
RPM Motors
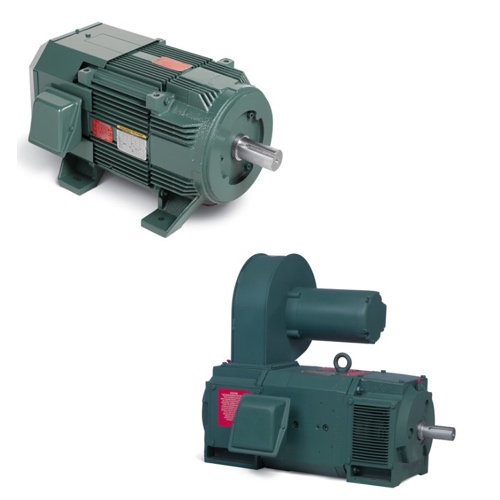
Electric motors that creates power using rotational force are called an RPM electric motors. These motors are designed to rotate at high speeds and can be either single-phase or three-phase. A single-phase motor uses just one power source and is usually found in light-duty applications; a three-phase motor needs three power sources and serves those demanding, heavy-duty jobs where more oomph is required. You might think of an RPM motor as something you find in an elevator, but these electrically powered machines have more to their repertoire than just that. They generate up to 200 horsepower and are used in lots of applications: pumps, compressors, conveyor systems, and so on.
An RPM electric motor's critical parts are the stator, magnetic field generator, and the rotor that spins and produces the change of magnetic field, which, in turn, creates the mechanical output. The smooth operation of these mechanisms—allowance for nearly frictionless spinning of the stator's winding—makes for a more efficient packaging and use of the generated electricity.
Products
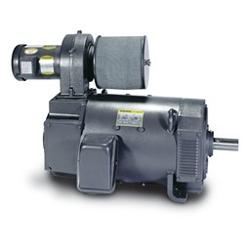

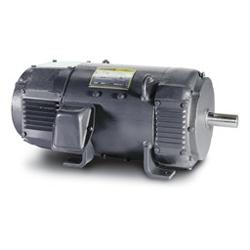
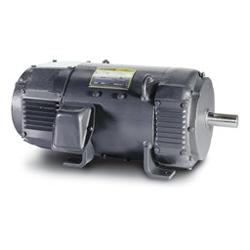
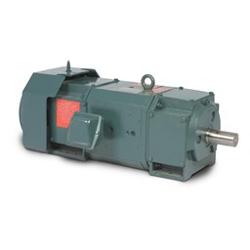
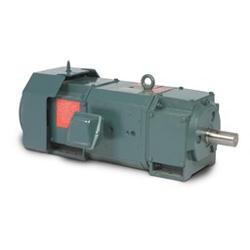
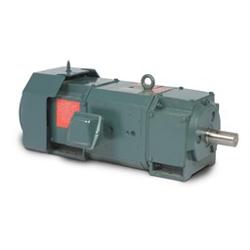
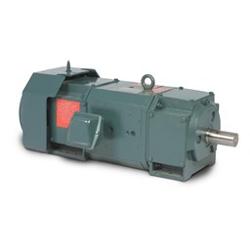
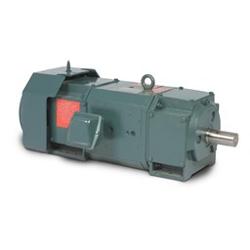
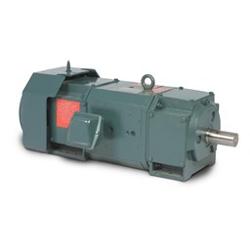
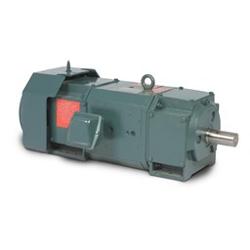
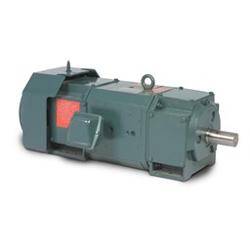
FAQs
What type of electric motor uses electromagnetic induction?
An induction motor, also known as an asynchronous motor, uses electromagnetic induction to generate mechanical power.
What other factors are involved in preventing an RPM motor from overheating?
Other factors involved in preventing an RPM motor from overheating include proper ventilation and cooling systems, high-quality insulation materials, efficient design to reduce electrical losses, and thermal overload protection mechanisms.
Motor Starters, Soft Starters and VFDs
Motor Starters
Motor starters safely start and stop a motor in industrial applications. They are designed with a contactor, overload and circuit protection. They are used when basic motor control is required, where torque on the motor is not a concern and speed control is not needed. The advantages of motor starters include: lower cost, allows for remote operation, allows for monitoring of motor state (with the use of auxiliary contacts) and they are safe and efficient. The disadvantages include: high inrush current that can cause fuses to blow and breakers to trip if the inrush is too high, and the starter will allow a full torque to start the motor which can cause the motor to ramp up to full speed very quickly potentially causing the motor to wear and degrade prematurely.
Soft Starters
Soft starters protect motors from inrush current by gently ramping up the motor to full speed. They provide all of the same functions as a traditional motor starter. The advantages of soft starters include: they are less expensive than a VFD when only startup control is needed, they are a smaller system than a VFD where space is a concern and they prevent unwanted torque upon startup, prolonging the life of the motor. The disadvantages include: they are more expensive than a traditional motor starter and they do not allow for full speed control.
VFDs
A Variable Frequency Drive (VFD) allows for the slow ramp up of a motor during startup and the slowing down of the motor during shutdown. It also allows for full speed control during the entire run cycle of the motor. VFDs provide the same functions as both the traditional motor starters and soft starters. The advantages of VFDs include: full speed control (start, stop and in-between), more custom control and monitoring, energy savings due to efficient motor usage and less wear and tear on the motors. The disadvantages include: they are more expensive and larger than other motor control options and they generate heat that may require fans or AC units.