
Safety Gateways
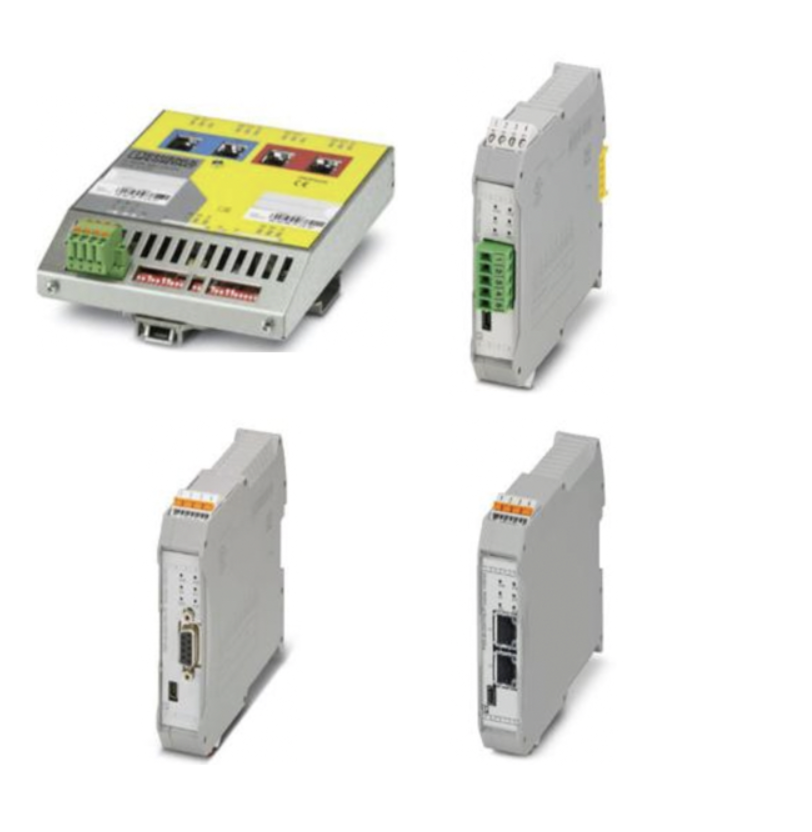
A gateway is a hardware device that joins two networks so that devices on one network can communicate with devices on another network. It serves as an entry and exit point for a network as all data traffic passes through it before being routed. Ethernet gateways are devices that allow protocol conversion to an EtherNet/IP network. In automated industrial or SCADA (Supervisory Control and Data Acquisition) systems, Ethernet gateways often facilitate connecting serial devices to an Ethernet network, allowing multiple connections and a conversion between fieldbus protocols such as Modbus or PROFIBUS (Process Filed Bus) to EtherNet/IP or PROFINET (Process Field Net).
Profibus is a fieldbus network designed for communication between PLCs and devices. This is accomplished through a master-slave communication, where the master (PLC) has multiple slave devices (sensors, motors, actuators, etc) communicating through a single cable. Profibus can handle large amounts of data at high speeds and can serve the needs of large installations. Profinet is similar to Profibus but uses Ethernet for its communication. Profisafe is software that provides additional safety over the bus in Profinet (of Profibus) networks. It ensures the integrity of failsafe signals transmitted between safety devices and a safety controller.
Products






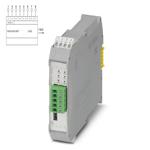
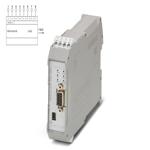


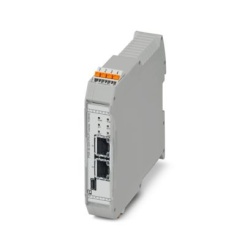
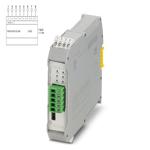
More Information about Safety Gateways
The PSRmodular configurable safety systems makes it possible to implement small applications with three safety functions as well as applications with up to 160 IOs. It allows for monitoring safety functions, such as safety door locks, light grids, emergency stop signals, shut-off mats, direction of rotation and speed. PSRmodular gateways connect a PRS-M basic module to a higher-level controller.
What is "Fail Safe"?
What is fail safe?
Fail safe is to cause a piece of machinery or other mechanism to revert to a safe condition in the event of a breakdown or malfunction. In regards to electrical equipment, this would be a state where no power exists. In other words, when the device fails, power would no longer be running to that piece of equipment.
So how is this done?
An electrical motor, for example, can be switched on and off with some kind of motor starter. This motor starter will commonly consist of a contactor, which is a normally open set of contacts capable of providing the necessary power to the motor, as well as an overload protection device. The overload is designed to monitor the power and ensure that any overcurrent event does not destroy the motor or allow the contacts on the contactor to be welded shut. Upstream of the motor starter will be some kind of circuit protection device, commonly a breaker or fuse. This device also protects against overcurrent, but offers additional protection against large voltage spikes, like a lightning strike or power surge. With all of these devices upstream of the motor, if the motor were to begin to overheat, the overload would cause the contacts on the contactor to open, switching power off to the motor. In this instance, the motor failed, but did so in a safe manner, or safe state.