
Enclosure Pressure, Humidity & Condensation
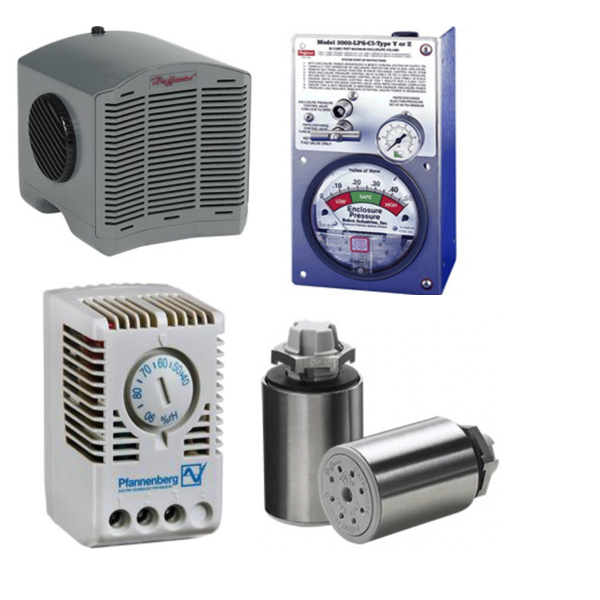
Enclosure pressure, particularly in electrical enclosures, plays a significant role in maintaining the integrity and functionality of electrical equipment. Applying positive internal pressure within the enclosure, often using inert gas or simply clean, dry air, helps in preventing the ingress of flammable gases, dust, and moisture, which are potential hazards in various industrial environments. This pressurization is essential in both indoor and outdoor enclosures, especially where the risk of explosive atmospheres or high ambient humidity levels exists.
Maintaining a positive pressure inside an enclosure means that the internal pressure is slightly higher than the surrounding atmosphere. This prevents moist air from entering the enclosure and creating conditions conducive to condensation. Condensation within an enclosure can lead to water droplets forming on electrical components, raising the risk of short circuits and corrosion. To combat this, methods such as applying corrosion inhibitor sprays and installing air conditioners or heaters are used. Heaters help in regulating the enclosure's internal temperatures, reducing the relative humidity inside and preventing condensation.
Subcategories
Products
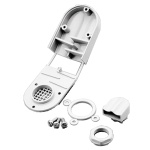
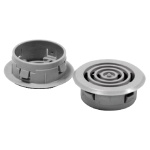
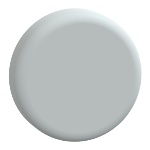


![Hoffman ATEX3003YZVM Large-Volume ATEX Purge System Type Y, Z and Ex [pz], 90CF, Vertical Mount](/images/product/icon/Hoffman-ATEX3003YZVM.jpg)
![Hoffman ATEX3003YZHM Large-Volume ATEX Purge System Type Y, Z and Ex [pz], 90CF, Horizontal Mount](/images/product/icon/Hoffman-ATEX3003YZHM.jpg)

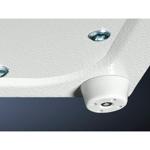



More Information about Enclosure Pressure, Humidity & Condensation Protection
In environments where the temperature and humidity fluctuate, it's essential to continuously monitor the air inside the enclosure. Devices that automatically trigger the purging process or control the flow of protective gas can be installed. This ensures that the air within the enclosure remains dry and at a constant flow, effectively preventing condensation.
The concept of purging and pressurization in enclosures is typically regulated by standards such as the ATEX Directive or IEC standards, ensuring safety in hazardous environments. These standards dictate the level of pressurization required and the types of gases or air that can be used for maintaining a safe environment within the enclosure.
Another aspect of managing humidity and condensation is ensuring proper ventilation while maintaining the required pressure and moisture levels. This could involve the use of ventilation systems that allow air to circulate within the enclosure while keeping moisture and hazardous gases out.
FAQs
How does air temperature affect a pressurized enclosure?
Air temperature can significantly affect a pressurized enclosure in several ways. Firstly, an increase in temperature typically causes the air inside the enclosure to expand, leading to an increase in pressure if the volume of the enclosure is fixed. Conversely, a decrease in temperature can cause the air to contract, resulting in a decrease in pressure within the enclosure, assuming no air is added or removed.
Purge System Basics
3 common reasons to use purge systems
They allow electrical enclosures to be installed in hazardous areas without the need for explosion proof enclosures.
They recycle the air inside of an enclosure, reducing the internal temperature.
They help reduce the effects of corrosion on components housed within the enclosure.
How does a purge system work?
Purge systems use incoming air from a supply line, solenoid valves, pressure gauges and pumps, to constantly maintain a positive pressure inside an enclosure. This prevents any flammable gases from entering the enclosure potentially causing an ignition event to occur. By maintaining a positive pressure within the enclosure, moisture and corrosive gases are also prevented from entering the enclosure and damaging components. Most purge systems will ensure that the air inside the enclosure is recycled a certain amount of times within a given time period. This air recycle function assists in maintaining a cooler temperature within the enclosure.