
Electromechanical Relays
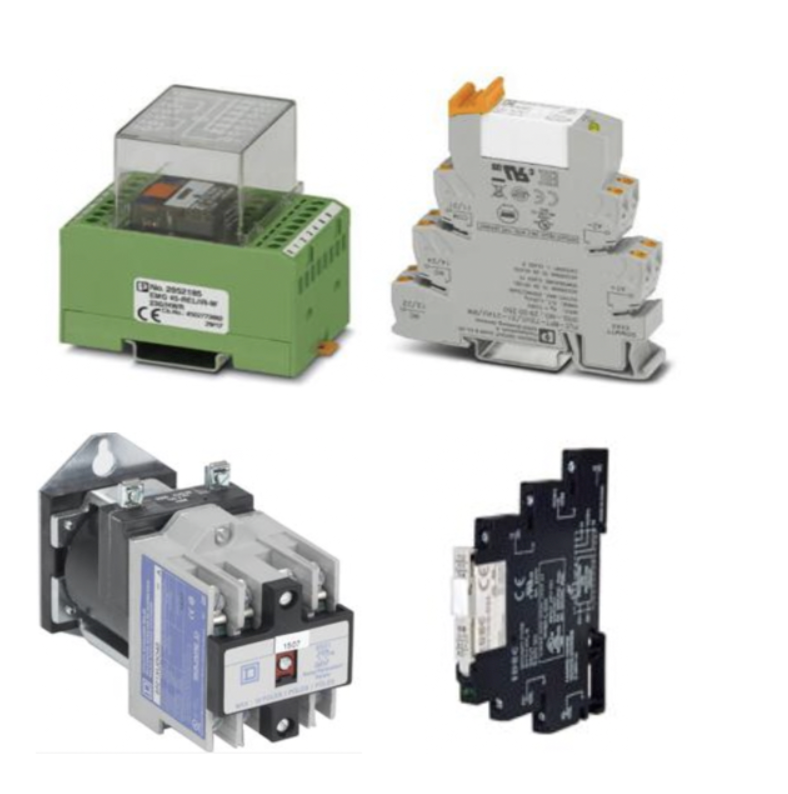
Electromechanical relays serve as versatile switching devices widely utilized in control circuits. They make it possible to switch electrical contacts on or off using contact positions that can be changed with a magnet. When this type of relay is powered, an electromagnet is energized; the current flowing through the coil generates a magnetic field that pulls the movable armature to the contacts, changing the contact position, enabling current to flow in the circuit, or disabling it. And doing all this by pulling a little armature with a whole lot of magnetic force is, as the saying goes, relaying on the (low-power) magnetism to achieve a (high-power) result.
Electromechanical relays are still highly regarded for all of the reasons that have made them longstanding devices. Their simplicity, cost-effectiveness, and the fact that they can handle surge currents and transient conditions make them still quite useful. Although solid-state relays are more and more being adopted in some applications because of their speed and durability, electromechanical relays are still a very common choice in situations where you want the kind of devices that provide mechanical, switching, and feedback operations.
Subcategories
Products
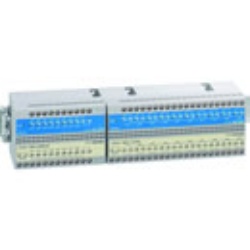
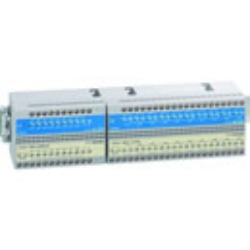
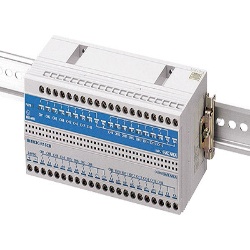
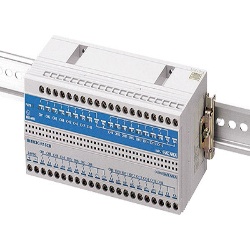
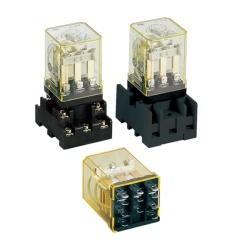
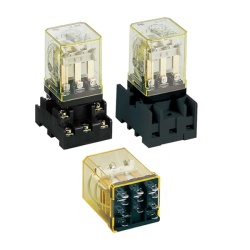
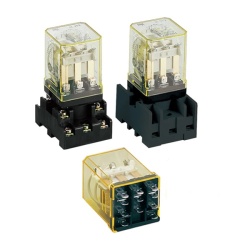
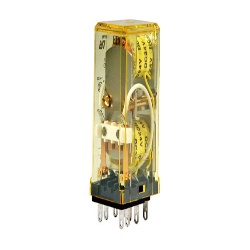
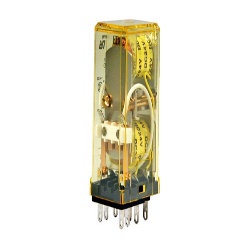
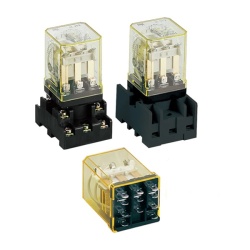
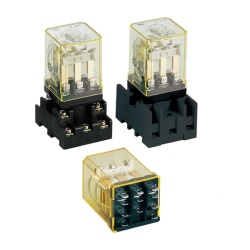
More Information about Electromechanical Relays
These terms and concepts help provide an understanding of the various aspects and features of electromechanical relays.
Relays
Electromechanical Relay: An electromechanical relay is a type of relay that utilizes both electrical and mechanical components to control the flow of current in an electrical circuit. It typically consists of a coil, a set of contacts, and a mechanical mechanism that controls the opening and closing of the contacts.
Power Relays: Power relays are electromechanical relays designed to handle high-power applications. They are capable of switching high voltages and currents, making them suitable for controlling heavy loads in industrial and electrical systems.
Reed Relays: A reed relay is a type of electromechanical relay that uses reed switches as its contacts. Reed switches are sealed glass tubes containing two ferromagnetic reeds that make contact under the influence of a magnetic field.
Latching Relays: Latching relays are relays that maintain their contacts in either an open or closed position without continuous power. They feature a mechanical latch that holds the contacts in position even after the coil is de-energized.
PCB Relays: PCB relays, or printed circuit board relays, are electromechanical relays designed for direct mounting on a printed circuit board. They have compact dimensions and are commonly used in applications where space is limited.
Signal Relays: Signal relays are electromagnetic switches that can be used to open or close a circuit, allowing or preventing the flow of current through it. Signal relays are typically used in low-power circuits to control the flow of signals between different components, such as between a microcontroller and a sensor.
Machine Tool Relays: Machine tool relays, also known as power relays or heavy-duty relays, are a type of electrical relay specifically designed for industrial applications, particularly in machine tools and equipment.
Other terms
Relay Coil: The relay coil is an electromagnet that generates a magnetic field when current flows through it. The magnetic field produced by the coil causes the mechanical components of the relay to move, resulting in the opening or closing of the contacts.
Electrical Circuit: An electrical circuit is a closed loop through which current can flow. Electromechanical relays are commonly used within electrical circuits to control the flow of current by opening or closing their contacts.
Solid State: Solid state refers to electronic components or devices that rely on semiconductor technology, such as transistors and integrated circuits, rather than mechanical parts. In contrast to solid state relays, electromechanical relays use mechanical contacts for switching.
Multiple Circuits: Some electromechanical relays have multiple sets of contacts, allowing them to control multiple circuits simultaneously. This can be useful in applications where multiple devices or circuits need to be controlled by a single relay.
Double Pole Single Throw (DPST): DPST refers to a relay configuration that has two sets of contacts, each capable of controlling a separate circuit. The contacts in a DPST relay can either be in an open or closed state, providing a double pole, single throw switching action.
Control Circuit: The control circuit of an electromechanical relay refers to the portion of the circuit that provides the electrical signal to energize the relay coil. When the coil is energized, it generates a magnetic field that actuates the mechanical components of the relay.
Contact Life: Contact life refers to the expected operational lifespan of the relay contacts. Over time, the repeated opening and closing of the contacts can cause wear, leading to a decrease in performance or eventual failure.
Wire Coil: The wire coil in an electromechanical relay is typically made of copper wire and is wound around a core. When an electrical current flows through the coil, it generates a magnetic field that interacts with the mechanical components of the relay.
Magnetic Core: The magnetic core is a component often found within the relay coil. It provides a path for the magnetic field generated by the coil, enhancing the magnetic coupling and overall efficiency of the relay.
FAQs
Is it possible to use relay switches and mechanical relays in a magnetic circuit?
Yes, relay switches and mechanical relays can be used in a magnetic circuit to control the flow of electrical current through the manipulation of magnetic fields and contacts.
How do relays operate in a relay system in automated test equipment?
Relays in a relay system for automated test equipment operate by using an electromagnetic coil to open or close electrical contacts, enabling precise control of circuit connections and switching between test configurations.
Relays: Electromechanical vs Solid State
Electromechanical Relays
Electromechanical relays (EMR) use physical moving parts to achieve the desired functionality. These moving parts include the contacts that switch between the normally open and normally closed stationary contacts in the relay. This movement is made possible by an electromagnet. When power is applied to this magnet, it will act on the movable contact causing the relay to switch. In an EMR, it is common to hear the switching sound that is represented as a “clicking” noise. This audible noise can be helpful when determining the functionality of the relay.
Solid State Relays
Solid state relays (SSR) use a low power, electrical signal to generate an optical semiconductor signal that will transmit and energize an output signal. When this is activated, the input optical signal will act as the switch, allowing a higher voltage signal to pass through the relays output components. The internal circuitry of a SSR is far more complex than an EMR, but there are no physical moving parts.