
Washdown Duty Motors

Washdown duty motors withstand the kinds of cleaning processes that most other electric motors might not handle, making them a good fit for environments where life depends on there not being any contaminants in the equipment: think food and beverage processing, pharmaceuticals, dairy operations. They're built to be able to withstand high-pressure water and steam as well as assorted cleaning solvents. Their housings, shafts, and exposed hardware are made mostly (if not entirely) with corrosion-resistant stainless steel. Stainless steel's smoothness is also excellent for cleaning and they feature no recesses or other places where bacteria can hide.
Washdown motors are equipped with almost magic-like seals. These advanced sealing systems ensure that water and cleaning agents don't intrude into the motor. In addition to common chlorinate-free cleansers, these stainless steel motors can withstand high-pressure sprays of all kinds, as well as the types of environmental conditions associated with certain installations—such as extreme temperatures or salt-laden air near coastal areas, aerosols in factories, or other manufacturing processes.
Products
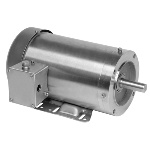
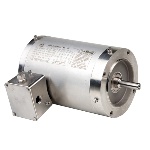

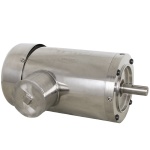
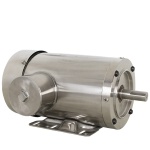
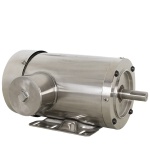
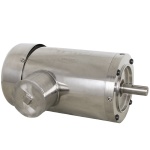
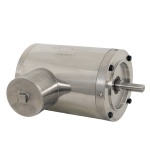
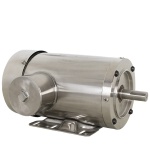
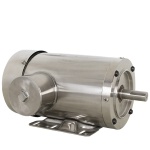
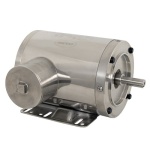
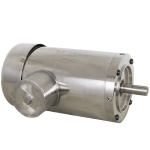
FAQs
Is the resistant insulation system in a washdown motor class f insulation?
Yes, the resistant insulation system in a washdown motor is often Class F insulation, providing high thermal tolerance and durability under rigorous washdown environments.
Does an improved paint system help food safe motors achieve food safe status over paint free motors?
Yes, an improved paint system can help food safe motors achieve food safe status by providing an additional layer of protection against corrosion and contamination, whereas paint-free motors rely solely on their material composition for safety.
Motor Starters, Soft Starters and VFDs
Motor Starters
Motor starters safely start and stop a motor in industrial applications. They are designed with a contactor, overload and circuit protection. They are used when basic motor control is required, where torque on the motor is not a concern and speed control is not needed. The advantages of motor starters include: lower cost, allows for remote operation, allows for monitoring of motor state (with the use of auxiliary contacts) and they are safe and efficient. The disadvantages include: high inrush current that can cause fuses to blow and breakers to trip if the inrush is too high, and the starter will allow a full torque to start the motor which can cause the motor to ramp up to full speed very quickly potentially causing the motor to wear and degrade prematurely.
Soft Starters
Soft starters protect motors from inrush current by gently ramping up the motor to full speed. They provide all of the same functions as a traditional motor starter. The advantages of soft starters include: they are less expensive than a VFD when only startup control is needed, they are a smaller system than a VFD where space is a concern and they prevent unwanted torque upon startup, prolonging the life of the motor. The disadvantages include: they are more expensive than a traditional motor starter and they do not allow for full speed control.
VFDs
A Variable Frequency Drive (VFD) allows for the slow ramp up of a motor during startup and the slowing down of the motor during shutdown. It also allows for full speed control during the entire run cycle of the motor. VFDs provide the same functions as both the traditional motor starters and soft starters. The advantages of VFDs include: full speed control (start, stop and in-between), more custom control and monitoring, energy savings due to efficient motor usage and less wear and tear on the motors. The disadvantages include: they are more expensive and larger than other motor control options and they generate heat that may require fans or AC units.