
Soft Starters
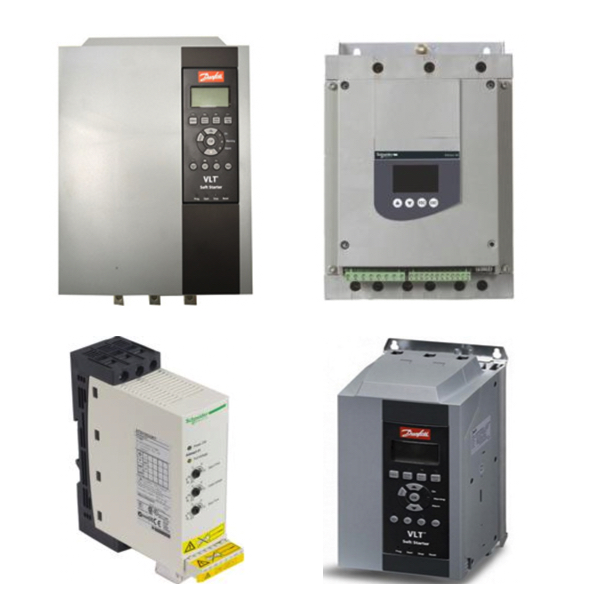
Because of their simplicity and reliability, they are among the most widely used motor control devices in the world. When used with three-phase motors, they provide extremely smooth acceleration and deliver controlled torque. Although a soft starter does not qualify as a motor control device, it regulates power input in a simple and elegant manner. When a belt drive or coupling is involved, using a mechanical soft starter may be one of the simplest ways to improve service life and reduce maintenance costs.
Regarding the design for torque control and optimized motor speed, soft starter models come with the flexibility needed for motor acceleration management and the preventive measures desired against sudden surge and electrical stress. Their use allows for voltage adjustments and inrush current limiting, acts that provide in the kinds of systems served by soft starters—largely pumps—with an efficiency and savviness that increase longevity and VRM (voltage risk management). In the kinds of pump application scenarios that lie at the low end of the pricing spectrum in our power utility world, one sees soft starters quite often.
Subcategories
Products
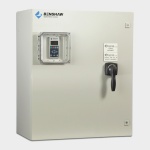
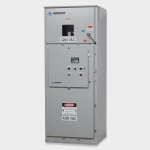
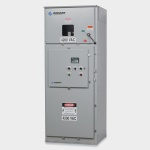
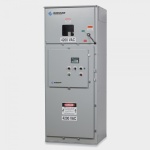
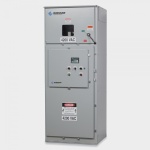
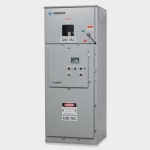
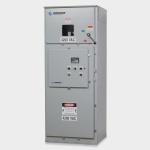
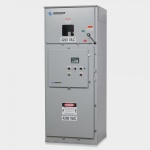
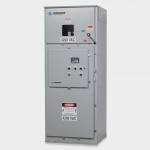
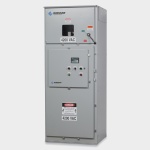
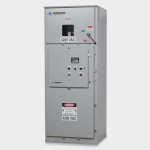
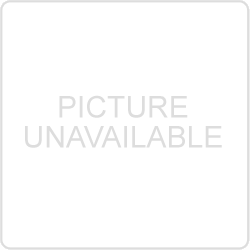
More Information about Soft Starters
Providing a smooth and well-controlled transition to full speed, soft starters are devices contributing to energy efficiency and operational stability. They are frequently selected in circumstances where a precise adjustment of speed is not a particular requirement but in which startup protection is necessary, and they are typically chosen over variable frequency drives in these circumstances. Many soft starter models include built-in protection features and other smart technologies that safeguard against voltage fluctuations and overheating, thereby making these devices a reliable solution for motors connected to critical applications. In power supply systems and high-torque industrial processes, using soft starters instead of other means to ensure smooth starting tends to bring about a number of efficiencies.
FAQs
Is there a difference in torque control voltage and maximum speed in electrical soft starters versus mechanical soft starters?
Yes, electrical soft starters provide more precise control over torque and voltage, and allow for adjustable maximum speeds, whereas mechanical soft starters generally offer less precise control and fixed maximum speeds.
Motor Starters, Soft Starters and VFDs
Motor Starters
Motor starters safely start and stop a motor in industrial applications. They are designed with a contactor, overload and circuit protection. They are used when basic motor control is required, where torque on the motor is not a concern and speed control is not needed. The advantages of motor starters include: lower cost, allows for remote operation, allows for monitoring of motor state (with the use of auxiliary contacts) and they are safe and efficient. The disadvantages include: high inrush current that can cause fuses to blow and breakers to trip if the inrush is too high, and the starter will allow a full torque to start the motor which can cause the motor to ramp up to full speed very quickly potentially causing the motor to wear and degrade prematurely.
Soft Starters
Soft starters protect motors from inrush current by gently ramping up the motor to full speed. They provide all of the same functions as a traditional motor starter. The advantages of soft starters include: they are less expensive than a VFD when only startup control is needed, they are a smaller system than a VFD where space is a concern and they prevent unwanted torque upon startup, prolonging the life of the motor. The disadvantages include: they are more expensive than a traditional motor starter and they do not allow for full speed control.
VFDs
Variable Frequency Drives (VFDs) allow for the slow ramp up of a motor during startup and the slowing down of the motor during shutdown. They also allow for full speed control during the entire run cycle of the motor. VFDs provide the same functions as both the traditional motor starters and soft starters. The advantages of VFDs include: full speed control (start, stop and in-between), more custom control and monitoring, energy savings due to efficient motor usage and less wear and tear on the motors. The disadvantages include: they are more expensive and larger than other motor control options and they generate heat that may require fans or AC units.