
Submersible Motors
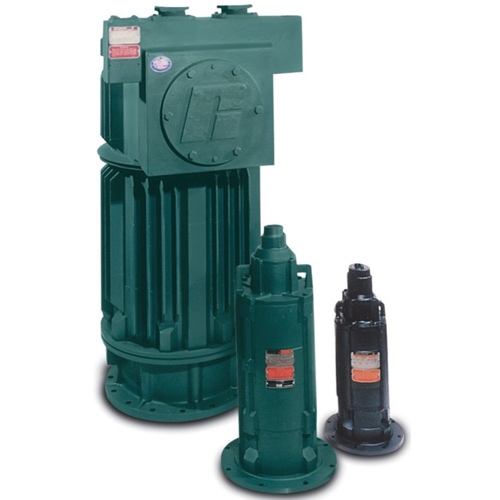
A submersible motor features totally enclosed, blower-cooled enclosures and are designed with a unique sealing system. They are meant to work under water and are built to work in the types of operations that might often flood, like industrial wastewater operations; slurry pumps; and pumps that operate under water. These motors are available as "wet pit" motors that work fully submerged, and as "dry pit" motors that are in enclosed, blower-cooled setups that keep them from overheating. The insulation system in a submersible motor ensures that it works at peak performance even at the maximum depth an application might require.
Numerous submersible motors are supplied with special paint coatings and extended cable lengths designed to handle corrosive environments and very moist conditions. The construction of the motors from stainless steel adds a further layer of protection from rust and from exposure to chemicals, and is, in fact, a pretty common material choice when it comes to making the kind of motors that last for years in a few specific, demanding applications—the kinds of applications that might submerge a motor for long periods of time. The totally enclosed design of a submersible motor allows it to work well and reduces the amount of maintenance needed to keep it operational.
Products




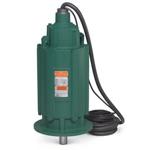
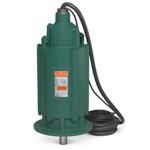



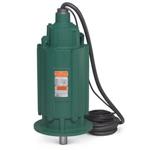
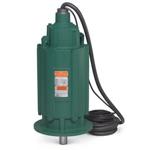

More Information about Submersible Motors
For maximum efficiency, submersible motors are designed to conserve space. In many cases, that means they work with shafts that are one size smaller than might be expected, without compromising power output. But maximizing space in a compact installation is only half the story. Even with that significant advantage, submersible motors can still be used for pumping and moving fluids in all sorts of underground conditions, whether at depths exceeding thirty feet or in aquifers just below the surface. Submersible pumps are typically centrifugal pumps with the motor and pump components enclosed in a waterproof casing.
FAQs
Do class I submersible motors require engineering approval for reliable operation in dry pit applications?
Yes, Class I submersible motors often require engineering approval to ensure reliable operation in dry pit applications, meeting safety and performance standards for demanding industrial environments.
Motor Starters, Soft Starters and VFDs
Motor Starters
Motor starters safely start and stop a motor in industrial applications. They are designed with a contactor, overload and circuit protection. They are used when basic motor control is required, where torque on the motor is not a concern and speed control is not needed. The advantages of motor starters include: lower cost, allows for remote operation, allows for monitoring of motor state (with the use of auxiliary contacts) and they are safe and efficient. The disadvantages include: high inrush current that can cause fuses to blow and breakers to trip if the inrush is too high, and the starter will allow a full torque to start the motor which can cause the motor to ramp up to full speed very quickly potentially causing the motor to wear and degrade prematurely.
Soft Starters
Soft starters protect motors from inrush current by gently ramping up the motor to full speed. They provide all of the same functions as a traditional motor starter. The advantages of soft starters include: they are less expensive than a VFD when only startup control is needed, they are a smaller system than a VFD where space is a concern and they prevent unwanted torque upon startup, prolonging the life of the motor. The disadvantages include: they are more expensive than a traditional motor starter and they do not allow for full speed control.
VFDs
A Variable Frequency Drive (VFD) allows for the slow ramp up of a motor during startup and the slowing down of the motor during shutdown. It also allows for full speed control during the entire run cycle of the motor. VFDs provide the same functions as both the traditional motor starters and soft starters. The advantages of VFDs include: full speed control (start, stop and in-between), more custom control and monitoring, energy savings due to efficient motor usage and less wear and tear on the motors. The disadvantages include: they are more expensive and larger than other motor control options and they generate heat that may require fans or AC units.