
Smart Relays

Smart relays are small-scale PLCs that are ideal controllers for simple automation tasks. They generally feature a timer, counter, relay output and auxiliary contact. Some smart relays include LCD screens for easy programming and display. Smart relays can be used for applications such as lighting control, pump control, level control, HVAC, packaging machines and industry manufacturing.
IDEC SafetyOne FS1A safety controllers can replace up to six safety relay modules without any programming. They are easily configured by turning a dip switch to 1 of 24 predefined logic circuits. One module can connect with various IDEC safety and non-safety components such as Interlock Switches, Emergency Stop switches, sensors, pilot lights and light curtains. The FS1A safety controller features up to 6 dual channel safety inputs, 4 safety outputs and multiple non-safety inputs, monitor, blanking and solenoid drive outputs.
Products

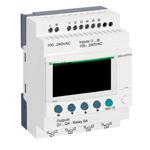


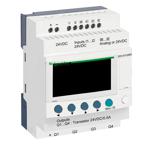


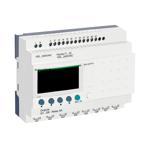




What is a relay? A relay is an electrically operated switch. Most relays use an electromagnetic to operate the switch. An electromagnet is a device that creates a magnetic field by passing an electrical current through a coil of wire. The magnetic field is then turned off when the current is removed.
Why use relays? Relays are commonly used when there is a need to control a switch with high voltage or circuits with large amounts of current passing through them. Operating these types of switches manually can be dangerous, inefficient and impractical. By using relays, operational safety is increased while also providing the ability to use smaller, safer and less expensive electrical equipment to control devices. Using relays allow for control of several devices on a single switch, as opposed to using several switches for each device. Relays can be combined with timers and logic circuits to assist in electrical automation.
How do relays work? A relay consists of two separate circuits that work together to open or close a switch (or contacts). The first circuit drives the coil (or electromagnet). The electricity passes through the coil, creating a magnetic field. The second circuit contains a set contacts and a separate power source. This circuit is what provides power to the electrical load.
When electricity passes through the coil, it creates a magnetic field. This magnetic field pulls the contact from the other circuit closed (or against the stationary contact) which will allow current to pass through the contacts, therefore allowing the load to become energized. When the coil is de-energized, the magnetic field is gone which allows the contact to be pushed back into its original state, de-energizing the load side of the circuit.