
Cable Entry Systems
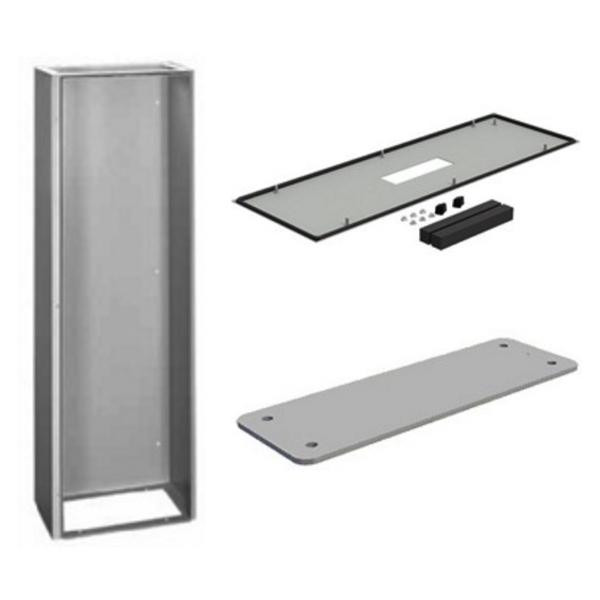
Providing an all-encompassing answer to the problem of how to manage cables as they move through enclosures and control cabinets, cable entry systems serve both aesthetic and practical ends. With a huge range of styles, sizes, and shapes, these solutions cover the gamut from industrial to more sophisticated looks, neatly accommodating wall penetrations. Be it a cable entry plate, a cable entry frame, or some other variant, you can count on these systems to achieve the following: ensure installation is easy; maintain a high degree of strain relief for the cables themselves; and provide a reliably protected access point for the kinds of sensitive electrical equipment.
For applications that need organized cable management, cable glands are used a lot with cable entry systems to deliver strain relief and sealing from the environment. These components serve lots of different cable diameters, making them generally friendly to the wide variety of industrial connectors and other electrical components that reside within enclosures. They definitely work well with assembled and unassembled cables. However, they have been especially useful for unassembled cables, allowing multiple cables to exit one opening while providing the necessary organization, strain relief, and environmental protection that makes these systems worth the money.
Products
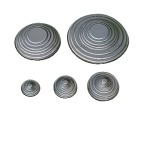
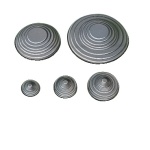
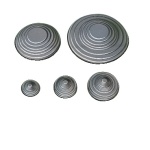
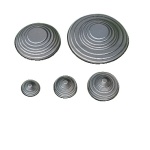
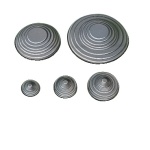
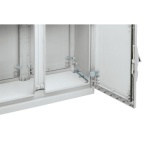
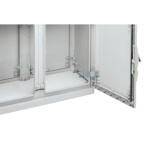
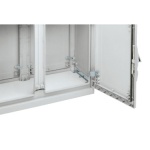
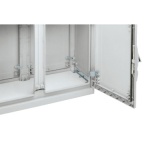
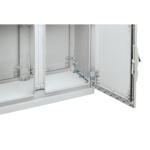
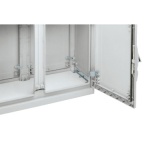
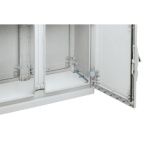
FAQs
Can cable entry systems allow for terminated cables, pre-terminated cables and prefabricated cables to enter one opening in a cable shield while still providing strain relief?
Yes, cable entry systems can allow for terminated cables, non-terminated cables, and pre-assembled cables to enter one opening in a cable shield while still providing strain relief and maintaining a secure, organized, and protected entry point.
Control Panel Fabrication: Best Practices
Use a larger enclosure whenever possible.
This allows room in the panel design to properly space all of the hardware and to install larger wire ducting. Panels that have ample space tend be me more organized, while panels that have everything crammed into a small space tend to be more difficult to work in and are often less organized.
Tap holes instead of using self-tapping screws.
It is common for panel builders to use self-tapping screws to save time during the fabrication process. While it can save time, this type of fastener does not always provide the consistent, strong connection that may be needed for the mounted hardware. This is especially true when hardware may need to be removed at some point and then later reattached. Holes that have been tapped prior to hardware installation will offer a stronger, more consistent connection point that will last longer.
Ensure that wire ducting is large enough.
It is very easy to undersize wire ducting when designing a panel. It is important to always plan for wire ducting to have extra room available once all wires have been run through it, including field wires.
When in doubt, label it.
It is a very good practice to label wires in a control panel, but it is not always required to label the other types of hardware in the panel to meet code. It is important to understand that any operators that may access this panel at a later date may not understand what the hardware in the panel is intended for. To make the panel is as safe as possible, and to allow operators to function in the panel more efficiently, it is a good idea to label everything that may come into question.