
Cable Ladder Rack Systems
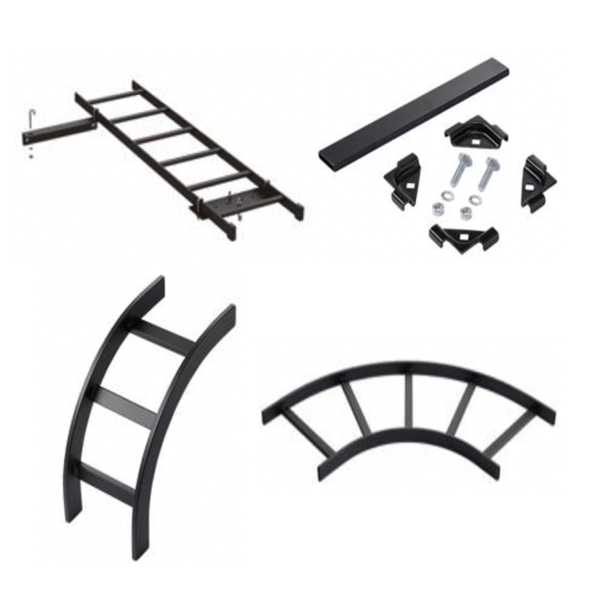
Cable ladder rack systems offer a trustworthy and effective alternative when it comes to managing cables in a number of different applications, from data centers to factories. The full line of racks are fully welded and made of sturdy materials that enable them to support a much greater load of cables than leaning or inefficient wall-mounted systems. Accessibility proves to be a recurring theme across the advantages of these systems.
When selecting a cable ladder rack assembly from reputable manufacturers, you ensure that what you're getting is UL-listed for quality and compliance with the many applicable industry standards. The ladder rack itself is simple enough. It consists of longitudinal members, or "rungs," that span between the vertical supports. This is why the assembly is often called a "ladder." However, the ensemble is usually much more than just a section of ladder. It may contain: 1. Various bends and offsets to route cable past obstructions while still in a code-compliant manner; 2. Various add-on options, like a safety net across the front of the assembly, to help stop falling objects.
Products

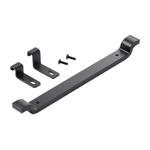







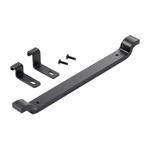


More Information about Cable Ladder Rack Systems
Ladder racks provide support for large amounts of cabling and offer a clear path for the cables to keep them organized. They have a highly scratch resistant, durable black powder coat finish and the external width of runs allow different configurations and different size cables to fit them. Most ladder rack kits come with support brackets, which is good because putting up a path for all the cables is pointless if you can’t support it at various intervals along the way. The parts in the kits come well packaged, ensuring that they’re in good shape when it’s time to install a major run of cable. Runway options go with the ladder racks as well.
FAQs
What is the maximum load with minimal deflection of most popular brands of cable ladder rack systems that are UL classified?
Most popular brands of UL-classified cable ladder rack systems have a maximum load capacity of 132 pounds per foot with minimal deflection when supported every 5 feet.
4 Best Practices when Fabricating a Control Panel
Use a Larger Enclosure Whenever Possible
This allows room in the panel design to properly space all of the hardware and to install larger wire ducting. Panels that have ample space tend be me more organized, while panels that have everything crammed into a small space tend to be more difficult to work in and are often less organized.
Tap Holes Instead of Using Self-Tapping Screws
It is common for panel builders to use self-tapping screws to save time during the fabrication process. While it can save time, this type of fastener does not always provide the consistent, strong connection that may be needed for the mounted hardware. This is especially true when hardware may need to be removed at some point and then later reattached. Holes that have been tapped prior to hardware installation will offer a stronger, more consistent connection point that will last longer.
Ensure that Wire Ducting is Large Enough
It is very easy to undersize wire ducting when designing a panel. It is important to always plan for wire ducting to have extra room available once all wires have been run through it, including field wires.
When in Doubt, Label it
It is a very good practice to label wires in a control panel, but it is not always required to label the other types of hardware in the panel to meet code. It is important to understand that any operators that may access this panel at a later date may not understand what the hardware in the panel is intended for. To make the panel is as safe as possible, and to allow operators to function in the panel more efficiently, it is a good idea to label everything that may come into question.