
Enclosure Cable Management

Cable management is essential in creating an organized and accessible environment for cables and wires inside a server rack or enclosure. Proper cable management helps prevent damage, low performance issues, and difficulty in maintenance and completing simple tasks.
Enclosure cable managers protect and organize cables, reduce signal interference and facilitate airflow. Horizontal cable managers secure and organize cables that go to the front or rear of a server rack or enclosure. The horizontal cable manager is placed above or below the device where the cables are plugged into and each cable is kept in place and separated by D-rings or other support options. Vertical cable managers secure and organize cables in a vertical pathway in a server rack or enclosure. The vertical cable manager is installed on the inner sides of an enclosure, saving space and allowing cables to bend safely when exiting.
Subcategories
Products
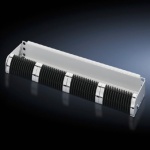
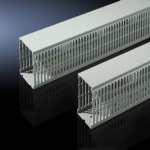

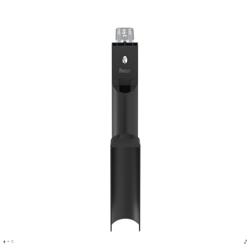
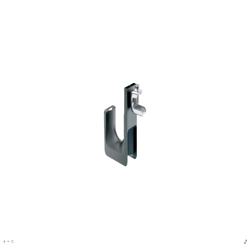
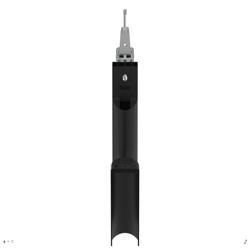
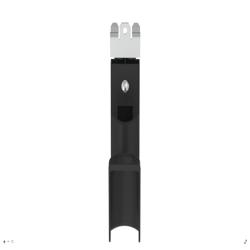
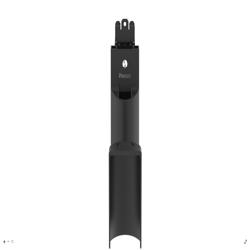
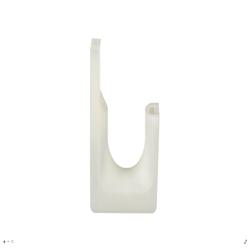
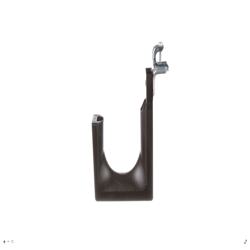
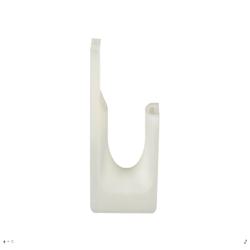
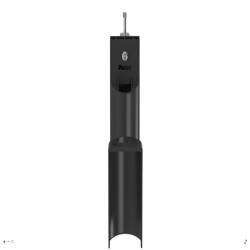
More Information About Cable Management
Wire duct are rigid trays that allow cables and wires to be re-routed and terminated within an enclosure. Slotted wire ducts have slots or fingers that can easily be broken away in various places to customize the wire slot size for thicker cables or bundles of cables. Slotless or unslotted wire ducts are solid and do not have slots or fingers. They provide better cable protection where cables are infrequently accessed.
Wireways are a metallic or non-metallic trough with a removable or hinged cover designed to protect cables from contaminants such as dirt, dust, moisture and oil. They can be mounted to ceilings, walls or secured under-floor.
Cable tray systems can be mounted to ceilings or under-floor for routing of cables. Wire mesh cable trays can be customized to fit the needs of a particular application by simply cutting and bending. The wide open design allows frequent entry and exit of cables and allows airflow for heat dissipation.
Ladder rack systems have two side rails connected by cross bars or “rungs” which allow air circulation around the cables, dissipating heat. The rungs of the ladder cable tray provide anchors for attaching and tying down cables. Ladder cable trays can have covers installed to protect the cables from falling water, dust or debris.
Control Panel Fabrication: Best Practices
Use a larger enclosure whenever possible.
This allows room in the panel design to properly space all of the hardware and to install larger wire ducting. Panels that have ample space tend be me more organized, while panels that have everything crammed into a small space tend to be more difficult to work in and are often less organized.
Tap holes instead of using self-tapping screws.
It is common for panel builders to use self-tapping screws to save time during the fabrication process. While it can save time, this type of fastener does not always provide the consistent, strong connection that may be needed for the mounted hardware. This is especially true when hardware may need to be removed at some point and then later reattached. Holes that have been tapped prior to hardware installation will offer a stronger, more consistent connection point that will last longer.
Ensure that wire ducting is large enough.
It is very easy to undersize wire ducting when designing a panel. It is important to always plan for wire ducting to have extra room available once all wires have been run through it, including field wires.
When in doubt, label it.
It is a very good practice to label wires in a control panel, but it is not always required to label the other types of hardware in the panel to meet code. It is important to understand that any operators that may access this panel at a later date may not understand what the hardware in the panel is intended for. To make the panel is as safe as possible, and to allow operators to function in the panel more efficiently, it is a good idea to label everything that may come into question.