
Severe Duty Motors
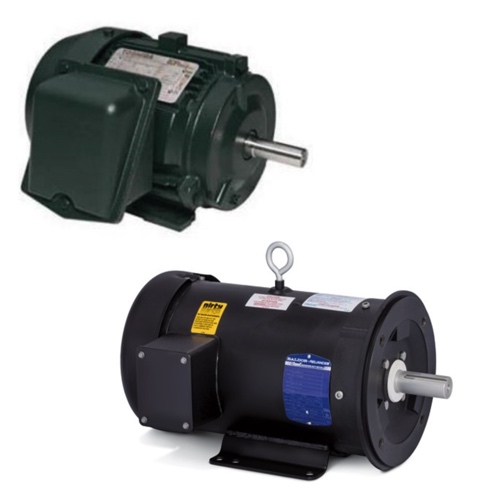
Typically, severe duty motors are meant to run in severe environmental operating conditions such as mines, chemical plants, wastewater treatment plants, and even in waste management facilities. Standard motors aren't tough enough for these harsh industrial processing applications; the severe duty version uses different technologies (mechanical and electrical) and the totally enclosed fan cooled motor keeps the inner parts from getting dirty and shedding normally functioning parts.
Severe-duty motors are built with insulation systems to withstand the high voltage spikes and thermal stresses that come with the job, thereby offering the long-term reliability required in demanding duty cycles. Motors used in hazardous locations resist demands that degrade windings and the overall strength of their electrical design. In a severe duty motor—as in any electric motor—engineers strive to reduces energy consumption and provide exceptional performance.
Products
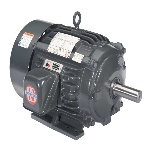
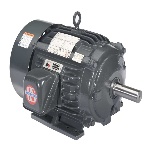
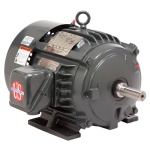
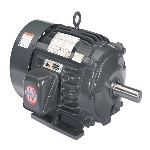



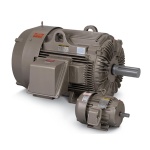




More Information about Severe Duty Motors
Baldor-Reliance Severe Duty motors have three guiding principles behind each design: 1. Safer installation: • Rugged lifting provisions • Oversized conduit box 2. Safer connection: • Clamp-type grounding lug • Permanently labeled color leads 3. Safer operation.
FAQs
Does cast iron construction and gear reducers contribute to severe duty ratings for inverter duty applications?
Yes, cast iron construction and gear reducers contribute to severe duty ratings for inverter duty applications by enhancing the motor's durability, strength, and ability to handle high torque and harsh conditions.
What do severe duty ratings protect against in chemical industries and petrochemical plants?
Severe duty ratings protect against corrosive chemicals, extreme temperatures, moisture, dust, and hazardous contaminants in chemical industries and petrochemical plants, ensuring reliable motor performance and longevity in harsh operating conditions.
Motor Starters, Soft Starters and VFDs
Motor Starters
Motor starters safely start and stop a motor in industrial applications. They are designed with a contactor, overload and circuit protection. They are used when basic motor control is required, where torque on the motor is not a concern and speed control is not needed. The advantages of motor starters include: lower cost, allows for remote operation, allows for monitoring of motor state (with the use of auxiliary contacts) and they are safe and efficient. The disadvantages include: high inrush current that can cause fuses to blow and breakers to trip if the inrush is too high, and the starter will allow a full torque to start the motor which can cause the motor to ramp up to full speed very quickly potentially causing the motor to wear and degrade prematurely.
Soft Starters
Soft starters protect motors from inrush current by gently ramping up the motor to full speed. They provide all of the same functions as a traditional motor starter. The advantages of soft starters include: they are less expensive than a VFD when only startup control is needed, they are a smaller system than a VFD where space is a concern and they prevent unwanted torque upon startup, prolonging the life of the motor. The disadvantages include: they are more expensive than a traditional motor starter and they do not allow for full speed control.
VFDs
A Variable Frequency Drive (VFD) allows for the slow ramp up of a motor during startup and the slowing down of the motor during shutdown. It also allows for full speed control during the entire run cycle of the motor. VFDs provide the same functions as both the traditional motor starters and soft starters. The advantages of VFDs include: full speed control (start, stop and in-between), more custom control and monitoring, energy savings due to efficient motor usage and less wear and tear on the motors. The disadvantages include: they are more expensive and larger than other motor control options and they generate heat that may require fans or AC units.