
VFD Variable Frequency Drives

Variable frequency drives (VFDs) are advanced electronic devices used to control electric motors by altering the supply of power to them. They regulate not just speed but also torque. They are critical in applications where precise motor control is necessary because they save energy, improve a process's controllable variables, and reduce stress on both the motor and its application's components (like gears). VFDs are used across many industries for these advantages.
VFDs have several benefits, but the most significant one is certainly energy efficiency. Motor speed can be adjusted to exactly match load demands—something a traditional motor cannot achieve. So, if you have applications where motors don’t need to run at full speed all the time (like in HVAC systems, pumps, and fans), VFDs save energy and reduce running costs; they also lead to cost savings during installation.
Subcategories
Products
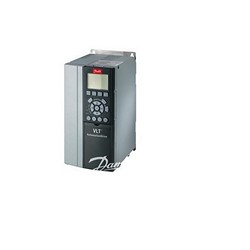
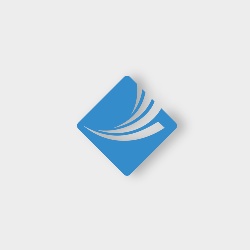
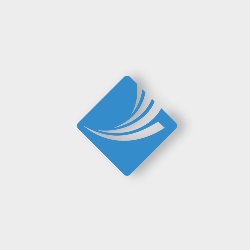
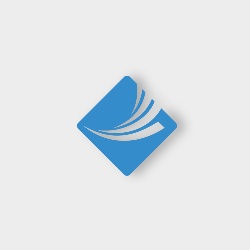
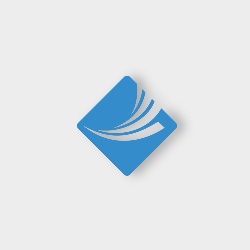
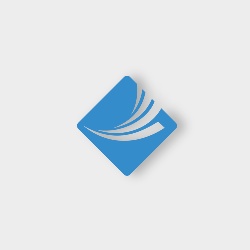
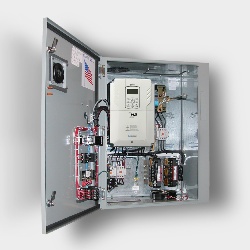
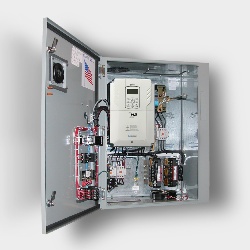
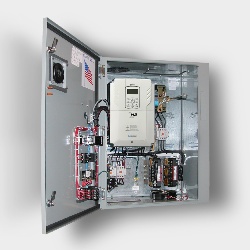
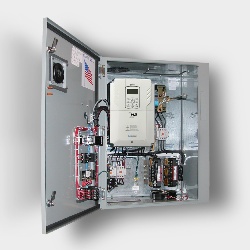
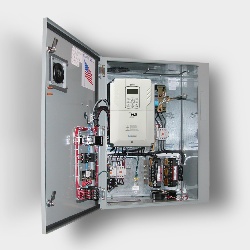
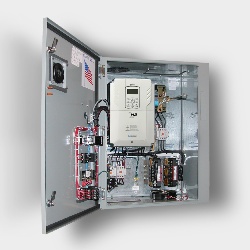
FAQs
Can the output voltage of a variable speed drive provide enough constant torque to control an induction motor?
Yes, the output voltage of a variable speed drive can provide enough constant torque to control an induction motor effectively.
Do medium voltage AC drives have insulated gate bipolar transistors?
Yes, medium voltage AC drives often use insulated gate bipolar transistors (IGBTs) for efficient and precise control of motor speed and torque.
What kind of energy consumption does variable speed drives and motor controllers have?
Variable speed drives and motor controllers typically have lower energy consumption compared to traditional fixed-speed motor controllers, as they adjust the motor's speed and torque to match the load requirements, optimizing energy use.
Do single phase DC drives provide enough torque control to increase productivity and performance of an industrial machine?
Yes, single-phase DC drives provide sufficient torque control to enhance productivity and performance in industrial machines by delivering precise speed regulation, smooth acceleration, and efficient power management.
Motor Starters, Soft Starters and VFDs
Motor Starters
Motor starters safely start and stop a motor in industrial applications. They are designed with a contactor, overload and circuit protection. They are used when basic motor control is required, where torque on the motor is not a concern and speed control is not needed. The advantages of motor starters include: lower cost, allows for remote operation, allows for monitoring of motor state (with the use of auxiliary contacts) and they are safe and efficient. The disadvantages include: high inrush current that can cause fuses to blow and breakers to trip if the inrush is too high, and the starter will allow a full torque to start the motor which can cause the motor to ramp up to full speed very quickly potentially causing the motor to wear and degrade prematurely.
Soft Starters
Soft starters protect motors from inrush current by gently ramping up the motor to full speed. They provide all of the same functions as a traditional motor starter. The advantages of soft starters include: they are less expensive than a VFD when only startup control is needed, they are a smaller system than a VFD where space is a concern and they prevent unwanted torque upon startup, prolonging the life of the motor. The disadvantages include: they are more expensive than a traditional motor starter and they do not allow for full speed control.
VFDs
A Variable Frequency Drive (VFD) allows for the slow ramp up of a motor during startup and the slowing down of the motor during shutdown. It also allows for full speed control during the entire run cycle of the motor. VFDs provide the same functions as both the traditional motor starters and soft starters. The advantages of VFDs include: full speed control (start, stop and in-between), more custom control and monitoring, energy savings due to efficient motor usage and less wear and tear on the motors. The disadvantages include: they are more expensive and larger than other motor control options and they generate heat that may require fans or AC units.