
Enclosure Cable Managers
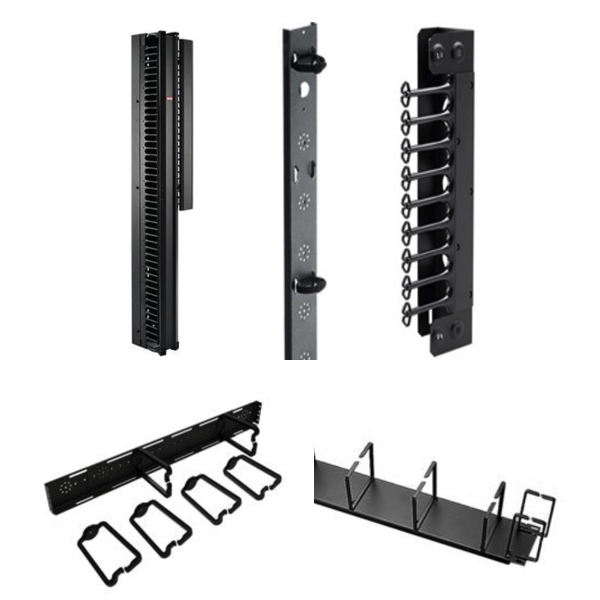
Cable managers are essential components used to organize, protect, and route cables within electrical enclosures, control panels, and server racks. They provide an efficient setup, and they help in reducing the clutter within the cables themselves. The low-profile designs of some cable managers allow them to be placed almost anywhere, so they can be used even where space is tight.
Cable managers reduce the possibility of damage to the individual cables. A cable that is crimped or kinked can quickly be rendered nonfunctional. The simplest of cable managers is nothing more than a tie strap. A slightly more complex cable manager is a series of rings through which a cable may be passed. The more complex managers help not only in routing the cables but also in maintaining the proper relationship among the cables and the equipment they are connected to.
The various types and configurations of these cable management solutions are designed to accommodate specific applications and enclosures of different sizes. They can include a vertical cable manager and a horizontal cable manager that are usually mounted alongside racks or panels. These managers organize cables, provide support, improve airflow and make maintenance more convenient.
Products
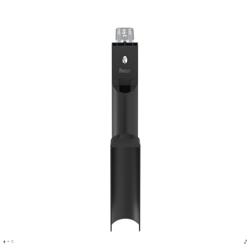
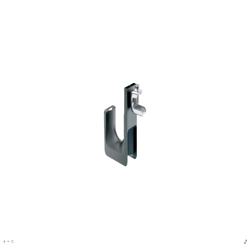
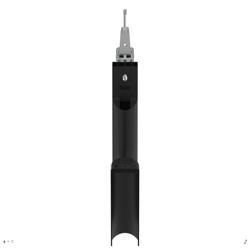
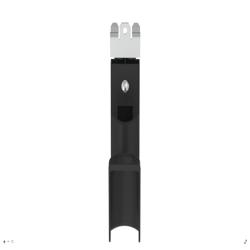
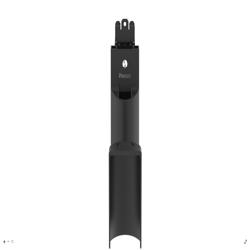
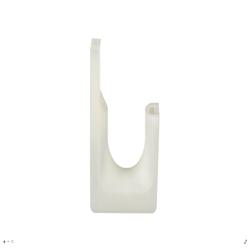
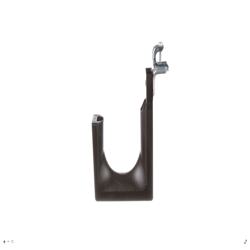
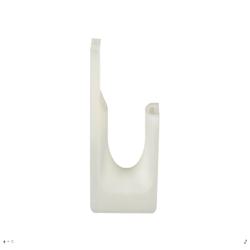
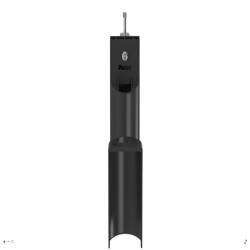
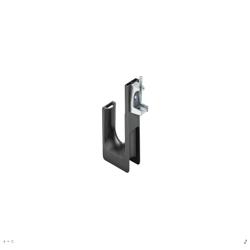
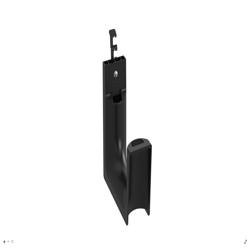
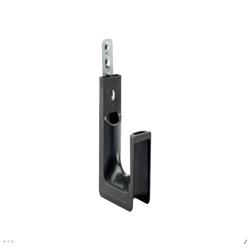
FAQs
Which type of cable managers can be attached to the rear of a cabinet?
Vertical cable managers are typically attached to the rear of a cabinet, providing organized routing and support for cables while maximizing space and ensuring easy access for maintenance and upgrades.
Which cable management product or device uses a rail and grommets?
Cable troughs or cable management rails with grommets are commonly used to organize and protect cables by guiding them through a structured path while preventing damage from sharp edges and reducing cable strain.
Control Panel Fabrication: Best Practices
Use a larger enclosure whenever possible.
This allows room in the panel design to properly space all of the hardware and to install larger wire ducting. Panels that have ample space tend be me more organized, while panels that have everything crammed into a small space tend to be more difficult to work in and are often less organized.
Tap holes instead of using self-tapping screws.
It is common for panel builders to use self-tapping screws to save time during the fabrication process. While it can save time, this type of fastener does not always provide the consistent, strong connection that may be needed for the mounted hardware. This is especially true when hardware may need to be removed at some point and then later reattached. Holes that have been tapped prior to hardware installation will offer a stronger, more consistent connection point that will last longer.
Ensure that wire ducting is large enough.
It is very easy to undersize wire ducting when designing a panel. It is important to always plan for wire ducting to have extra room available once all wires have been run through it, including field wires.
When in doubt, label it.
It is a very good practice to label wires in a control panel, but it is not always required to label the other types of hardware in the panel to meet code. It is important to understand that any operators that may access this panel at a later date may not understand what the hardware in the panel is intended for. To make the panel is as safe as possible, and to allow operators to function in the panel more efficiently, it is a good idea to label everything that may come into question.