
Distributed I/O
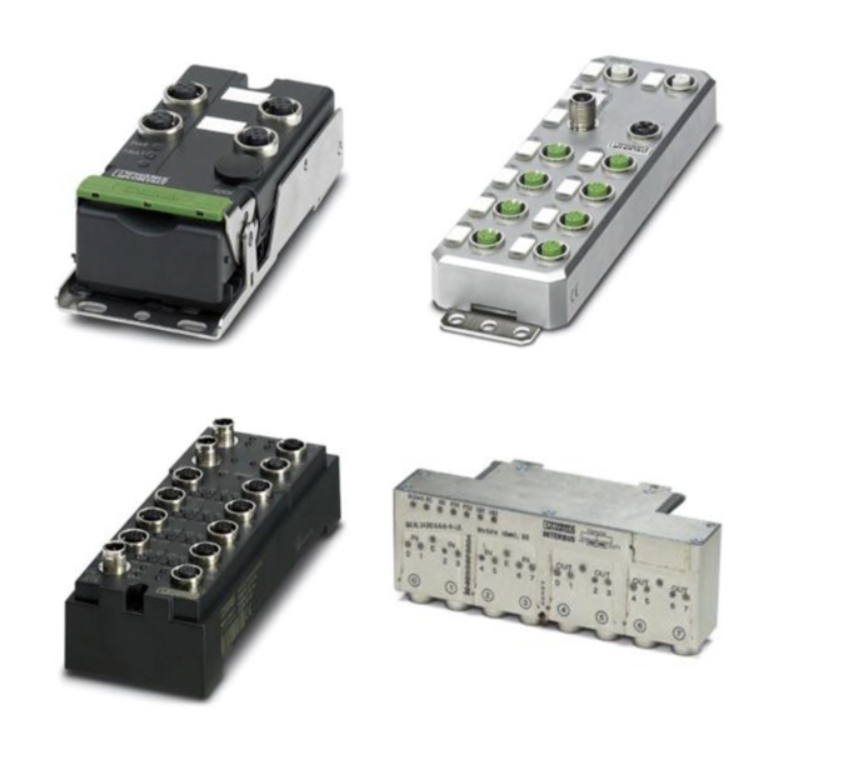
Distributed I/O systems are modular devices that provide digital and analog input and output signals. A digital output, for instance, might be a simple on/off command sent to a device. Meanwhile, analog output is signal handling with a breadth of values—ideal for something like temperature measurements. Field devices, like sensors and actuators, leading up to the distributed I/O modules, communicate the right signals to the control system. On the other hand, these I/O modules likewise receive the right kinds of signals from the field devices and make their way to the control system.
Distributed I/O systems are compact enough to be panel-mounted or mounted on a DIN rail inside control cabinets—so they’re out of harm’s way—yet they’re still accessible enough to serve as an interface with the outside world. These modules still exist in a technological landscape that’s evolving quickly. Enter the I/O Link, which is emerging as a standard for communication between controllers and field devices. That has led to, among other things, the emergence of the I/O Link Master and the direct connection of I/O Link-compatible sensors and actuators.
Products
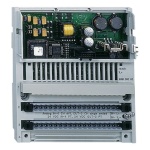
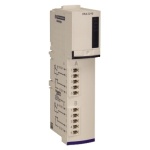
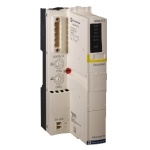
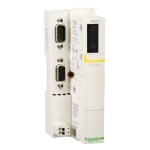
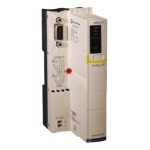
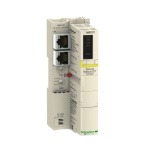
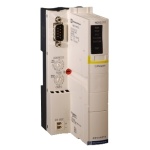
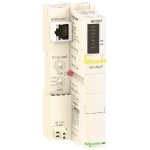
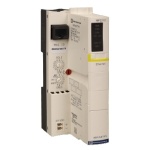
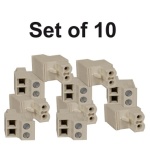
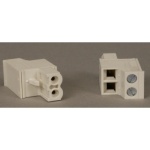
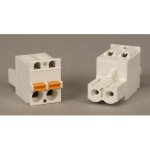
More Information about Distributed I/O
Some distributed I/O systems have another impressive characteristic: high density channel count. A single module can manage an almost unmanageable number of input and output signals. Where compactness was a design disadvantage in early I/O systems, today, increased channel density helps achieve system designs that are more compact and efficient. Distributed I/O has also come to mean innovative business models for machine builders and for automation specialists. Scalable to a ridiculous degree, these systems can be expanded or shrunk, their modular nature allowing for a design that handles the specific demands of the automation project at hand.
FAQs
Can distributed I/O connect multiple controllers in safety systems?
Yes, distributed I/O systems can connect multiple controllers, including those used in safety systems. In industrial automation, the ability to interconnect various controllers is crucial, especially in complex installations where redundant or specialized controllers might be necessary for different tasks.
Do distributed I/O modular devices provide a network adapter?
Yes, distributed I/O modular devices typically include a network adapter to enable seamless communication across industrial networks.
I/O
Digital Signals
Digital signals are represented in either a true or false. There is no gray area with digital signals. An example of this might be a light switch. A light switch is either on or off. Another example of this might be a motor that is running or not running. Digital signals can be generated with both AC and DC circuits with varying voltages, currents and resistance. Some practical examples of using digital signals in an industrial environment might be if a pump is running or not running or a whether a valve is open or closed.
Analog Signals
Analog signals convey information in the form of a range. A light switch might be on or off as a digital signal, but a dimmer switch would be an analog signal. It can be on or off, but it can also be somewhere in between. A practical example of using analog signals in an industrial environment would be if there is a need to measure the level of a tank; whether it's full, empty or somewhere in between. Analog signals can take many different forms with some of the more common being a 4 to 20 milliamp signal or a 0 to 5 or 0 to 10 volt signal.
Output Signals
Output signals send data out and can be either analog or digital. For example, a digital output could be a run command to a motor. In this case, a signal would be sent that tells a motor to either start or stop. An analog output could be sent to control the speed of that motor, since analog signals have the ability to control a range of values.
Inputs Signals
Inputs signals are received data from either a digital or analog source. Just like with output signals, inputs can be either digital (which would tell if a motor is running or a door has been opened) or analog (which would be able to tell if the pressure in a pipe is too high or what the level in a water tank is).