- Antennas & Radios (Industrial)
- Batteries (Industrial)
- Breakers, Fuses & Circuit Protection
-
Cable, Wire & Assemblies
- Phoenix Contact Cables & Connectors
- Weidmuller Cables & Connectors
- Ericson Cables & Accessories
- Wire
- Ethernet Cable & Accessories
- Coax Cable & Accessories
- Fiber Optic Cables & Accessories
- Audio, Data & Video Cable & Accessories
- AC Power Cords
- Cable Reels
- Cordsets
- Bonding & Grounding
- Sensor Cables & Connectors
- Wire & Cable Accessories
- View All
- Connectors
-
Enclosures
- All Enclosures
- Steel Enclosures & Junction Boxes
- Stainless Steel Enclosures
- Non-Metallic Enclosures
- Aluminum Enclosures
- Commercial Enclosures
- Consolet Enclosures
- Disconnect Enclosures
- Hazardous Location Enclosures
- HMI Enclosure Systems
- Modular Enclosures
- Network Cabinets & Racks
- Push Button Enclosures
- Solar Enclosures
- Wire Management Wireways & Troughs
- View All
-
Enclosure Accessories
- Accessories for Specific Enclosure Models
- Enclosure Air Conditioners & Cooling
- Enclosure Backplates & Panels
- Enclosure Bases & Base Accessories
- Enclosure Cable Management
- Enclosure Corrosion Inhibitors
- Enclosure Door & Door Accessories
- Enclosure Floor Stands, Pedestals, Legs, & Casters
- Enclosure Lighting
- Enclosure Mounting, Hardware & Fasteners
- Enclosure Paint, Patch Kits & Hole Seals
- Enclosure Power Distribution & Grounding
- Enclosure Pressure, Humidity & Condensation
- Enclosure Racks & Rack Mounting
- Enclosure Rain Hoods & Drip Shields
- Enclosure Roof Plates & Canopies
- Enclosure Shelves, Drawers & Trays
- Enclosure Sun-Solar Shields
- Enclosure Thermal Management
- Enclosure Windows & Inspection Windows
- Data Interface
- View All
- Energy & Power Measurement
- Instrumentation
- Labels & Markings
- Lighting
- Motors & Motor Control
- Networking & Communication
- Operator Interface
- Panel Hardware
- Personal Protective Equipment
- PLCs & IO
- Plugs & Receptacles
- Power Supplies & Regulation
-
Push Buttons, Switches & Signaling Devices
- Push Buttons
- Indication & Signaling (Pilot Lights, Beacons, Audibles etc.)
- Selector Switches
- Foot Switches
- Control Stations
- Potentiometers
- Pendant Control Stations
- Biometric Switches
- Joysticks
- Light Switches & Wallplates
- Legend Plates for Switches, Push Buttons & Signaling Devices
- Push Button & Switch Accessories
- View All
- Relays, Timers & Counters
- Safety (Industrial)
- Security & Surveillance
- Sensors
- Signal & Power Conditioning
- Software Services
- Solar
- Structural Aluminum Framing
- Surge Protection & Filters
- Tapes & Adhesives
- Terminal Blocks & Connectors
- Tools & Supplies
- Towers & Direct Embedded Poles
Motor Starters
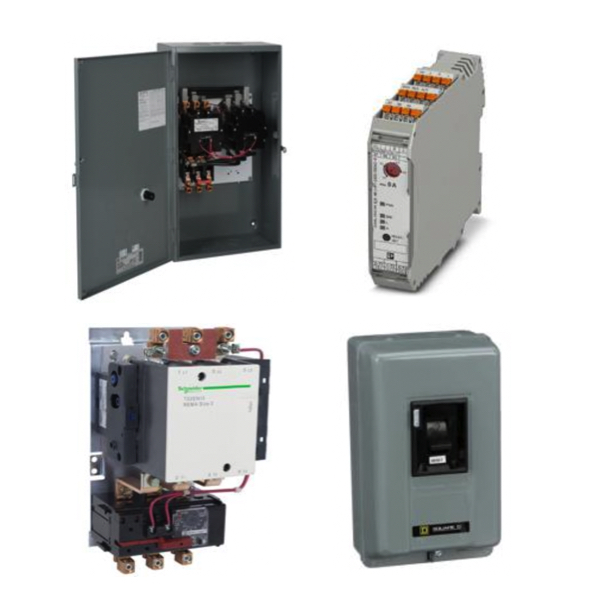
Electric motors are safely started, stopped, and protected by motor starters, which are essential electrical devices. Motor starters boost the motor up to voltage and control excessive current that threatens to damage the motor. Starting under too much load can cause an electric motor to draw several times its full-load current until the motor reaches speed. Current at startup can be controlled by the use of a magnetic motor starter. When using a magnetic motor starter, the magnetic starter automatically breaks the control circuit if there is a power failure or a drop in voltage to the motor. When power is restored, the motor is ready and raring to go, but with the help of a soft start, if necessary, to overcome any torque obstacles.
Depending on application requirements, different motor starters are used. A star-delta starter is the common selection for a delta connected motor. This type of starter is used to provide reduced voltage during the critical intervals of starting (e.g., when the motor first begins to turn and must overcome inertia). A reduced voltage differentiates the small but necessary starting torque from the much larger amounts of torque typically produced right after the motor is first turned on. If the motor must be protected because it tends to heat up or has windings that could be damaged by too much torque (or voltage), then a star-delta starter offers some insurance—that is, until it switches back to full power after the motor gets going.
Subcategories
More Information about Motor Starters
Also found in motor starters are highly sophisticated safety features and functions such as overload relays, contactor coils, and starter contacts. These features and functions help to prevent overheating, and they help to protect against excessive electrical current draw, which can be damaging to equipment and power infrastructure. Further protection for the motor is usually provided by a circuit breaker that will open the circuit in an overcurrent condition, or a situation where the motor has stalled.
Protection for the power system that the motor is connected to is usually provided by an assembly that contains a circuit breaker and a voltage regulating device that ensures the main incoming voltage to the motor remains stable. Whether employing a manual starter or a magnetic motor starter, these assemblies are critical in the safe operation of motors.
FAQs
Does the motor starter provide manual speed control and starting torque control of the electrical device (electric motor) through the power circuit?
No, the motor starter typically does not provide manual speed control and starting torque control; these functions are generally managed by devices like variable frequency drives (VFDs) or dedicated motor controllers, while the starter primarily handles safe starting, stopping, and protection of the motor.
Do manual motor starters have short circuit protection for the electrical power that runs them?
Yes, manual motor starters typically include short circuit protection to safeguard the motor and electrical power circuit.
Can a control circuit transformer be used with an AC motor to help control motor speed and provide overload protection?
Yes, a control circuit transformer can be used with an AC motor to help regulate motor speed and provide overload protection by ensuring stable control voltage and safeguarding against electrical faults.
Motor Control Basics
Motor control allows operational control of electrical motors in various environments.
Motor control circuits provide a safe way to operate electrical motors. Back when motor control circuits were in their infancy, it would have been common to see a simple disconnect switch that would be used to turn on and off a motor. Depending on the size of the motor and how much voltage was required, operating this disconnect would have been dangerous, with a very high possibility of arcing or electrocution. Not to mention that when the disconnect was actuated, the large amount of inrush current would have damaged the motor over time.
In today's motor control circuits, there are a few common pieces of hardware.
A circuit breaker is used to protect the motor and any hardware downstream. A contactor and an overload relay are connected together and function in tandem to allow for remote and safe operation of the motor. The contactor functions much like a relay, allowing for a smaller electrical circuit to remotely close the motor contacts, starting the motor. The overload relay is designed to protect the motor in the case of a prolonged overcurrent event. These two devices are wired in series, so that if the overload relay detects an overcurrent event, the contactor will open the motor contacts, shutting off power to the motor.
The other two most common types of motor control hardware are a soft starter and a Variable Frequency Drive (VFD).
Both of these devices function in a similar way to the motor circuit with some added functions. The soft starter is designed to reduce large inrush current to the motor upon startup. This “soft starting” of the motor will prolong its life and allow for safer operation. The VFD performs the soft start functions, but also allows for speed control of the motor. This speed control is critical in many different environments and has made VFDs one of the most common and safe to use motor control circuits today.