
IEEE 841 Premium Motors

IEEE 841 Premium Motors are electric motors that are designed to meet specific performance and durability standards set forth by the Institute of Electrical and Electronics Engineers (IEEE). These motors are used in a variety of industrial applications where reliable and efficient performance is critical. IEEE 841 Premium Motors are used in harsh or extreme environments that may be subject to moisture, dust, corrosive chemicals, high or low temperatures, or other environmental factors that can affect the performance and lifespan of a motor. These environments include oil refineries, chemical processing plants, paper mills, water treatment facilities, and other heavy industrial settings. IEEE 841 Premium Motors are built to withstand these harsh conditions and are designed to provide superior performance, energy efficiency, and reliability. They typically have features such as rugged cast iron frames, corrosion-resistant coatings, and heavy-duty bearings, which make them well-suited for these challenging applications.
Products
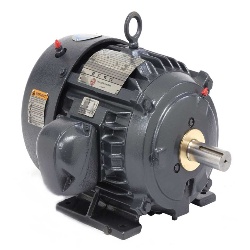
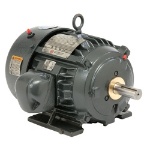
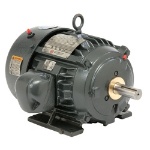
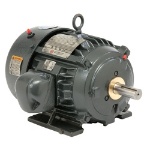
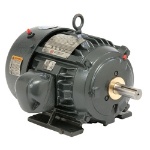
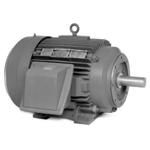






More Information about IEEE 841 Motors
Toshiba EQP Global 841 Motors are designed for other severe duty applications in the gas, mining, mill, oil and chemical industries. The Class I Division 2 and vacuum pressure impregnated (VPI) Class F insulation provides additional reliability to withstand harsh environments. The IP56 protection includes non-contacting labyrinth seals on the DE and ODE to provide increased moisture and dust protection. According to the IEEE 841 standard, severe duty motors should be able to perform at ambient temperatures from -13 degrees F to 104 degrees F and altitude up to 3281 feet. They should have full voltage starting and tolerate humid, corrosive or salty environments. They are typically made of cast iron with a ruggedized frame to resist vibration, and painted with corrosive resistant paint.
Baldor-Reliance 841XL Motors are designed to meet and exceed the requirements of IEEE 841. This Industry standard was created for the Petroleum and Chemical industry to improve the reliability, efficiency and performance of Severe Duty motors used in severe duty environments. Other severe process industries like Forest Products have also adopted using the IEEE 841 spec as it helps promote uniform motor specification and reduce total cost of ownership.
FAQs
What NEMA (National Electrical Manufacturers Association) enclosures come with IEEE 841 motors?
IEEE 841 does not explicitly specify the use of a certain NEMA enclosure. However, given the environments these motors are expected to operate in, they are often manufactured with NEMA-rated enclosures that provide high levels of protection.
What is meant by premium efficiency?
"Premium efficiency" is a term used to classify electric motors that have been designed to achieve higher levels of efficiency compared to standard models. This categorization is often defined by international standards and regulations.
Motor Starters, Soft Starters and VFDs
Motor Starters
Motor starters safely start and stop a motor in industrial applications. They are designed with a contactor, overload and circuit protection. They are used when basic motor control is required, where torque on the motor is not a concern and speed control is not needed. The advantages of motor starters include: lower cost, allows for remote operation, allows for monitoring of motor state (with the use of auxiliary contacts) and they are safe and efficient. The disadvantages include: high inrush current that can cause fuses to blow and breakers to trip if the inrush is too high, and the starter will allow a full torque to start the motor which can cause the motor to ramp up to full speed very quickly potentially causing the motor to wear and degrade prematurely.
Soft Starters
Soft starters protect motors from inrush current by gently ramping up the motor to full speed. They provide all of the same functions as a traditional motor starter. The advantages of soft starters include: they are less expensive than a VFD when only startup control is needed, they are a smaller system than a VFD where space is a concern and they prevent unwanted torque upon startup, prolonging the life of the motor. The disadvantages include: they are more expensive than a traditional motor starter and they do not allow for full speed control.
VFDs
A Variable Frequency Drive (VFD) allows for the slow ramp up of a motor during startup and the slowing down of the motor during shutdown. It also allows for full speed control during the entire run cycle of the motor. VFDs provide the same functions as both the traditional motor starters and soft starters. The advantages of VFDs include: full speed control (start, stop and in-between), more custom control and monitoring, energy savings due to efficient motor usage and less wear and tear on the motors. The disadvantages include: they are more expensive and larger than other motor control options and they generate heat that may require fans or AC units.