
Motor Management
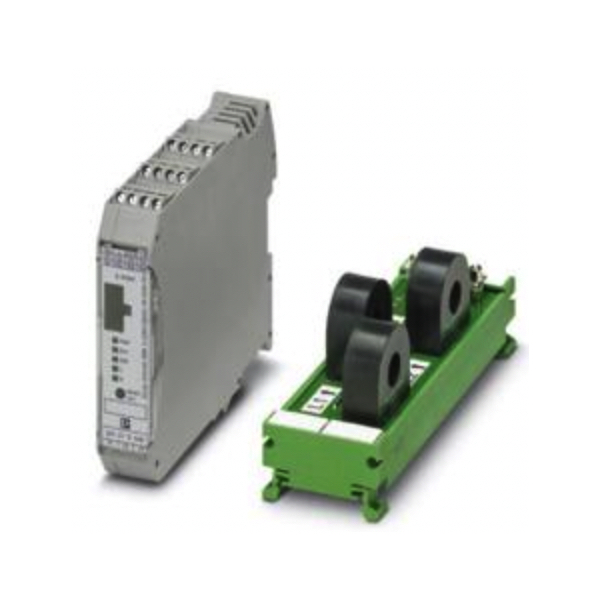
Motor management devices are designed to give you total control, protection, and monitoring of electric motors in industrial situations. They're renowned for their reliability, advanced features, and easy integration into numerous automation systems. They help make sure electric motor operation is both efficient and safe, minimizing downtime. At the same time, they clearly pay off by reducing service needs and extending the life of your motor equipment.
Motor management devices are a key part of maintaining the reliable operation and extending the service life of motors. Their ability to monitor vital parameters in real-time — current, voltage, power, and temperature — allows for the prompt identification of any problems that might develop.
They detect an overloading condition in real-time; they see a phase loss as it happens. By comparing what's happening now to what was happening previously, they identify conditions that might be developing and likely lead to increased unavailability or reduced reliability in motors.
Products
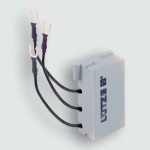
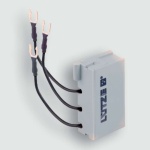
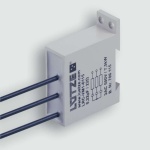
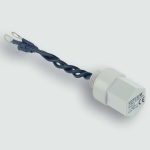
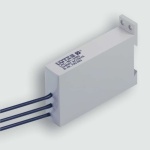

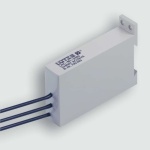
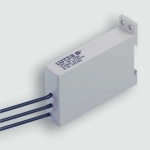
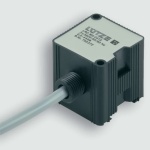
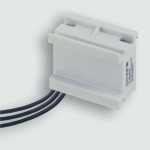
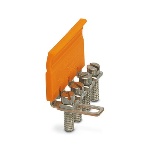

FAQs
Can motor management systems create more energy efficiency and motor efficiency by requiring motor maintenance and motor repair of AC motors?
Yes, motor management systems can enhance energy efficiency and motor efficiency by proactively scheduling maintenance and repairs for AC motors, ensuring they operate optimally and reducing energy consumption and downtime.
Do variable frequency drives, soft starters and motor controllers help with efficient motors?
Yes, variable frequency drives, soft starters and motor controllers improve motor efficiency by precisely controlling motor speed and torque to match load demands, reducing energy consumption and energy costs.
When a motor fails, is it necessary to make a another motor purchase or can the old motor be repaired?
When a motor fails, it can often be repaired, but the decision to repair or purchase a new motor depends on the extent of the damage, cost of repairs, and the availability of spare parts.
Motor Control Basics
Motor control allows operational control of electrical motors in various environments.
Motor control circuits provide a safe way to operate electrical motors. Back when motor control circuits were in their infancy, it would have been common to see a simple disconnect switch that would be used to turn on and off a motor. Depending on the size of the motor and how much voltage was required, operating this disconnect would have been dangerous, with a very high possibility of arcing or electrocution. Not to mention that when the disconnect was actuated, the large amount of inrush current would have damaged the motor over time.
In today's motor control circuits, there are a few common pieces of hardware.
A circuit breaker is used to protect the motor and any hardware downstream. A contactor and an overload relay are connected together and function in tandem to allow for remote and safe operation of the motor. The contactor functions much like a relay, allowing for a smaller electrical circuit to remotely close the motor contacts, starting the motor. The overload relay is designed to protect the motor in the case of a prolonged overcurrent event. These two devices are wired in series, so that if the overload relay detects an overcurrent event, the contactor will open the motor contacts, shutting off power to the motor.
The other two most common types of motor control hardware are a soft starter and a Variable Frequency Drive (VFD).
Both of these devices function in a similar way to the motor circuit with some added functions. The soft starter is designed to reduce large inrush current to the motor upon startup. This “soft starting” of the motor will prolong its life and allow for safer operation. The VFD performs the soft start functions, but also allows for speed control of the motor. This speed control is critical in many different environments and has made VFDs one of the most common and safe to use motor control circuits today.