
Starter Contactor Accessories
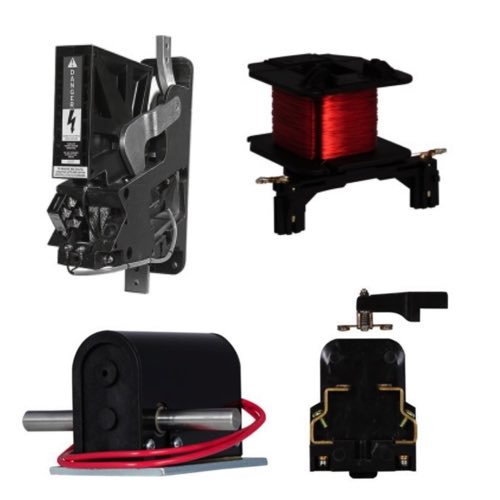
Starter contactor accessories boost the functionality and service life of starter contactor products. They're designed to meet the particular demands of motor control applications, which make them suitable for a wide range of industrial situations. One thing these starter accessories do is allow auxiliary contacts to be fitted—something that gives remote indication and monitoring not just of the starter contactor's operation but also of an attached load (i.e., a motor).
Starter contactors have two types of accessories: auxiliary contacts and overload relays. The purpose of these accessories is not the same. The first one, the auxiliary contact, provides additional output for other devices connected to it. So when the main contact accomplishes its task of connecting and disconnecting a circuit, the aux contact does exactly the same thing. They work in tandem with each other to sequence multiple devices that need to be turned on and off in a specific order because they might share common wires or otherwise interact with each other in some way.
Starter contactor surge suppressors, also known as starters and motor control systems (MCSs), provide protection for a wide range of electrical equipment from voltage surges and transient overvoltages. This is critical because these types of events can easily occur due to the operation of motors—a fact that highlights the importance of using high-quality surge protectors.
Products
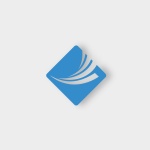
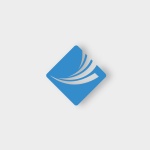
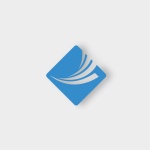
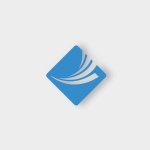
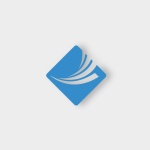
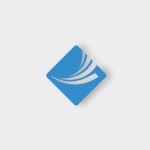
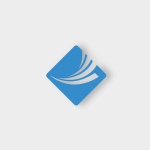
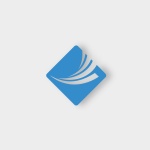
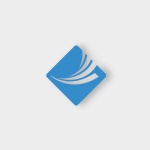
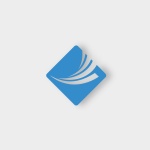
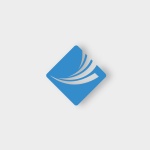
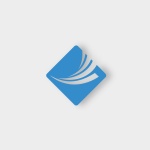
FAQs
Does the manufacturer or brand matter when I shop for starter contactor accessories?
Yes, the manufacturer or brand matters when shopping for starter contactor accessories, as it ensures compatibility, quality, and best results with your existing equipment.
What type of filters and buttons are found in starter contactors?
Starter contactors typically include filters for reducing electromagnetic interference (EMI) and surge protection, as well as control buttons such as start, stop, and reset buttons for manual operation and fault management.
Motor Control Basics
Motor control allows operational control of electrical motors in various environments.
Motor control circuits provide a safe way to operate electrical motors. Back when motor control circuits were in their infancy, it would have been common to see a simple disconnect switch that would be used to turn on and off a motor. Depending on the size of the motor and how much voltage was required, operating this disconnect would have been dangerous, with a very high possibility of arcing or electrocution. Not to mention that when the disconnect was actuated, the large amount of inrush current would have damaged the motor over time.
In today's motor control circuits, there are a few common pieces of hardware.
A circuit breaker is used to protect the motor and any hardware downstream. A contactor and an overload relay are connected together and function in tandem to allow for remote and safe operation of the motor. The contactor functions much like a relay, allowing for a smaller electrical circuit to remotely close the motor contacts, starting the motor. The overload relay is designed to protect the motor in the case of a prolonged overcurrent event. These two devices are wired in series, so that if the overload relay detects an overcurrent event, the contactor will open the motor contacts, shutting off power to the motor.
The other two most common types of motor control hardware are a soft starter and a Variable Frequency Drive (VFD).
Both of these devices function in a similar way to the motor circuit with some added functions. The soft starter is designed to reduce large inrush current to the motor upon startup. This “soft starting” of the motor will prolong its life and allow for safer operation. The VFD performs the soft start functions, but also allows for speed control of the motor. This speed control is critical in many different environments and has made VFDs one of the most common and safe to use motor control circuits today.