
Brake Motors
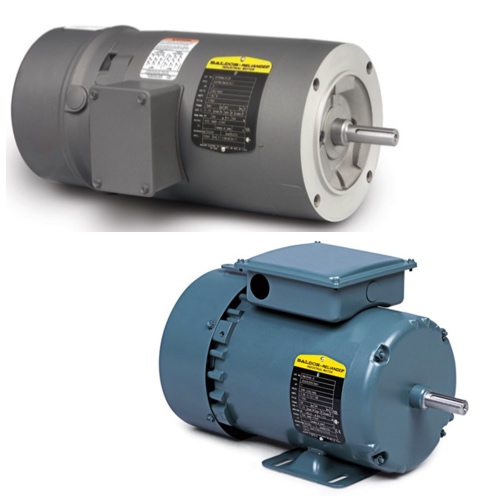
Braking motors are specialized motors that provide controlled stopping and holding capabilities in industrial applications where precise control and extra safety are needed. When power is removed, a brake mechanism that is automatically engaged ensures that the load is held securely in place. The brake motor is totally enclosed fan-cooled, making it safe to use in a variety of industrial environments. Brake motors are used where hard work is the order of the day and controlled stopping and starting are crucial to reducing downtime and increasing operational efficiency.
Selection of the proper brake motor for an application hinges on such aspects as torque, conditions of the environment, and the compatibility of the control system. Torque itself can be broken down into static and dynamic requirements, both of which the motor must satisfy. The static requirement is for starting torque; the dynamic requirement arises when the motor is coming to a stop. Clearly a motor that is not properly sized for these two functions could not serve its intended purpose.
Products
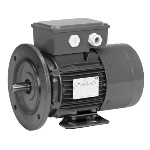
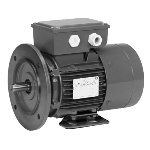
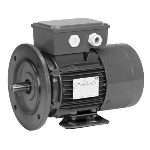
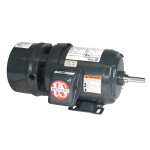








More Information about Brake Motors
Brake motors are high-performance operations with minimal maintenance that are not only ideal but also necessary for a few demanding applications. With many models coming equipped with a rectifier for efficient brake operation, their C-face mounting enables flexible installation. They operate reliably over long periods in three common situations: manufacturing, automation, and material handling—plenty of applications that demand a motor with a strong frame and easy access to wiring for installation and servicing.
FAQs
What is the frame size of a single phase brake motor?
The frame size of a single-phase brake motor typically ranges from 56 to 215T, depending on the specific application and power requirements.
Does the compact design of inverter duty brake motors make them ideal for cranes and hoists?
Yes, the compact design of inverter duty brake motors makes them ideal for cranes and hoists, as it allows for easy integration while providing precise control, enhanced safety, and reliable load handling.
What is a service factor and is it one of the essential features of brake motors?
A service factor is a multiplier that indicates the extra capacity a motor can handle beyond its rated power without overheating or damaging components, and it is an essential feature of brake motors, ensuring reliability and durability in demanding industrial applications.
Motor Starters, Soft Starters and VFDs
Motor Starters
Motor starters safely start and stop a motor in industrial applications. They are designed with a contactor, overload and circuit protection. They are used when basic motor control is required, where torque on the motor is not a concern and speed control is not needed. The advantages of motor starters include: lower cost, allows for remote operation, allows for monitoring of motor state (with the use of auxiliary contacts) and they are safe and efficient. The disadvantages include: high inrush current that can cause fuses to blow and breakers to trip if the inrush is too high, and the starter will allow a full torque to start the motor which can cause the motor to ramp up to full speed very quickly potentially causing the motor to wear and degrade prematurely.
Soft Starters
Soft starters protect motors from inrush current by gently ramping up the motor to full speed. They provide all of the same functions as a traditional motor starter. The advantages of soft starters include: they are less expensive than a VFD when only startup control is needed, they are a smaller system than a VFD where space is a concern and they prevent unwanted torque upon startup, prolonging the life of the motor. The disadvantages include: they are more expensive than a traditional motor starter and they do not allow for full speed control.
VFDs
A Variable Frequency Drive (VFD) allows for the slow ramp up of a motor during startup and the slowing down of the motor during shutdown. It also allows for full speed control during the entire run cycle of the motor. VFDs provide the same functions as both the traditional motor starters and soft starters. The advantages of VFDs include: full speed control (start, stop and in-between), more custom control and monitoring, energy savings due to efficient motor usage and less wear and tear on the motors. The disadvantages include: they are more expensive and larger than other motor control options and they generate heat that may require fans or AC units.