
Interface Modules
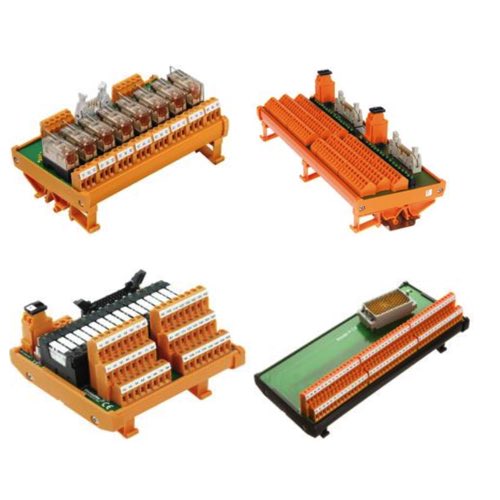
Interface modules bridge the gap between devices and control systems. They perform signal transmission between the electrical systems and perform several vital functions, including that of a translator for signals sent between devices that use different communication protocols. Modules typically interpret a signal from one device and reformat it so that another device can understand it. For example, in a system where a computer and a programmable logic controller (PLC) are trying to communicate, the interface module would make sure that both devices understood the signals being sent.
In industrial environments, intricate wiring systems are simplified and reduced in size because of interface modules, which fit very well into control panels. This is especially advantageous in the wiring-tight situations that some applications require, where high-density wiring is needed and space is at a premium. The modules are designed to be easy to install and maintain and are broadly usable in many situations, from simple on-off control to multipoint process control. They plug together easily and offer about as much functionality as a designer might want.
Products


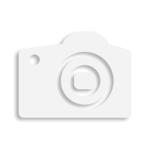









More Information about Interface Modules
Interface modules connect electronics to electrical systems at the control level and perform signal transmission and distribution in the control and field levels (system, machine) and vice versa. Diode modules in interface technology are used for signal isolation, polarity protection, and controlled signal flow within electrical systems, ensuring reliable and safe operation.
What is the typical number of channels that an interface module has?
The typical number of channels an interface module has can range from 1 to 16 or more, depending on the application and design requirements.
PLCs vs Data Loggers
PLCs
Programming Logic Controllers (PLCs) are industrial digital computers that are designed for the control of electrical processes. These processes include any activity that requires high reliability, ease of programming and process fault diagnosis. PLCs are used to collect various types of data through the I/O portion of the PLC. The I/O or inputs and outputs, is where sensors and instruments can be wired into the PLC. This information on its own does not enable the function of the PLC. The PLC needs to be programmed. The programming language that is used will depend on the type of PLC that is selected. There are many different languages that can be used and some PLCs even allow for multiple languages to used on the same piece of hardware. With the program loaded onto the PLC it will then have the ability to read the various inputs and outputs, assist in storing the data it collects, send that data to an HMI or send output commands. The output commands can control things like valve actuation and on/off commands to relays and contactors. PLCs can perform complex tasks if the right kind of hardware is used, paired with the right programming.
Data Loggers
Data loggers, or data recorders, are electronic devices that record data over time. This data can be collected with a built in set of sensors or instruments, or with external sensors that can be connected to the data logger just like a PLC. One of the biggest differences between PLCs and data loggers is that data loggers don't typically require as much programming and are only intended to be used to collect data. One of the primary benefits of using data loggers is that they can automatically collect data over a 24 hour period. Once they have been properly configured, data loggers are deployed and left unattended to measure and record information for a specified time period. This allows for a comprehensive and accurate picture of the various conditions that can be monitored, such as air temperature or relative humidity. Data loggers almost always have some kind of internal memory for data storage. This is different from PLCs, which are not designed to store large amounts of data, but instead send that data to an over network connection or HMI.