
VFD & Motor Protection

Variable frequency drives (VFDs) are electronic devices used to control the speed and torque of AC motors by varying the frequency and voltage supplied to the motor. Along with their speed control capabilities, VFDs incorporate several motor protection features to safeguard the motor and its associated equipment.
Motor protection is a critical aspect of VFDs, and they incorporate a range of protective functions to prevent motor damage and ensure reliable operation. These protection functions include overload protection, short circuit protection, stall prevention, and current limitation. Overload protection safeguards the motor against excessive current draw, while short circuit protection helps in detecting and mitigating short circuit faults.
VFDs often incorporate additional protective devices such as line reactors, resistors, and capacitors. Line reactors help in reducing harmonics and provide added protection against power surges and voltage transients. Capacitors and resistors assist in improving motor performance and protecting against voltage spikes and inrush currents.
Subcategories
Products
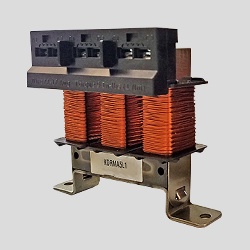
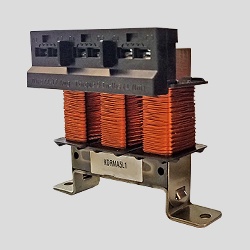
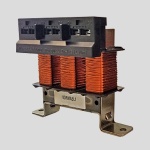
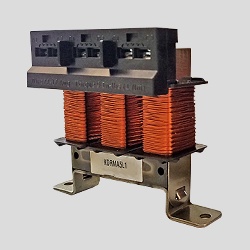
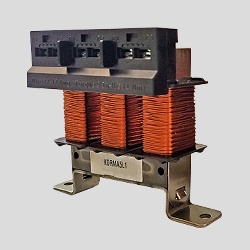
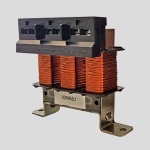
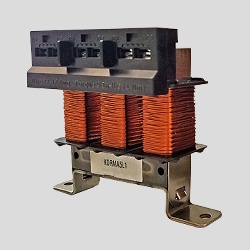
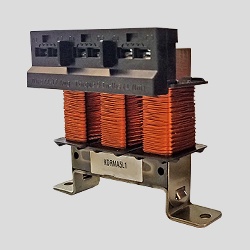
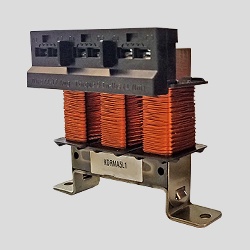
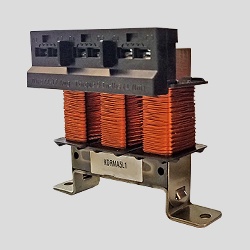
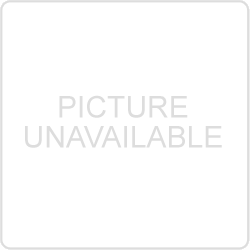
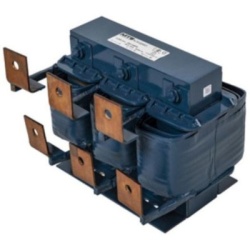
More Information about VFD and Motor Protection Devices
To provide better protection, VFDs also employ complex protective functions that go beyond basic overload and short circuit protection. These functions may involve monitoring motor parameters such as winding temperature, motor current, and motor nameplate information. By continuously monitoring these parameters, VFDs can adjust their operation to prevent motor overheating and ensure safe operation within the motor's rated limits.
It is important to follow the VFD manufacturer's recommendations for motor protection and adhere to the motor nameplate information to ensure proper operation and protection. This may involve correctly sizing the VFD based on the motor's power requirements and implementing appropriate wiring practices to minimize noise and interference.
VFDs also offer other benefits beyond motor protection. They provide precise control over motor speed, enable energy savings through efficient operation, and reduce mechanical stress on the motor and connected equipment. Additionally, VFDs allow for soft starting and stopping of motors, which extends motor life and reduces mechanical wear and tear.
FAQs
How is a variable frequency drive similar to motor speed controllers?
VFDs are a more advanced type of motor speed controller that utilizes specific electronic components and control algorithms to achieve precise speed control and additional functionality such as motor protection and advanced control features.
Does a motor VFD provide stall prevention current limitation?
Yes, a motor Variable Frequency Drive (VFD) can provide stall prevention current limitation as part of its motor protection features. Stall prevention is an important function in VFDs to protect the motor and the connected equipment from damage or excessive stress.
What is provided on a variable frequency drive diagram?
A variable frequency drive (VFD) diagram typically provides a visual representation of the components and connections involved in the operation of the VFD system. These can include: power supply, input section, rectifier, DC bus, inverter, control section, output section, motor and control signals.
Inductive Load Basics
Electrical load is an electrical component or portion of a circuit that consumes electrical power. For example, a power source such as a battery or generator will have a load which consumes that power, such as a light bulb, motor or television.
There are three types of electrical loads: capacitive loads, resistive loads and inductive loads
Capacitive and Resistive Loads
Capacitive loads are similar to inductive loads in that the current and voltage are out of phase with one another, however, capacitive loads see the current reach its maximum before the voltage, while inductive loads see the voltage reach its maximum before the current. Resistive loads typically consist of things like heating elements.
Inductive Loads
Inductive loads use a coil to produce a magnetic field. The most common types of inductive loads are motors, fans, blenders and pumps. Inductive loads resist change in current, which lags behind the voltage. There are two different types of power with inductive loads. There is real power, which is based off of the work that is actually being done by the motor and there is reactive power, which is the power that is drawn from the power source to produce the magnetic field. The total power of an inductive load combines both the real power and reactive power.