
Power Monitors, Transducers & Repeaters
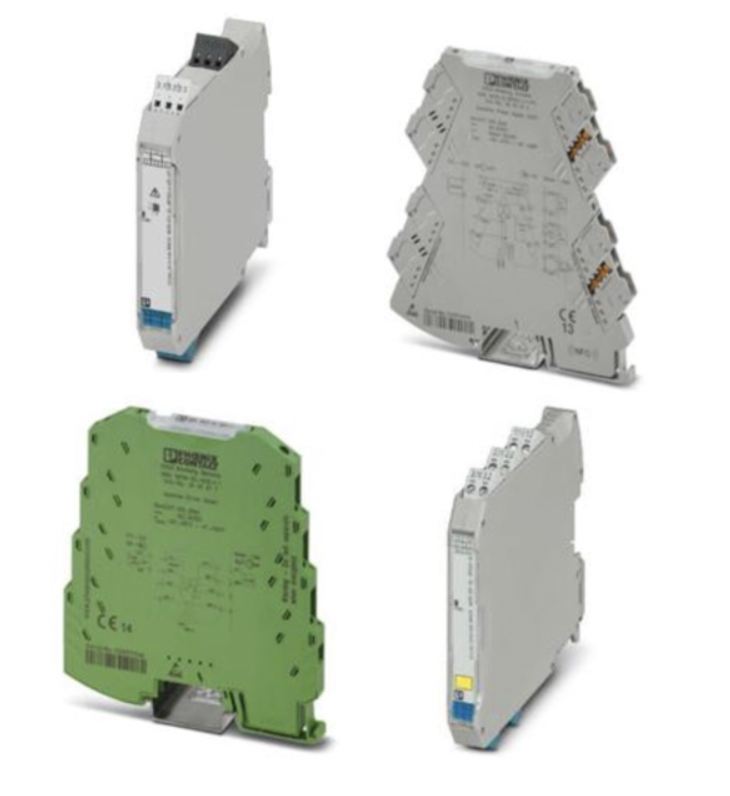
Signal conditioners are devices that convert one type of electronic input signal into a different type of output signal. The input signals received from sensors are amplified, filtered and isolated into a more easily read output signal for processing. Many applications involve measurements from sensors that need signal conditioning before the instrument can accurately and effectively measure the signal. Functions of signal conditioners include: conversion, linearization and amplification.
Signal conversion is used by industrial applications that use a wide range of sensors to perform measurements. The different signals generated by the sensors need to be converted, in order to be usable by the instruments they are connected to. Some signals produced by sensors need to be linearized by a signal conditioner because they do not have a straight-line relationship with the physical measurement. Linearization results in a more accurate result.
Signal amplification increases the signal for processing and digitization. It can be performed by increasing the input signal or by increasing the signal-to-noise ratio. Instrumentation amplifiers are used with DC signals and have high input impedance, high gain and common mode rejection ratio. Isolation amplifiers isolate high DC levels from the device while passing small AC or differential signals. Signal filtering filters the signal frequency spectrum to only include valid data and blocks any noise. The filters can be made from either active or passive components or a digital algorithm.
Products
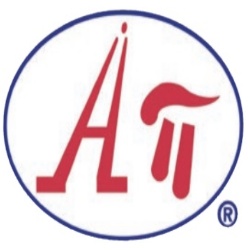
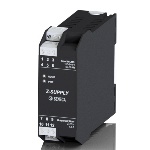
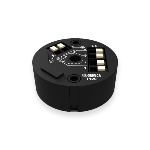
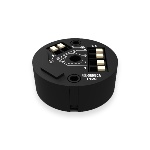
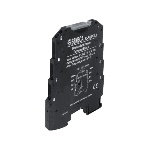
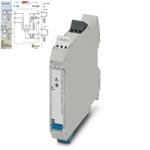


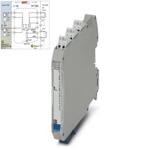



Signal Isolation Basics
When dealing with scenarios that involve many different control circuits and input and output signals, distortion can occur. This distortion can corrupt the signals, rendering the data virtually useless. For example, if there is a transmitter sending a 4-20 milliamp signal to a PLC and the transmitter is located several feet away in a different building, both devices have the possibility of having different ground potentials. This difference in potential can cause the current flowing between the two points to distort the control signal being sent. This current flow between two different ground potentials is referred to as a ground loop. Ground loops can be fairly common in industrial control applications, and because of the issues that they cause, must be controlled. This is where signal isolation comes into play.
Signal isolation
Signal isolation provides electrical isolation between input and output circuits and is sometimes referred to as galvanic isolation. This physical break in the galvanic path of the control signal offers a way to eliminate the effects of ground loops. There are two different methods of signal isolation that are used today: optical isolation and transformer isolation.
Optical isolation
Optical isolation uses a module and a small circuit board composed of an LED and photosensitive detector with an insulating air gap, that creates the physical separation. The advantage of using optical isolation is that the size of the unit is quite small and can provide higher levels of insulation than other methods. A disadvantage of using optical isolation is that these devices need to be powered separately from the signal itself and the signals need to be relatively small.
Transformer isolation
Transformer isolation utilizes a transformer to provide the isolation gap, while still allowing the signal to be transmitted. This type of isolation works well with AC power signals. An advantage of using this type of isolator is the that it does not require its own power source. It can simply transmit the signal passively.