
Starter Overload Relays
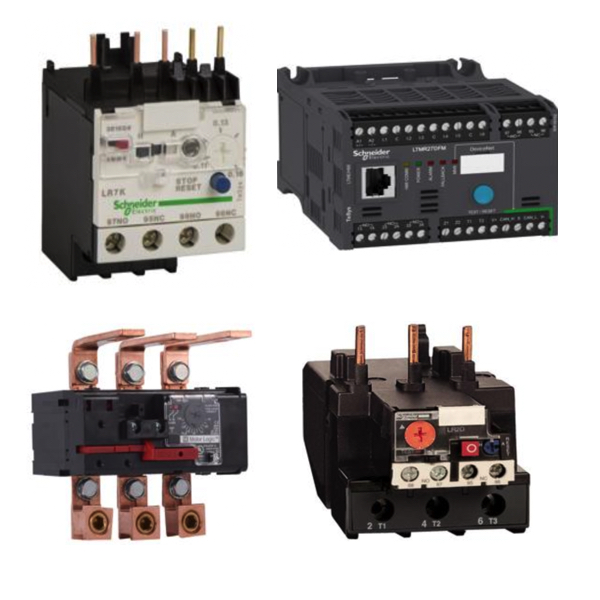
The starting overload relay is an essential part of a motor control system and provides protection against excessive currents of both immediate and long duration. It operates in conjunction with the motor starter and contactor to ensure the safe and reliable operation of motors, running at all sorts of loads even under less-than-ideal conditions.
The types of overload relays found today include IEC overload relays and electronic overload relays. The former are used in order to protect against overcurrent conditions, while the latter can sense more types of anomalies, including phase loss. Either way, these relays provide an added level of safety for motors and other equipment operating in a circuit together with them.
Typically installed in series with the motor circuit, and often mounted directly on the motor starter or control panel, is the overload relay. It watches the current flowing through the motor and turns on a protection action when that current increases above a set threshold. This can shut off whatever circuit supplies power to the motor (closing an electromagnetic switch or opening contactors) or send a signal telling whatever monitoring device there is that it should make the motor stop operating safely.
Subcategories
Products
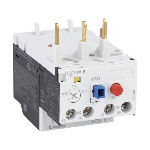
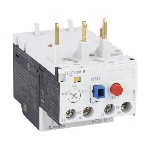
FAQs
What communications capabilities do three phase motor overloads have to provide overload protection and phase loss protection to motors?
Three-phase motor overloads often have communications capabilities such as Modbus, Profibus, or Ethernet/IP, allowing them to provide real-time data on motor performance, fault conditions, and protection status to centralized control and monitoring systems.
What role does a heater element and a ratchet wheel play in an overload relay's ability to provide protection to motors?
In an overload relay, the heater elements generates heat proportional to the motor's current, causing the ratchet wheel to move and eventually trip the relay if the current exceeds safe levels, thus protecting the motor from overheating.
Motor Control Basics
Motor control allows operational control of electrical motors in various environments.
Motor control circuits provide a safe way to operate electrical motors. Back when motor control circuits were in their infancy, it would have been common to see a simple disconnect switch that would be used to turn on and off a motor. Depending on the size of the motor and how much voltage was required, operating this disconnect would have been dangerous, with a very high possibility of arcing or electrocution. Not to mention that when the disconnect was actuated, the large amount of inrush current would have damaged the motor over time.
In today's motor control circuits, there are a few common pieces of hardware.
A circuit breaker is used to protect the motor and any hardware downstream. A contactor and an overload relay are connected together and function in tandem to allow for remote and safe operation of the motor. The contactor functions much like a relay, allowing for a smaller electrical circuit to remotely close the motor contacts, starting the motor. The overload relay is designed to protect the motor in the case of a prolonged overcurrent event. These two devices are wired in series, so that if the overload relay detects an overcurrent event, the contactor will open the motor contacts, shutting off power to the motor.
The other two most common types of motor control hardware are a soft starter and a Variable Frequency Drive (VFD).
Both of these devices function in a similar way to the motor circuit with some added functions. The soft starter is designed to reduce large inrush current to the motor upon startup. This “soft starting” of the motor will prolong its life and allow for safer operation. The VFD performs the soft start functions, but also allows for speed control of the motor. This speed control is critical in many different environments and has made VFDs one of the most common and safe to use motor control circuits today.