
Crusher Duty Motors
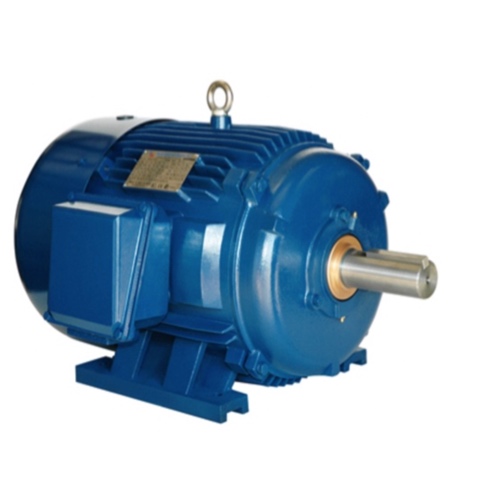
Crusher duty motors are specifically made for and used in the extreme applications found in the mining and rock crushing industry, as well as in cement plants and where belt driven rock crushers are used. These electric motors are usually larger and heavier, owing mostly to cast iron construction, providing reliable performance in severe duty service conditions.
Motors that are meant for crushing duty are usually Totally Enclosed Fan Cooled (TEFC). This kind of motor is really good for keeping out dust, moisture, and other kinds of contaminants. And as a motor, it is reliable because it is made for harsh operating conditions. All these things together make a TEFC motor likely to pull its weight in an application.
Motors intended for use with crushers are designed to supply high starting torques to handle the large inertial load. Equipped with an oversized roller bearing, these motors handle high radial and axial loads, which is crucial for torque applications feeders, screen decks, augers, and screw conveyors. This is a key requirement for ground mining bulk material crushers, but it's also crucial for other kinds of equipment in the cement mining industry, like pellet mills, grinders, pellet presses, and conveyor belts.
Products




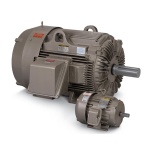







FAQs
What is an insulated ode bearing and how does it help bearing temperature?
An insulated ODE (opposite drive end) bearing is designed to prevent electrical currents from passing through the bearing, reducing electrical discharge that can cause excessive heat and thus helping to maintain optimal bearing temperature and prolong bearing life.
Motor Starters, Soft Starters and VFDs
Motor Starters
Motor starters safely start and stop a motor in industrial applications. They are designed with a contactor, overload and circuit protection. They are used when basic motor control is required, where torque on the motor is not a concern and speed control is not needed. The advantages of motor starters include: lower cost, allows for remote operation, allows for monitoring of motor state (with the use of auxiliary contacts) and they are safe and efficient. The disadvantages include: high inrush current that can cause fuses to blow and breakers to trip if the inrush is too high, and the starter will allow a full torque to start the motor which can cause the motor to ramp up to full speed very quickly potentially causing the motor to wear and degrade prematurely.
Soft Starters
Soft starters protect motors from inrush current by gently ramping up the motor to full speed. They provide all of the same functions as a traditional motor starter. The advantages of soft starters include: they are less expensive than a VFD when only startup control is needed, they are a smaller system than a VFD where space is a concern and they prevent unwanted torque upon startup, prolonging the life of the motor. The disadvantages include: they are more expensive than a traditional motor starter and they do not allow for full speed control.
VFDs
A Variable Frequency Drive (VFD) allows for the slow ramp up of a motor during startup and the slowing down of the motor during shutdown. It also allows for full speed control during the entire run cycle of the motor. VFDs provide the same functions as both the traditional motor starters and soft starters. The advantages of VFDs include: full speed control (start, stop and in-between), more custom control and monitoring, energy savings due to efficient motor usage and less wear and tear on the motors. The disadvantages include: they are more expensive and larger than other motor control options and they generate heat that may require fans or AC units.