
Servo Motors
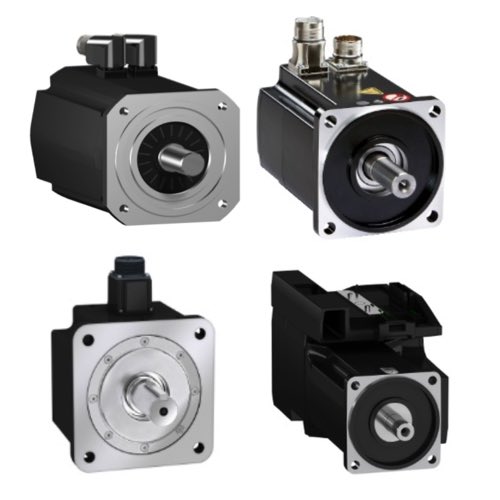
Motion control systems use servo motors as a main component to provide control over the angular or linear position of machinery, as well as over speed and torque. Servo motors differ from stepper motors in that the latter often are used to provide control in a system that has definite increments in position, such as when a machine is programmed to make cuts at specific angles. Like all motors, a servo motor consists of a control circuit, a motor shaft, and an output shaft. Its use in an industrial setting is much like that of a stepper motor; however, a servo motor has the advantage of providing much higher torque in a more compact design and maintaining precise motion control.
There are two main kinds of servo motors: brushed and brushless ones. Brushless servo motors are much better than brushed ones in many ways and are becoming increasingly common. Brushless servo motors are quieter and have something called a higher power density. And when it comes to strength, the other big number that brushed vs. brushless motors are compared on is torque. Brushless servo motors produce torque better and more evenly.
Products
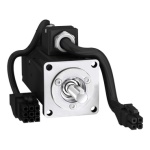
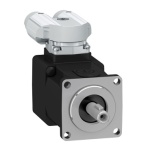
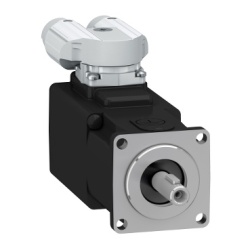
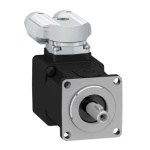
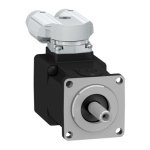
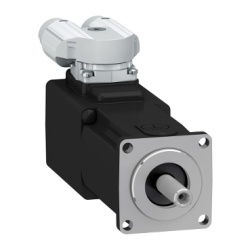
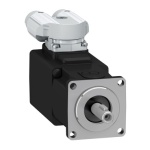
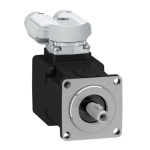
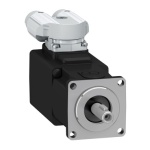
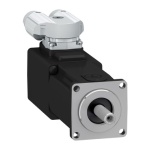
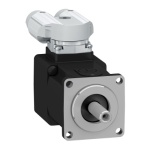
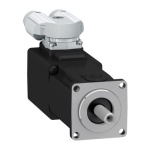
More Information about Servo Motors
A servo motor is a rotary or linear actuator that allows for precise control of angular or linear position, velocity and acceleration in a mechanical system. A servo driver is an electronic device that receives control signals from a controller and adjusts the voltage and current supplied to a servo motor. As servo motors require a rotary encoder and servo controller (driver) they are more expensive than stepper motors. A stepper motor is an electromechanical device that converts electrical pulses into precise mechanical movements, allowing accurate control of position, speed, and rotation in increments.
In advanced motion control systems, the integration of servo motors with control systems gives you maximum power output with minimal energy loss. The feedback signal that you get from encoders or resolvers ensures that the movement of the motor is in line with the programmed control position. Whether in robotics or in the aerospace and manufacturing sectors, these motors deliver the goods—high power output, near-miraculous control, and indefatigable reliability. Their near-exact maintenance of control over any kind of speed and position makes them essential in applications that demand precision, efficiency, and high-performance automation.
FAQs
Can continuous rotation servo motors be used for machine tools and conveyor systems in harsh environments?
Yes, continuous rotation servo motors can be used for machine tools and conveyor systems in harsh environments, as they provide precise control over continuous motion, are durable, and can withstand challenging conditions.
Are servo motors also permanent magnet motors that produce a reduction in electrical noise?
Yes, servo motors, particularly brushless servo motors, are often permanent magnet motors that help reduce electrical noise while providing precise motion control and high power density in industrial applications.
Motor Starters, Soft Starters and VFDs
Motor Starters
Motor starters safely start and stop a motor in industrial applications. They are designed with a contactor, overload and circuit protection. They are used when basic motor control is required, where torque on the motor is not a concern and speed control is not needed. The advantages of motor starters include: lower cost, allows for remote operation, allows for monitoring of motor state (with the use of auxiliary contacts) and they are safe and efficient. The disadvantages include: high inrush current that can cause fuses to blow and breakers to trip if the inrush is too high, and the starter will allow a full torque to start the motor which can cause the motor to ramp up to full speed very quickly potentially causing the motor to wear and degrade prematurely.
Soft Starters
Soft starters protect motors from inrush current by gently ramping up the motor to full speed. They provide all of the same functions as a traditional motor starter. The advantages of soft starters include: they are less expensive than a VFD when only startup control is needed, they are a smaller system than a VFD where space is a concern and they prevent unwanted torque upon startup, prolonging the life of the motor. The disadvantages include: they are more expensive than a traditional motor starter and they do not allow for full speed control.
VFDs
A Variable Frequency Drive (VFD) allows for the slow ramp up of a motor during startup and the slowing down of the motor during shutdown. It also allows for full speed control during the entire run cycle of the motor. VFDs provide the same functions as both the traditional motor starters and soft starters. The advantages of VFDs include: full speed control (start, stop and in-between), more custom control and monitoring, energy savings due to efficient motor usage and less wear and tear on the motors. The disadvantages include: they are more expensive and larger than other motor control options and they generate heat that may require fans or AC units.