
Phoenix Contact PLCs
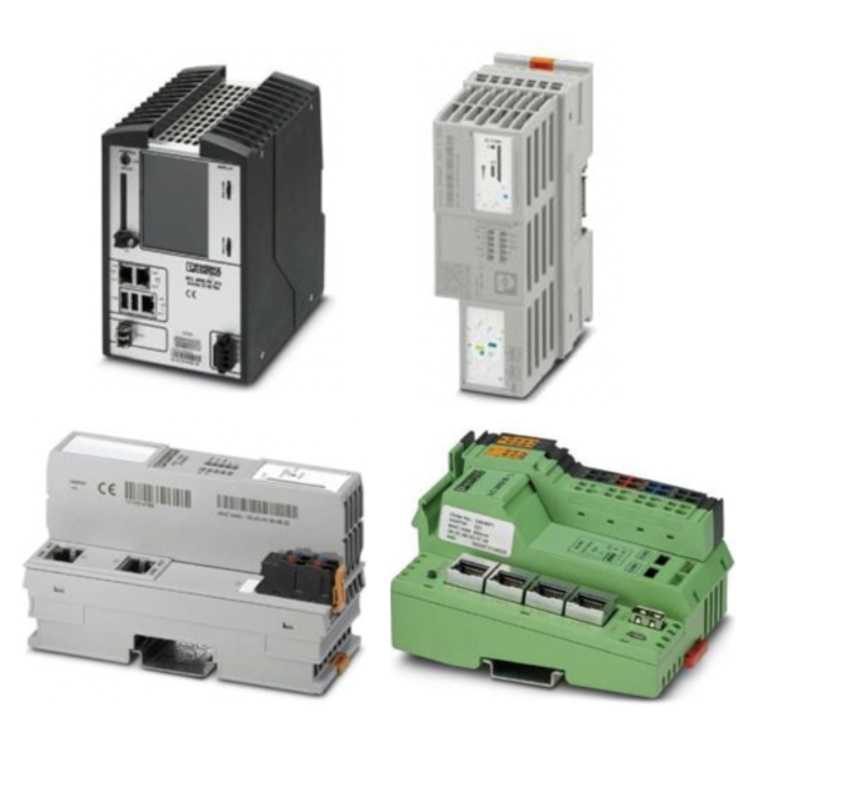
Phoenix Contact programmable logic controllers (PLCs) work in both simple and complex automation applications, ensuring reliable real-time data processing and controlling across a multitude of connected devices. With integrated communication interfaces and a high degree of connectivity, these PLCs find open opportunities across a range of networked tasks, from simple remote monitoring to more intricate process control. One of the few truly free programming environments on the market, the PLCnext Engineer software is built around an uncomplicated user interface that makes the work of configuring and programming the Phoenix Contact PLCs almost child's play.
These programmable logic controllers also place a premium on durability and reliability, with some models practically immune to tough industrial conditions. Phoenix Contact PLCs are built for long-term use in such demanding sectors as manufacturing, energy management, and logistics. A well-nigh infinite range of options to customize both input and output guarantees that the PLC can serve with precision in controlling the myriad kinds of machinery and industrial processes with which its path may cross. Enhancing operational efficiency, reducing downtime.
Subcategories
Products
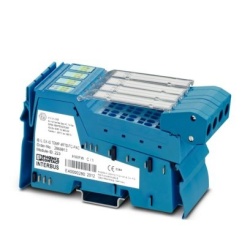
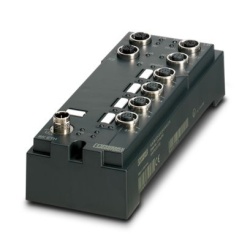
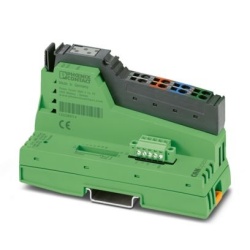

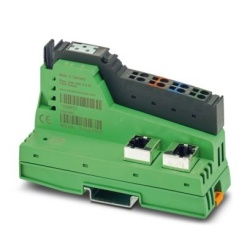
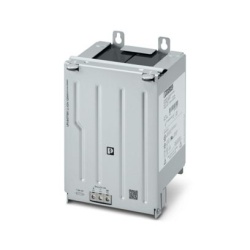
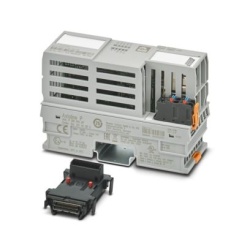
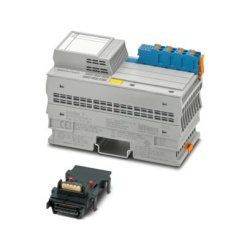
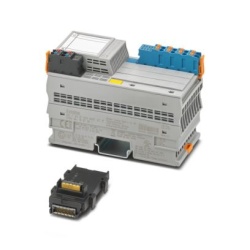
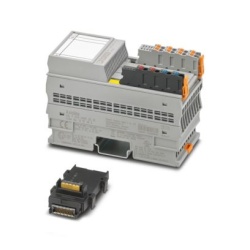
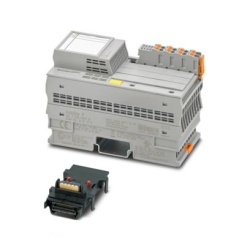
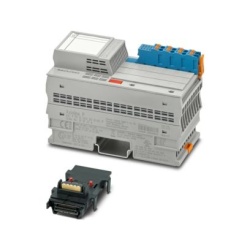
More Information about Phoenix Contact PLCs
Phoenix Contact PLCs are meant to make industrial automation work better, to be more flexible, and to allow more advanced control technology. Each product has modular engineering software and a purely digital control matrix for premium flexibility, control, and responsiveness. They have what is called "PLCnext Technology." That is now what these systems are based on. They have multiple programming languages that they allow—well, that you can use to program them: IEC 61131, C++, and a few MATLAB languages. This is to say that you could use Simulink, for example, if you worked in that environment. If you are a control systems engineer, you might be working in that type of environment.
FAQs
What industry would use Phoenix Contact PLCs in the automation technology system for access to devices?
Manufacturing industries commonly use Phoenix Contact PLCs in their automation technology systems to enable streamlined access and control of connected devices.
PLCs
Programming Logic Controllers (PLCs) are industrial computer that are designed to monitor and control a series of inputs and outputs.
The program running the PLC evaluates the inputs, and changes the output signals based on the program response to the input signals. Several programming languages are available to program most PLCs. The most common of these is called ladder logic. Ladder logic is a visual programming language that evolved from relay logic diagrams, which visually look like ladders because they consist of two vertical rails with runs between them that contain programmed logic. While ladder logic is the most common programming language used within PLCs, there are others that are also common, including function block diagrams, structured text and sequential function charts.
The hardware included in a PLC includes: a CPU, memory, I/O connections, a power supply and a programming device.
The CPU is a microprocessor that acts as the brains of the PLC. It performs logic operations, controls instruction and performs various other tasks that help keep the PLC running effectively. The memory in a PLC allows data to be stored that is needed to run the program, as well as any data that is collected by the inputs. Depending on the the type of PLC, the section for I/O may have a fixed number of points or it may be modular, allowing for additional I/O to be added. Many PLCs require some type of power supply and it is common to see more modular based systems integrate the power supply. Lastly, the PLC provides a programming device that feeds the program into the PLC's memory, so that it can perform the desired operation. This is most commonly some type of computer.
The PLC is designed to run a program repeatedly over and over again, normally many times a second. Each time a program runs, the PLC goes through some very specific steps.
While the order and the specifics may vary from manufacturer to manufacturer, they all typically follow a pattern similar to the following:
The PLC performs internal self checks to make sure that it is functioning correctly.
The PLC reads the inputs that are connected to it. It will then store the status of each of those inputs in its memory.
The PLC will execute the program logic.
The PLC will write the new values to the hard wired outputs to match those determined during the program execution. At some point in the cycle, communication requests will also be processed.
Following the execution of the last step, the PLC will then cycle back to the beginning of the process and begin all over again.