
Hazardous Location Enclosures
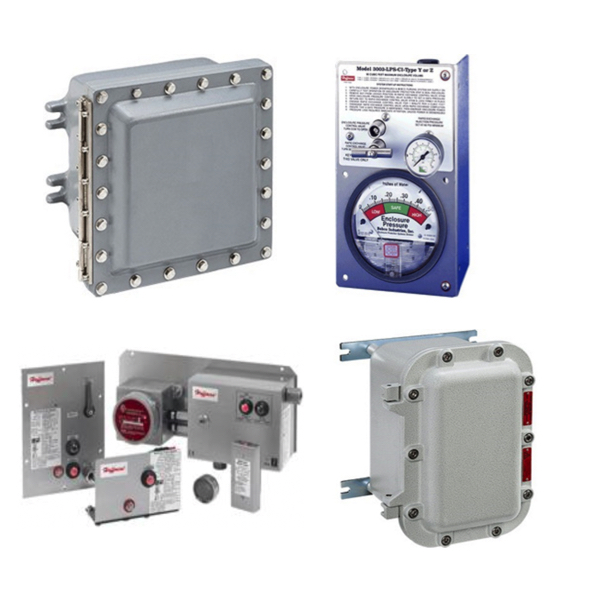
Hazardous location enclosures are specially crafted to protect electrical equipment in hazardous environments where flammable gases, vapors, or dust might be present. These enclosures are designed to prevent internal equipment from causing an external explosion or fire. A distinct characteristic of such enclosures is their ability to withstand an internal explosion, ensuring that any potential sparks or ignitions are contained within the enclosure, preventing them from reaching the external explosive environment.
Class I, Class II, and Class III are commonly used classifications, with Class I primarily pertaining to gases and vapors, Class II for dust, and Class III for fibers. Within these classes, various divisions and zones define the specific nature and likelihood of the hazardous materials being present either continuously or intermittently. For example, Class I Division 1 indicates a location where explosive gas-air mixtures are likely to occur during normal operations.
Hazardous location enclosures also encompass explosion-proof enclosures, which are designed to contain and extinguish any explosions that occur within their boundaries. The use of inert gas in some of these enclosures, known as purge systems, helps in maintaining a safe internal atmosphere by displacing the hazardous gases or vapors.
Subcategories
Products
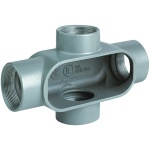
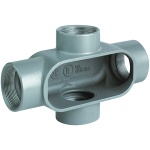
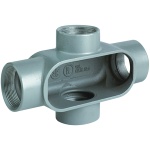
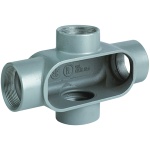
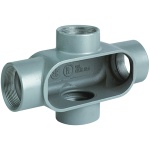
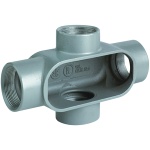
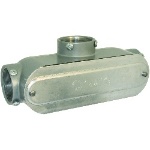
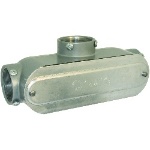
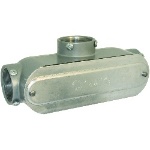
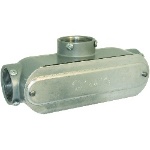
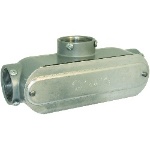
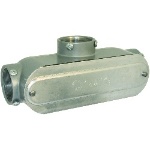
More Information about Hazardous Location Enclosures
It's essential for these enclosures to offer protection not only from explosions but also from other environmental factors such as corrosion from chemicals or hose directed water. Their design often incorporates features like increased safety to ensure that any potential ignition sources, like a spark, are either eliminated or safely contained.
Given the risks associated with hazardous areas, it's crucial for such enclosures to meet the specific standards set by bodies like the National Electrical Manufacturers Association. This guarantees that the equipment housed within these enclosures remains safe, and the surrounding environment is protected from potential fires or explosions. Junction boxes, specifically designed for these locations, often fall under the category of hazardous location enclosures.
In industrial settings, ensuring the safety of workers and equipment becomes paramount, especially when dealing with explosive gases or vapors. Utilizing hazardous area enclosures is a proactive measure, ensuring that the equipment functions optimally without posing any threat to its surroundings.
FAQs
What are considered hazardous substances?
Hazardous substances are any chemicals or materials that have the potential to cause harm to human health or the environment.
What are considered hazardous locations?
Hazardous locations are areas where flammable liquids, gases, vapors, or dusts are present, either continuously, intermittently, or during normal operations, in quantities sufficient to produce explosive or ignitable mixtures. When these mixtures come into contact with an ignition source, there's potential for an explosion or fire. Due to these risks, special precautions are taken in these areas regarding the design, installation, and use of electrical equipment.
Purge System Basics
3 common reasons to use purge systems
They allow electrical enclosures to be installed in hazardous areas without the need for explosion proof enclosures.
They recycle the air inside of an enclosure, reducing the internal temperature.
They help reduce the effects of corrosion on components housed within the enclosure.
How does a purge system work?
Purge systems use incoming air from a supply line, solenoid valves, pressure gauges and pumps, to constantly maintain a positive pressure inside an enclosure. This prevents any flammable gases from entering the enclosure potentially causing an ignition event to occur. By maintaining a positive pressure within the enclosure, moisture and corrosive gases are also prevented from entering the enclosure and damaging components. Most purge systems will ensure that the air inside the enclosure is recycled a certain amount of times within a given time period. This air recycle function assists in maintaining a cooler temperature within the enclosure.