
Safety PLCs
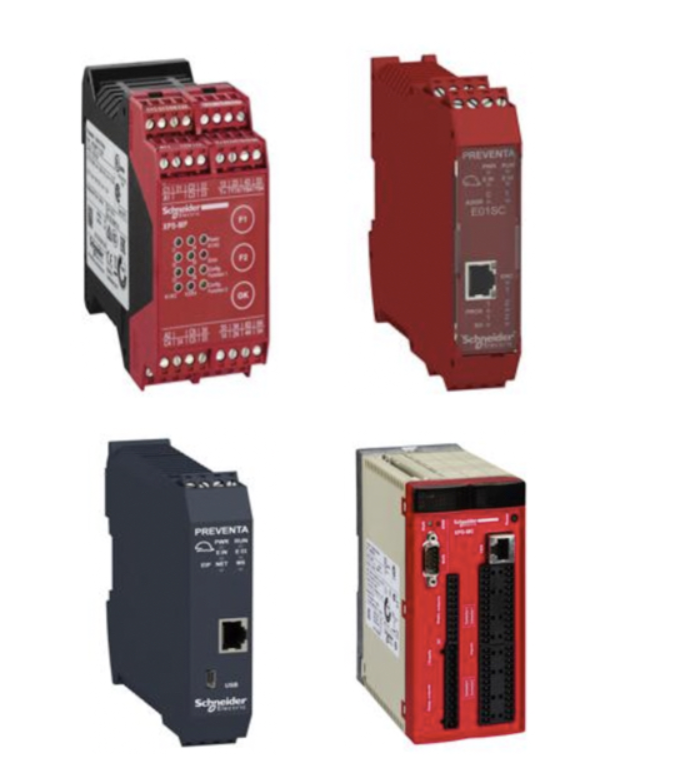
Safety PLCs, or safety programmable logic controllers, are specialized devices used in safety systems to enhance functional safety in industrial environments. These safety devices are designed to keep processes safe and to make sure that, even in high-risk situations, operations continue as intended. Safety PLCs are situated at the heart of a safety program which relies on layers of protection to deal with the dangers that can arise from equipment failures or faulty conditions. These controllers are part of a system that achieves a particular safety integrity level—SIL, for short—and they function in a way that makes sure that all of us can comply with some pretty strict standards related to safety.
Safety PLCs are not your average PLCs. They possess some advanced features—like program flow control and well-designed diagnostics—that help keep them from failing and make them act in a way that's consistent with system integrity. And safety controllers are capable of identifying a number of serious issues—like internal faults and corrupted programs—that could easily get a normal PLC into some kind of trouble. When a safety controller identifies a serious problem, a built-in response mechanism ensures that the system transitions into some kind of safe state. Of course, safety relays, safety sensors and safety PLCs aren't the only components in an industrial safety architecture. Still, if you have a safety application, redundancy and state transition logic in your safety PLC make it an indispensable component.
Products
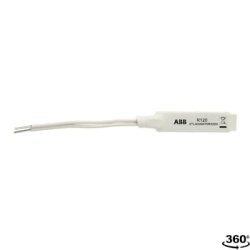
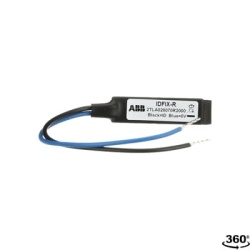
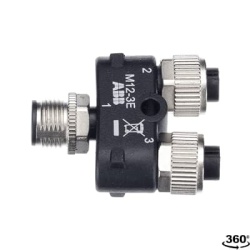
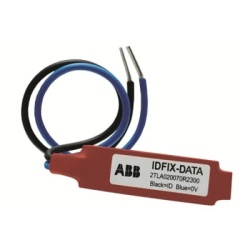
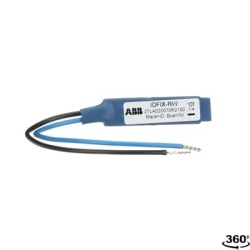
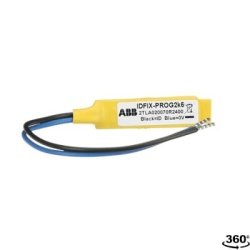
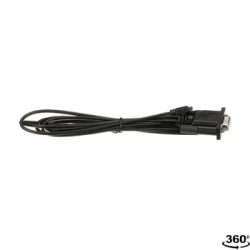
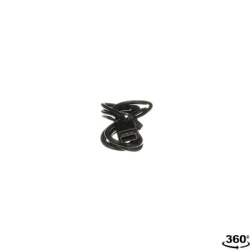
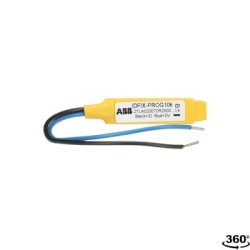
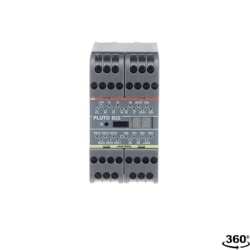
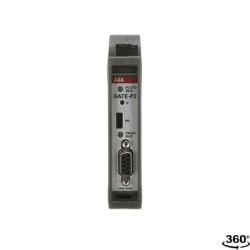
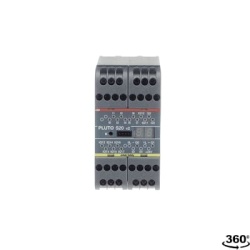
More Information about Safety PLCs
Plenty of advantages come from the use of safety PLCs in many different sectors—counted among these are the sectors of manufacturing, energy, and oil and gas. Safety PLCs monitor and detect faults in a way that is so reliable and efficient that such monitoring and detection are actually called "safety functions." Only when a system achieves what are called "satisfactory safety performance levels" can it be said to live up to the kind of "safety integrity" that is necessary for even the simplest of industrial operations to protect the humans and the property involved.
FAQs
What is a Safety Integrity Level (SIL) in a safety instrumented system?
A Safety Integrity Level (SIL) is a measure of the reliability and effectiveness of a safety instrumented system in reducing risk, with each specific safety integrity level (ranging from SIL 1 to SIL 4) representing an increasing degree of risk reduction and reliability required for specific safety functions in hazardous operations.
How does safety logic help prevent potential failures in automated processes?
Safety logic helps prevent potential failures in automated processes by continuously monitoring inputs, detecting anomalies, and executing predefined actions to transition systems into a safe state, thereby mitigating risks and ensuring process integrity.
What are the integrated safety functions of safety PLCs?
The integrated safety functions of safety PLCs include integrated motion control, safety relays, safety instrumented systems, program flow control, functional safety monitoring, redundancy, diagnostics, and failure prevention to ensure compliance with specific safety integrity levels in automated processes.
PLCs
Programming Logic Controllers (PLCs) are industrial computer that are designed to monitor and control a series of inputs and outputs.
The program running the PLC evaluates the inputs, and changes the output signals based on the program response to the input signals. Several programming languages are available to program most PLCs. The most common of these is called ladder logic. Ladder logic is a visual programming language that evolved from relay logic diagrams, which visually look like ladders because they consist of two vertical rails with runs between them that contain programmed logic. While ladder logic is the most common programming language used within PLCs, there are others that are also common, including function block diagrams, structured text and sequential function charts.
The hardware included in a PLC includes: a CPU, memory, I/O connections, a power supply and a programming device.
The CPU is a microprocessor that acts as the brains of the PLC. It performs logic operations, controls instruction and performs various other tasks that help keep the PLC running effectively. The memory in a PLC allows data to be stored that is needed to run the program, as well as any data that is collected by the inputs. Depending on the the type of PLC, the section for I/O may have a fixed number of points or it may be modular, allowing for additional I/O to be added. Many PLCs require some type of power supply and it is common to see more modular based systems integrate the power supply. Lastly, the PLC provides a programming device that feeds the program into the PLC's memory, so that it can perform the desired operation. This is most commonly some type of computer.
The PLC is designed to run a program repeatedly over and over again, normally many times a second. Each time a program runs, the PLC goes through some very specific steps.
While the order and the specifics may vary from manufacturer to manufacturer, they all typically follow a pattern similar to the following:
The PLC performs internal self checks to make sure that it is functioning correctly.
The PLC reads the inputs that are connected to it. It will then store the status of each of those inputs in its memory.
The PLC will execute the program logic.
The PLC will write the new values to the hard wired outputs to match those determined during the program execution. At some point in the cycle, communication requests will also be processed.
Following the execution of the last step, the PLC will then cycle back to the beginning of the process and begin all over again.