
Wire Duct
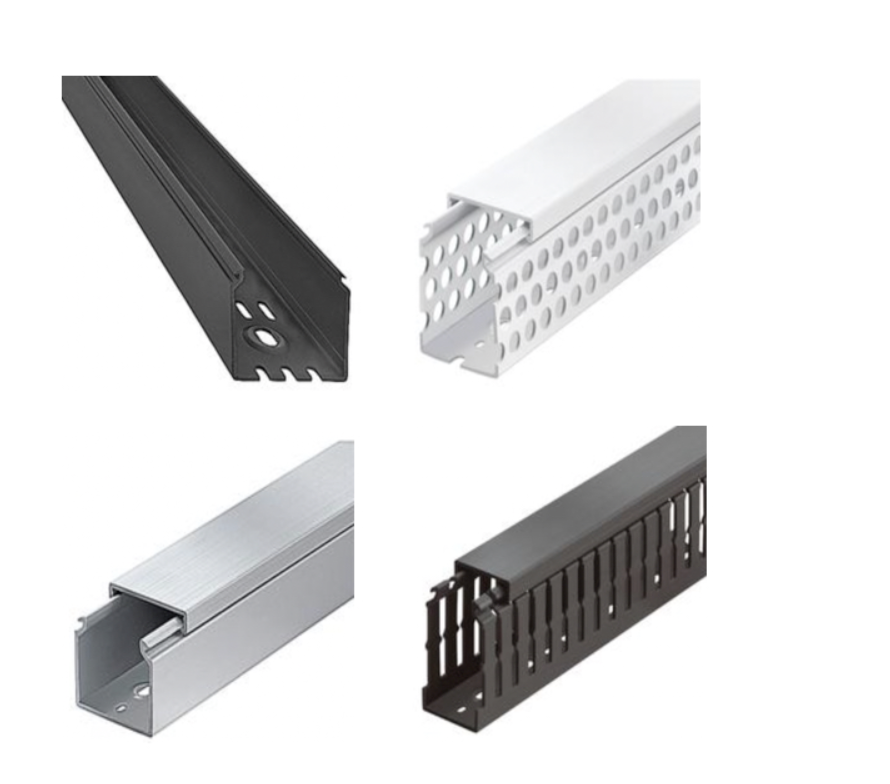
An essential part of any electrical enclosure that houses wires and cables, wire duct organizes and routes them in a neat and efficient way. It comes in different widths and lengths to fit various install base requirements. It is available in several colors, including gray and white, that improve the chances of making successful visual identifications of the contained wiring. In terms of durability, wire duct is rock solid. There are also ample opportunities for customization using cover options that visually maintain the line of sight to the contained wiring; using solid wall wiring duct for that part of the install, however, is a good first step.
Wire duct's slot design allows for easy wire installation and future changes, making it flexible. Narrow slot wiring duct has a restricted slot design that offers precise openings. They can be used to manage wires and cables. When you need to re-route cables, you can do it easily and neatly with narrow slot duct. You can use cable ties in conjunction with duct to keep the wires secure and maintain the appearance of orderliness. The duct (and, therefore, the wires) has been certified. It was put through performance tests, and it passed. You can use duct (and the wires it contains) in various types of industrial and commercial applications. It comes in several sizes. You can select the size based on your need.
Subcategories
Products
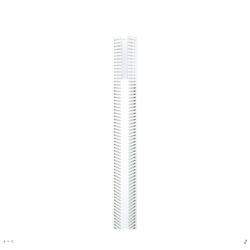
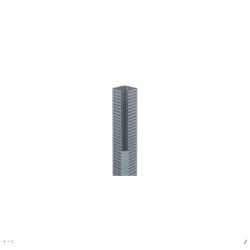
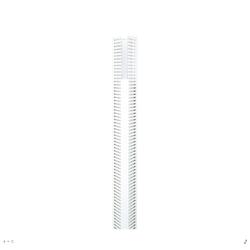
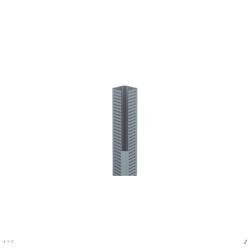
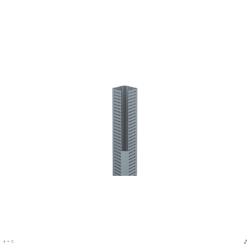
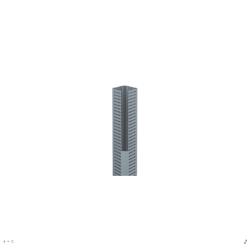
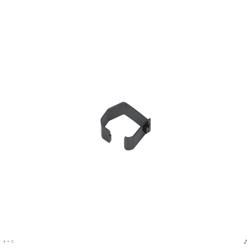
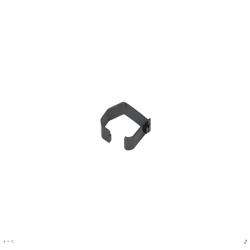
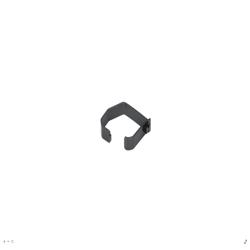
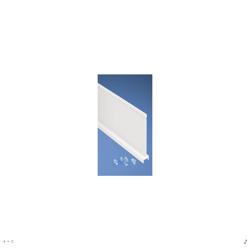
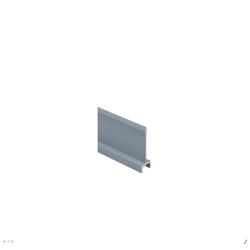
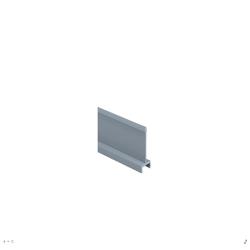
FAQs
Is wire duct a method of cable management that allows electrical wiring to be protected while improving safety and functionality?
Yes, wire duct is a method of cable management that protects electrical wiring while enhancing safety and functionality.
Can terminated wires be re-routed easily using manufactured wire duct?
Yes, terminated wires can be re-routed easily using manufactured wire duct, especially with slotted designs that provide convenient access and flexibility for adjustments.
4 Best Practices When Fabricating a Control Panel
Use a Larger Enclosure Whenever Possible
This allows room in the panel design to properly space all of the hardware and to install larger wire ducting. Panels that have ample space tend be me more organized, while panels that have everything crammed into a small space tend to be more difficult to work in and are often less organized.
Tap Holes Instead of Using Self-Tapping Screws
It is common for panel builders to use self-tapping screws to save time during the fabrication process. While it can save time, this type of fastener does not always provide the consistent, strong connection that may be needed for the mounted hardware. This is especially true when hardware may need to be removed at some point and then later reattached. Holes that have been tapped prior to hardware installation will offer a stronger, more consistent connection point that will last longer.
Ensure that Wire Ducting is Large Enough
It is very easy to undersize wire ducting when designing a panel. It is important to always plan for wire ducting to have extra room available once all wires have been run through it, including field wires.
When in Doubt, Label it
It is a very good practice to label wires in a control panel, but it is not always required to label the other types of hardware in the panel to meet code. It is important to understand that any operators that may access this panel at a later date may not understand what the hardware in the panel is intended for. To make the panel is as safe as possible, and to allow operators to function in the panel more efficiently, it is a good idea to label everything that may come into question.