
Vertical Motors

The vertically installed electric motor is a specialized type of motor used in applications where the motor must be mounted vertically. Such motors find common use in many pump applications, especially when the pumps are for deep wells and water treatment, and are also found in heating, ventilation, and air conditioning systems, and other industrial processes wherein vertical space optimization is vital. These types of motors handle the thrust load that comes from the impellers in the pump to ensure not just adequate but also reliable system performance. They do this while providing power to the impellers at optimal levels—both axially and radially.
There are several ways to configure vertical motors, but two basic designs predominate: hollow shaft and solid shaft. Both types of motors are used in many different applications—aerospace, automotive, pharmaceuticals, food processing—wherever a motor is needed to drive something. Whether an application requires a hollow-shaft or solid-shaft motor often boils down to how the pump's shaft must connect to and operate within the motor.
Products
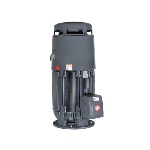
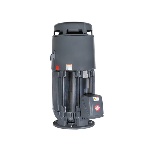
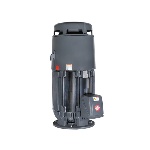
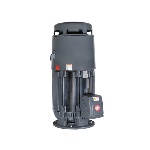
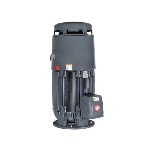
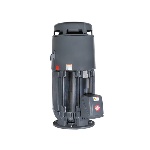
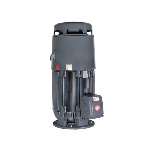



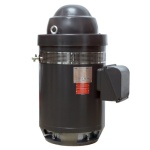

FAQs
What API standards does a totally enclosed fan cooled vertical motor follow?
A totally enclosed fan cooled vertical motor typically follows API standards such as API 610 for centrifugal pumps and API 541 for form-wound motors used in the petroleum, chemical, and gas industries.
Is high thrust a required feature for vertical motors to operate in the water treatment industry?
Yes, high thrust is a required feature for vertical motors to operate effectively in the water treatment industry, as they need to handle the significant axial loads generated by deep well and other vertical pumping applications.
Motor Starters, Soft Starters and VFDs
Motor Starters
Motor starters safely start and stop a motor in industrial applications. They are designed with a contactor, overload and circuit protection. They are used when basic motor control is required, where torque on the motor is not a concern and speed control is not needed. The advantages of motor starters include: lower cost, allows for remote operation, allows for monitoring of motor state (with the use of auxiliary contacts) and they are safe and efficient. The disadvantages include: high inrush current that can cause fuses to blow and breakers to trip if the inrush is too high, and the starter will allow a full torque to start the motor which can cause the motor to ramp up to full speed very quickly potentially causing the motor to wear and degrade prematurely.
Soft Starters
Soft starters protect motors from inrush current by gently ramping up the motor to full speed. They provide all of the same functions as a traditional motor starter. The advantages of soft starters include: they are less expensive than a VFD when only startup control is needed, they are a smaller system than a VFD where space is a concern and they prevent unwanted torque upon startup, prolonging the life of the motor. The disadvantages include: they are more expensive than a traditional motor starter and they do not allow for full speed control.
VFDs
A Variable Frequency Drive (VFD) allows for the slow ramp up of a motor during startup and the slowing down of the motor during shutdown. It also allows for full speed control during the entire run cycle of the motor. VFDs provide the same functions as both the traditional motor starters and soft starters. The advantages of VFDs include: full speed control (start, stop and in-between), more custom control and monitoring, energy savings due to efficient motor usage and less wear and tear on the motors. The disadvantages include: they are more expensive and larger than other motor control options and they generate heat that may require fans or AC units.