC can process. For example, an input module might be connected to temperature sensor or a limit switch, which sends a signal to the input module when a machine has reached a certain position in its cycle. The input module reads this signal and sends it to the PLC for processing.
Output Modules
Output modules, on the other hand, are used to send signals to control devices and actuators, such as motors and solenoids. For example, an output module might be connected to a motor that drives a conveyor belt, allowing the PLC to control the speed and direction of the conveyor.
Both input and output modules come in digital and analog versions. Digital modules are used for on/off signals and can only detect binary input signals (e.g., the limit switch is either open or closed). Digital output signals can turn a device on or off (e.g., an output signal can activate or deactivate a motor). Analog modules, on the other hand, can read or make discrete inputs and generate continuous signals (e.g., temperature, pressure, flow), which are useful for more precise control of a process.
Input and output modules can be easily swapped out or added to a PLC system as needed, allowing for flexible configuration and customization of the control system. The specific type and number of I/O modules needed will depend on the particular requirements of the process being controlled.
FAQs
What does an analog input module and analog output module do?
Analog input modules are designed to convert continuous analog signals from input devices such as sensors and other devices into digital signals that the PLC can process. Analog output modules are designed to convert digital signals from the PLC into continuous analog signals that can be used to control actuators and other devices.
What are discrete input modules and discrete output modules?
Discrete input modules are used to read digital signals from sensors and other devices that produce binary signals, such as limit switches, push buttons, and proximity sensors. Discrete output modules are used to send binary signals to control devices and actuators, such as solenoid valves, relays, and contactors.
PLCs vs Data Loggers
PLCs
Programming Logic Controllers (PLCs) are industrial digital computers that are designed for the control of electrical processes. These processes include any activity that requires high reliability, ease of programming and process fault diagnosis. PLCs are used to collect various types of data through the I/O portion of the PLC. The I/O or inputs and outputs, is where sensors and instruments can be wired into the PLC. This information on its own does not enable the function of the PLC. The PLC needs to be programmed. The programming language that is used will depend on the type of PLC that is selected. There are many different languages that can be used and some PLCs even allow for multiple languages to used on the same piece of hardware. With the program loaded onto the PLC it will then have the ability to read the various inputs and outputs, assist in storing the data it collects, send that data to an HMI or send output commands. The output commands can control things like valve actuation and on/off commands to relays and contactors. PLCs can perform complex tasks if the right kind of hardware is used, paired with the right programming.
Data Loggers
Data loggers, or data recorders, are electronic devices that record data over time. This data can be collected with a built in set of sensors or instruments, or with external sensors that can be connected to the data logger just like a PLC. One of the biggest differences between PLCs and data loggers is that data loggers don't typically require as much programming and are only intended to be used to collect data. One of the primary benefits of using data loggers is that they can automatically collect data over a 24 hour period. Once they have been properly configured, data loggers are deployed and left unattended to measure and record information for a specified time period. This allows for a comprehensive and accurate picture of the various conditions that can be monitored, such as air temperature or relative humidity. Data loggers almost always have some kind of internal memory for data storage. This is different from PLCs, which are not designed to store large amounts of data, but instead send that data to an over network connection or HMI.