
Reversing Combination Starters

Reversing combination starters are motor control devices that combine various components into a single enclosure for controlling and protecting electric motors in reversing applications. Unlike non-reversing combination starters, reversing combination starters allow for the control and reversal of motor rotation. They are used in applications where the motor needs to change direction, such as conveyor systems, cranes, and certain types of machinery.
Reversing combination motor starters include motor starters, which consist of contactors and overload relays. The contactor controls the power supply to the motor and enables the direction of rotation to be reversed, while the overload relay protects the motor against overcurrent conditions.
NEMA reversing combination starters are designed and manufactured in accordance with NEMA standards to ensure safe and reliable motor control. They undergo testing to meet specific performance and safety requirements.
Products
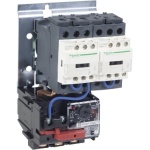
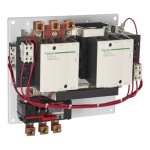
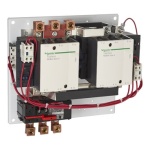
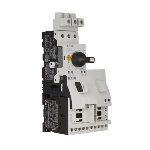
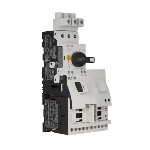
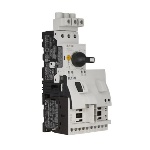
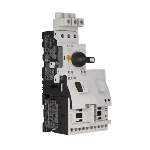
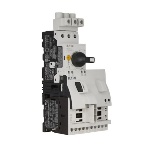
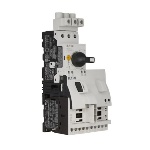
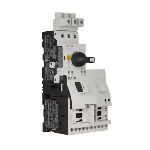
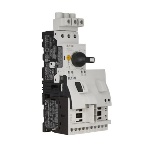
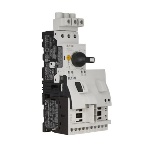
More Information about Reversing Combination Starters
Similar to non-reversing combination starters, reversing combination starters are housed in a single enclosure that contains all the necessary components. The enclosure provides a safe and organized space for the components and ensures compliance with relevant safety standards.
Overload Protection: Overload relays within the reversing combination starter provide protection against excessive current. They monitor the motor's current and trip the starter if the current exceeds a predefined threshold, helping to prevent motor damage.
Short Circuit Protection: Reversing combination starters are equipped with short circuit protection, typically in the form of a circuit breaker or fuses. These components interrupt the power supply in the event of a short circuit fault, safeguarding the motor and electrical system.
Control and Power Wiring: Reversing combination starters facilitate the proper wiring of control circuits and power supply to the motor. They ensure that the control signals and power connections are correctly configured for the desired motor direction and provide a convenient and organized wiring solution.
NEMA Sizes: Reversing combination starters are available in various NEMA sizes, such as Size 0, Size 1, Size 2, and so on. The appropriate size is selected based on the motor's power requirements and the physical dimensions needed to accommodate the components.
Safety and Compliance: Reversing combination starters are designed to provide safe motor control and comply with relevant industry standards, such as NEMA and IEC. They undergo rigorous testing to ensure their reliability and adherence to safety guidelines.
Application Flexibility: Reversing combination starters are suitable for a wide range of applications that require reversible motor operation. They are used in industries such as manufacturing, material handling, and automation, where the ability to control motor direction is essential.
Manufacturer Options: Various manufacturers, such as Schneider Electric, Square D, and Eaton, offer reversing combination starters with different features, options, and accessories. These options may include coil voltage variations, solid-state control, and additional auxiliary contacts.
Motor Control Basics
Motor control allows operational control of electrical motors in various environments.
Motor control circuits provide a safe way to operate electrical motors. Back when motor control circuits were in their infancy, it would have been common to see a simple disconnect switch that would be used to turn on and off a motor. Depending on the size of the motor and how much voltage was required, operating this disconnect would have been dangerous, with a very high possibility of arcing or electrocution. Not to mention that when the disconnect was actuated, the large amount of inrush current would have damaged the motor over time.
In today's motor control circuits, there are a few common pieces of hardware.
A circuit breaker is used to protect the motor and any hardware downstream. A contactor and an overload relay are connected together and function in tandem to allow for remote and safe operation of the motor. The contactor functions much like a relay, allowing for a smaller electrical circuit to remotely close the motor contacts, starting the motor. The overload relay is designed to protect the motor in the case of a prolonged overcurrent event. These two devices are wired in series, so that if the overload relay detects an overcurrent event, the contactor will open the motor contacts, shutting off power to the motor.
The other two most common types of motor control hardware are a soft starter and a Variable Frequency Drive (VFD).
Both of these devices function in a similar way to the motor circuit with some added functions. The soft starter is designed to reduce large inrush current to the motor upon startup. This “soft starting” of the motor will prolong its life and allow for safer operation. The VFD performs the soft start functions, but also allows for speed control of the motor. This speed control is critical in many different environments and has made VFDs one of the most common and safe to use motor control circuits today.