
Enclosure Pressure Purging
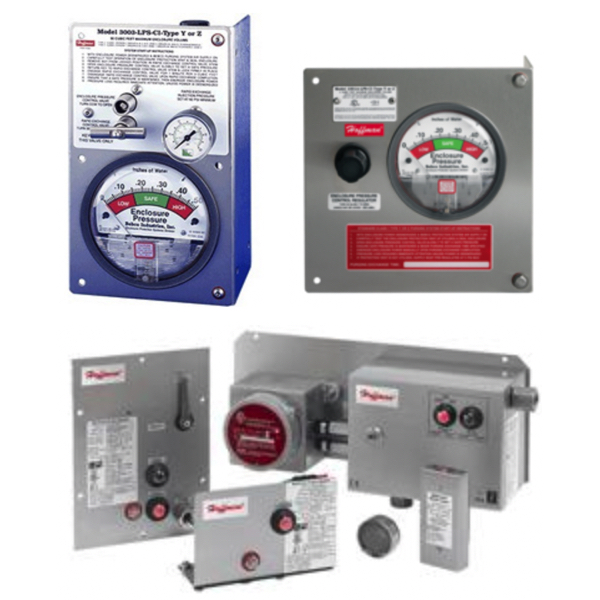
Enclosure pressure purging is a critical process in ensuring the safety and functionality of electrical equipment, especially in hazardous environments. This method involves the use of purge and pressurization systems, which are designed to remove hazardous gas or flammable substances from the enclosure. By introducing an inert gas or clean air, these systems purge the potentially explosive atmospheres that could be present inside the enclosure.
The primary goal of this process is to maintain a positive internal enclosure pressure, which is achieved by continuously supplying protective gas, such as an inert gas, into the enclosure. This positive pressure prevents the ingress of hazardous gases or flammable gases from the surrounding environment. Purge and pressurization systems are especially important in explosion proof enclosures or in areas where there is a high risk of internal explosive gases.
Products


![Hoffman ATEX3003YZVM Large-Volume ATEX Purge System Type Y, Z and Ex [pz], 90CF, Vertical Mount](/images/product/icon/Hoffman-ATEX3003YZVM.jpg)
![Hoffman ATEX3003YZHM Large-Volume ATEX Purge System Type Y, Z and Ex [pz], 90CF, Horizontal Mount](/images/product/icon/Hoffman-ATEX3003YZHM.jpg)




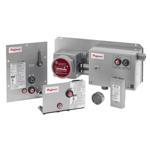


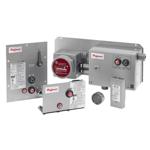
More Information about Enclosure Pressure Purging
These systems work by first initiating an initial purge, which clears any hazardous or flammable gas from the enclosure. Following the purge, the enclosure is pressurized to maintain a constant flow of protective gas. This pressurization helps to create a barrier against the entry of hazardous gases from the outside, thus protecting the internal equipment.
The use of protective gas supply, such as an inert gas supply, is a key component in these systems. Inert gases are preferred as they do not react with the electrical components or with other potentially explosive materials within the enclosure. Additionally, the system often includes features for leakage compensation, ensuring that the positive pressure inside the enclosure is maintained even if there are minor leaks.
The design of pressurization systems takes into account the specific needs of the electrical enclosures they protect. This includes considerations for the size of the enclosure, the type of hazardous gases or flammable substances present, and the requirements for safe operation in hazardous locations. The systems are often controlled by a control unit, which manages the purge flow rate and the maintenance of positive pressure, ensuring both the safety of the protected equipment and compliance with safety standards like those set by the National Fire Protection Association.
Enclosure pressure purging, through the use of purge and pressurization systems, is a vital safety measure for electrical enclosures in hazardous areas. By purging hazardous gases and maintaining a protective atmosphere of inert gas or clean air, these systems safeguard electrical equipment from the risks of explosion or fire, while ensuring continuous and safe operation in challenging environments.
FAQs
While installing electrical equipment in a sealed enclosure, what is done with the enclosure pressurization system?
When installing electrical equipment in a sealed enclosure, the enclosure pressurization system is first activated to conduct an initial purge, ensuring that any hazardous or flammable substances inside are removed. After purging, the system maintains a continuous positive internal enclosure pressure to prevent external hazardous gases from entering. Throughout the process, the pressure within the enclosure is monitored to ensure it remains at a safe level.
What do pressurization systems purge?
Pressurization systems purge potentially hazardous gases and vapors from the enclosure, replacing them with clean, non-hazardous air or inert gas. This ensures that the internal environment of the enclosure is free from explosive or flammable atmospheres, providing a safe area for electrical equipment to operate.
Purge System Basics
3 common reasons to use purge systems
They allow electrical enclosures to be installed in hazardous areas without the need for explosion proof enclosures.
They recycle the air inside of an enclosure, reducing the internal temperature.
They help reduce the effects of corrosion on components housed within the enclosure.
How does a purge system work?
Purge systems use incoming air from a supply line, solenoid valves, pressure gauges and pumps, to constantly maintain a positive pressure inside an enclosure. This prevents any flammable gases from entering the enclosure potentially causing an ignition event to occur. By maintaining a positive pressure within the enclosure, moisture and corrosive gases are also prevented from entering the enclosure and damaging components. Most purge systems will ensure that the air inside the enclosure is recycled a certain amount of times within a given time period. This air recycle function assists in maintaining a cooler temperature within the enclosure.