
Fieldbus Solutions
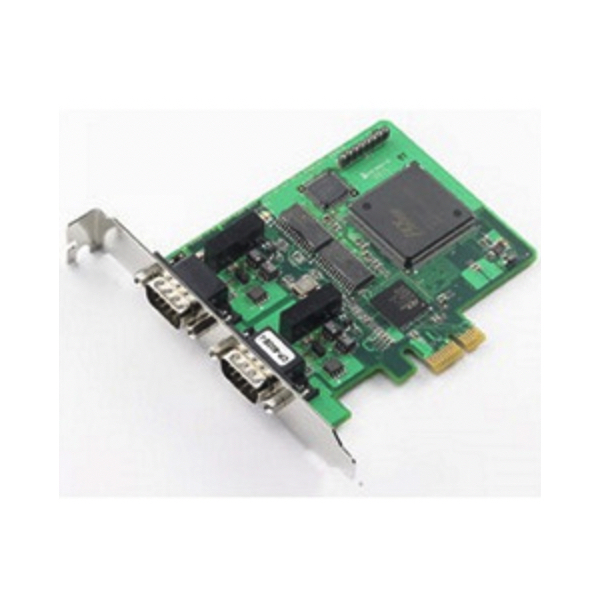
Fieldbuses connect multiple field devices over a single cable or ‘bus.’ In fieldbus networks, distributed IO mechanisms distribute or collect multiple inputs and outputs from the field into a local IO device. The data is then transferred through just one cable to and from the Programming Logic Controller (PLC). Fieldbuses have eliminated the need to individually wire each field device to its controller. They allow multiple analog and digital signals to be connected at the same time. Some fieldbus instruments perform calibration and diagnostics for various operations such as temperature readings, conductivity measurement and flow controls. There are many different types of fieldbuses supported by different manufacturers, most of which are defined by international standards.
Profibus is a fieldbus network designed for communication between PLCs and devices. This is accomplished through a master-slave communication, where the master (PLC) has multiple slave devices (sensors, motors, actuators, etc) communicating through a single cable. Profibus can handle large amounts of data at high speeds and can serve the needs of large installations. Profinet is similar to Profibus but uses Ethernet for its communication.
Products
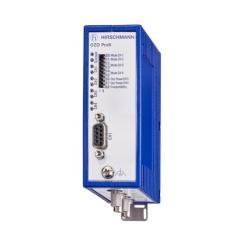
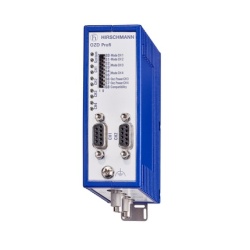
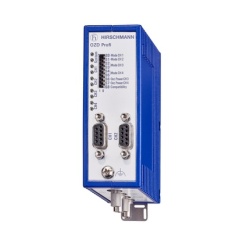
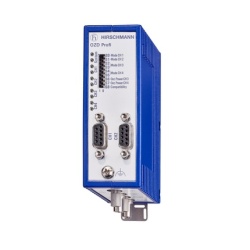
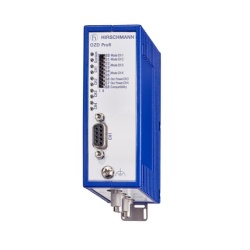
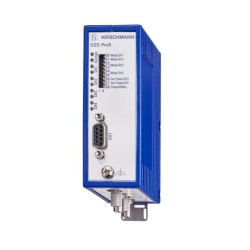
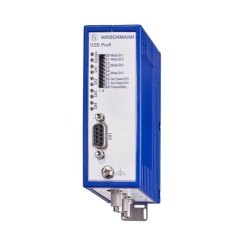
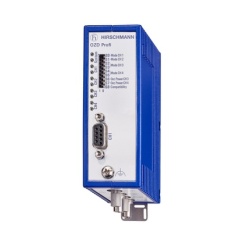
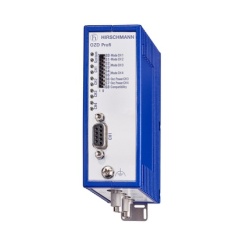
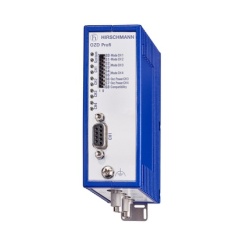

More Information about Fieldbus Solutions
Controller Area Network (CAN) is a fast serial bus that is designed to provide a reliable and efficient link between actuators and sensors. CAN uses a twisted pair cable to communicate with up to 40 devices. It provides standardized communication objects for service data, process data, network management, emergency messages and synchronization. The CAN bus is primarily used in embedded systems because it provides fast, real-time communication between microcontrollers.
Serial Communication Basics
Serial communication sends data sequentially over a computer bus or communication cable one bit at a time. Parallel communication sends data simultaneously over multiple communication lines in a single bus or cable multiple bits at a time. While it may seem that parallel communication would be the preferred method, this is not always the case. Because of the increased complexity of data transmission in parallel communication, serial communication can provide faster speeds. The speed of serial communication can be altered by adjusting the BOD rate, which increases the number of the bits transmitted per second.
Two of the most common standards that have been created to take advantage of serial based communication in the industrial space are RS 232 and RS 485. RS 232 standard used to be very common, however it had lower transmission speeds, short maximum cable lengths and large voltage swings, making it useful only in certain situations. RS 485 is an improved standard that is still found in many applications today. It fixed many of the issues the RS 232 standard had by providing higher transmission speeds, longer cable lengths and other improvements that increased its usability and performance.