
Air Quality & Gas Detection
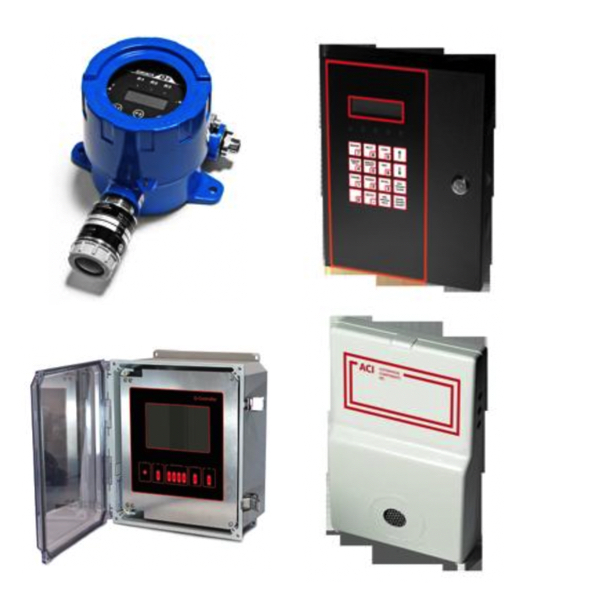
Air quality and gas detection are important for both indoor and outdoor environments, as they directly impact health and safety. Monitors and sensors play a vital role in detecting and measuring a range of pollutants, from common gases like carbon dioxide and carbon monoxide to more specific ones like sulfur dioxide, nitrogen dioxide, nitric oxide, and volatile organic compounds (VOCs).
An air quality monitor is a device that can measure the concentration of these pollutants in the air. Some also monitor levels of particulate matter, which are tiny particles suspended in the air that can be harmful when inhaled. Other monitors may detect the presence of gases such as methane, propane, and natural gas, which are important for detecting gas leaks that can lead to fires or explosions.
Carbon dioxide and carbon monoxide are two of the most common gases monitored, as they can be harmful or even lethal in high concentrations. Carbon monoxide, in particular, is odorless and colorless, making it especially dangerous without proper detection equipment.
Products
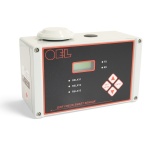
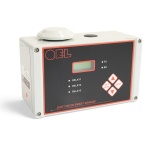
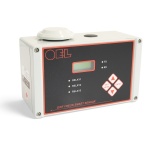
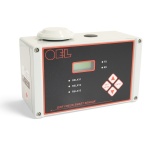
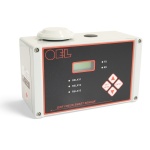
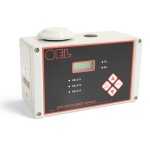
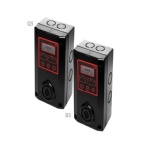
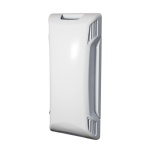
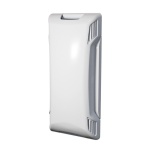
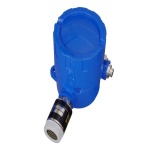
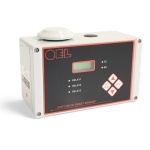
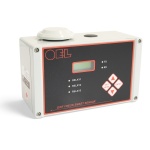
More Information about Air Quality and Gas Detection
Many air quality monitors also measure temperature and humidity, as these can affect the concentration and distribution of pollutants. The data collected from these devices can be used to inform decisions about ventilation, air conditioning, and heating systems to improve indoor air quality.
Non-dispersive infrared (NDIR) gas sensors are often used for carbon dioxide detection. They work by shining a light through a gas sample and measuring the light absorption. Each gas absorbs different wavelengths of light, so the sensor can determine the type and concentration of gas in the sample.
In an indoor environment, sources of pollutants can include natural gas stoves, which can release carbon monoxide, nitrogen dioxide, and other chemicals. Poor ventilation can lead to buildup of these gases, resulting in indoor air pollution. Regular monitoring can alert occupants to elevated levels of these gases, allowing them to improve ventilation with fresh outdoor air or reduce emissions.
Outdoor air quality monitoring is also important, as pollutants can come from a variety of sources, such as industrial emissions, vehicle exhaust, and natural occurrences. These monitors often have to withstand a wider range of conditions, and may also track pollutants like ozone and sulfur dioxide.
FAQs
What causes poor indoor air quality?
Poor indoor air quality can be caused by a variety of factors, including: poor ventilation, combustion sources, Volatile Organic Compounds (VOCs), radon, particulate matter and so on.
Analog and Digital Control Signals: The Basics
Digital Signals
Digital signals are represented in either a true or false. There is no gray area with digital signals. An example of this might be a light switch. A light switch is either on or off. Another example of this might be a motor that is running or not running. Digital signals can be generated with both AC and DC circuits with varying voltages, currents and resistance. Some practical examples of using digital signals in an industrial environment might be if a pump is running or not running or a whether a valve is open or closed.
Analog Signals
Analog signals convey information in the form of a range. A light switch might be on or off as a digital signal, but a dimmer switch would be an analog signal. It can be on or off, but it can also be somewhere in between. A practical example of using analog signals in an industrial environment would be if there is a need to measure the level of a tank; whether it's full, empty or somewhere in between. Analog signals can take many different forms with some of the more common being a 4 to 20 milliamp signal or a 0 to 5 or 0 to 10 volt signal.
Communication
Communication in a device can either be sent or received. Whether that data is sent or received depends on the type of information. Is there a need to monitor the status of something? If so, an input needs to be received about that information. Is there a need to control something? If so, an output needs to be sent about what needs to occur. Receiving inputs and setting outputs are both things that can be accomplished by using both digital and analog signal types. Therefore, the signals are referred to as analog outputs (AO), analog inputs (AI), digital inputs (DI) or digital outputs (DO).