
Wireways

Wireways serve as protective enclosures that manage and direct electrical wiring in all types of buildings. They ensure that all kinds of electrical cables are organized and adequately protected from a number of possible environmental hazards. Among the most effective materials used to make wireways are the following: galvanized steel, stainless steel, aluminum, and PVC. Some call the wireway a "raceway" since its primary purpose is to route cables in an organized manner to their destinations.
Wireways are available in a variety of shapes and sizes to accommodate the installation of different types of wiring. They are often modular and can easily be joined and extended to cover a desired distance. Their basic design and the removable cover of their basic model provide access sufficient for the installation, removal, or inspection of wiring both before and after the wiring way is covered. They offer a low profile, which is helpful in achieving a smooth path for the wiring. Their shape is also helpful in achieving a good working draft for cool wiring when sufficient air circulation must be provided for the wiring.
Products
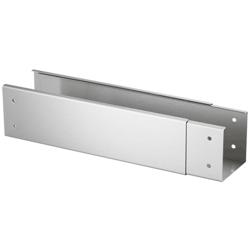
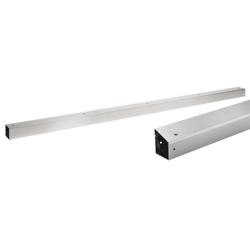
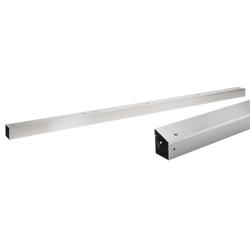
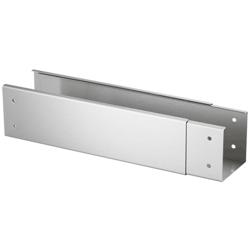
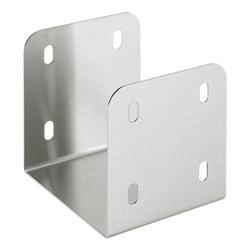
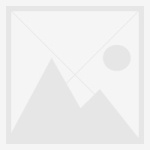
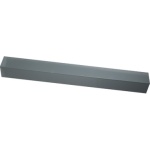
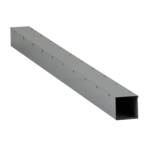
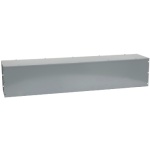
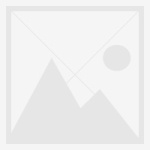
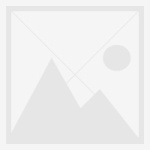
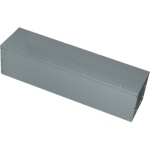
FAQs
Is it possible to request covers for the length of a trough to prevent dust and debris from contaminating power conductors?
Yes, it is possible to request covers for the length of a trough to prevent dust and debris from contaminating power conductors, providing added protection and maintaining a clean and safe wiring environment.
Is it possible to search for a particular quantity of wireways from a manufacturer that is in stock?
Yes, it is possible to search for a specific quantity of wireways from a manufacturer that is in stock through distributors, online catalogs, or the manufacturer's website.
4 Best Practices when Fabricating a Control Panel
Use a Larger Enclosure Whenever Possible
This allows room in the panel design to properly space all of the hardware and to install larger wire ducting. Panels that have ample space tend be me more organized, while panels that have everything crammed into a small space tend to be more difficult to work in and are often less organized.
Tap Holes Instead of Using Self-Tapping Screws
It is common for panel builders to use self-tapping screws to save time during the fabrication process. While it can save time, this type of fastener does not always provide the consistent, strong connection that may be needed for the mounted hardware. This is especially true when hardware may need to be removed at some point and then later reattached. Holes that have been tapped prior to hardware installation will offer a stronger, more consistent connection point that will last longer.
Ensure that Wire Ducting is Large Enough
It is very easy to undersize wire ducting when designing a panel. It is important to always plan for wire ducting to have extra room available once all wires have been run through it, including field wires.
When in Doubt, Label it
It is a very good practice to label wires in a control panel, but it is not always required to label the other types of hardware in the panel to meet code. It is important to understand that any operators that may access this panel at a later date may not understand what the hardware in the panel is intended for. To make the panel is as safe as possible, and to allow operators to function in the panel more efficiently, it is a good idea to label everything that may come into question.