
Sensor Cables & Connectors
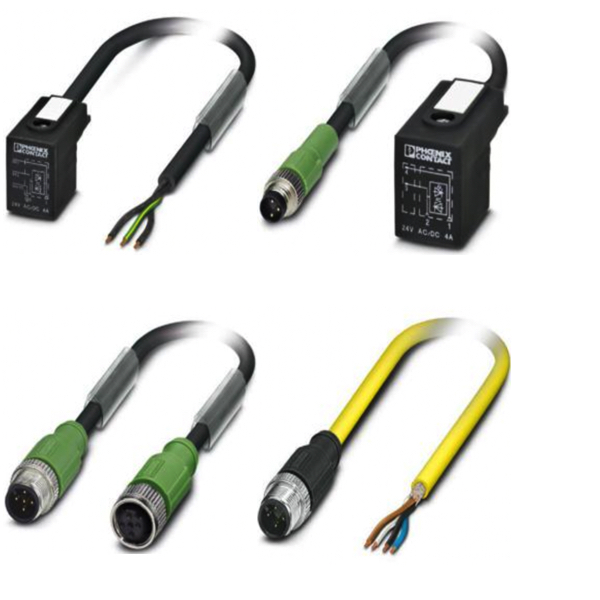
Sensor cables are used in many essential applications, such as those related to monitoring and controlling processes. These cables are carefully designed and manufactured to optimize the overall performance of the cable–sensor–equipment system. There are, of course, many important pieces to the "system" mentioned, but the cables are an especially important piece because any issues that arise with the cable can have a detrimental effect on the overall performance of the system.
It is extremely important to take into account cable length when one is selecting a sensor cable. You want to be certain the decision you make will be suitable for the application at hand. If the cable is too short, it limits where you can put your sensors. If the cable is much too long, it can result in signal loss or even interference.
When customers in the wire and cable industry are in need of cables for their sensors, they seek those that are appropriate for their sensor's job—whether it's measuring speed, temperature, or voltage. Nothing is more important than having a cable that, at the very least, won't harm their sensors or the devices those sensors are connected to. In some cases, a cable that is incompatible with the electronics of a particular sensor or the apparatus it's being used in can lead to a cascading, damaging effect. Even a cable that's undersized in a certain gauge or doesn't have enough or the right shielding can cause severe performance issues.
Subcategories
Products
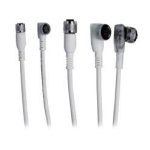
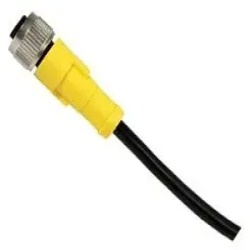
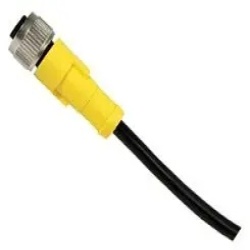
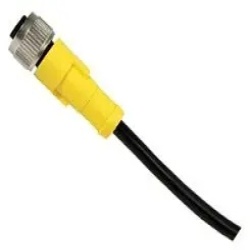
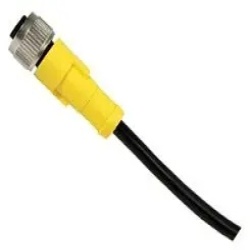
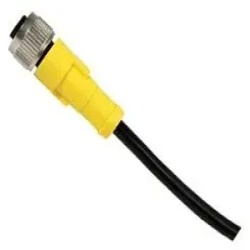
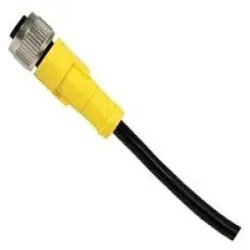
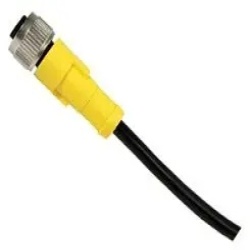
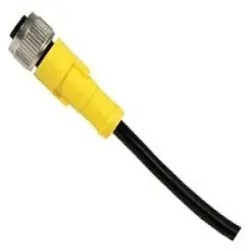
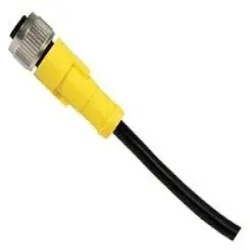
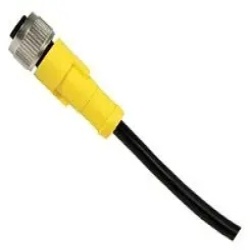
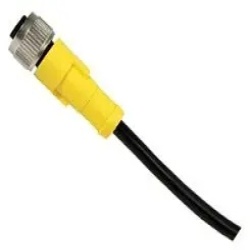
FAQs
What custom sensor cable provides optimum performance in measuring temperature range?
A custom thermocouple sensor cable, often made with high-temperature insulation like PTFE or fiberglass, provides optimum performance in measuring a wide temperature range accurately.
Which brand cables provide easy compatibility in existing sensor cable systems?
Brands like Phoenix Contact and Weidmuller provide cables that offer easy compatibility with existing sensor cable systems due to their high-quality standards and versatile design.
Analog vs Digital Control Signals: The Basics
Digital Signals
Digital signals are represented in either a true or false. There is no gray area with digital signals. An example of this might be a light switch. A light switch is either on or off. Another example of this might be a motor that is running or not running. Digital signals can be generated with both AC and DC circuits with varying voltages, currents and resistance. Some practical examples of using digital signals in an industrial environment might be if a pump is running or not running or a whether a valve is open or closed.
Analog Signals
Analog signals convey information in the form of a range. A light switch might be on or off as a digital signal, but a dimmer switch would be an analog signal. It can be on or off, but it can also be somewhere in between. A practical example of using analog signals in an industrial environment would be if there is a need to measure the level of a tank; whether it's full, empty or somewhere in between. Analog signals can take many different forms with some of the more common being a 4 to 20 milliamp signal or a 0 to 5 or 0 to 10 volt signal.
Communication
Communication in a device can either be sent or received. Whether that data is sent or received depends on the type of information. Is there a need to monitor the status of something? If so, an input needs to be received about that information. Is there a need to control something? If so, an output needs to be sent about what needs to occur. Receiving inputs and setting outputs are both things that can be accomplished by using both digital and analog signal types. Therefore, the signals are referred to as analog outputs (AO), analog inputs (AI), digital inputs (DI) or digital outputs (DO).