
Close Coupled Pump Motors
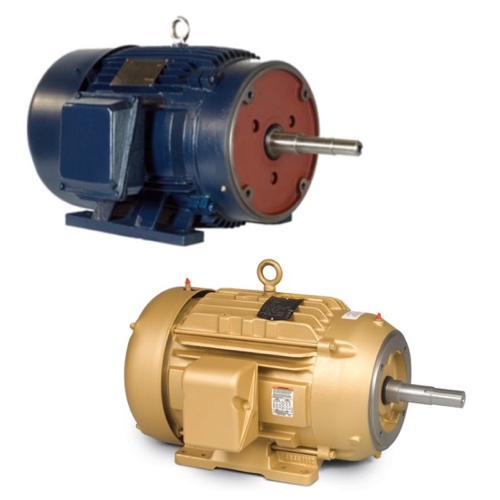
Close coupled pump motors are designed for use in pump systems, but they can also work with a number of other systems. The motors can power many different types of pumps, from centrifugal to regenerative turbine types, and they’re usually quite compact. These small motors can output a lot of power despite their physical size, and the power-to-size ratio is something that many pump and motor manufacturers really seem to like about close-coupled pump motors.
Pump motors that are mounted directly on the pump itself are called close-coupled pump systems. They create more effectiveness between the power (shaft torque and speed) and the volume flow rate (during pump "runout") than pumps either belted to standard motors or those with independent drivers.
Close-coupled pump motors provide several advantages. They offer superior starting torque, allowing them to rapidly achieve the desired speed and power. Unlike some other types, these pump motors can be very power-efficient. Even when the pump and motor must be assembled in a tight space, it's possible to save on power in such situations. And modern pump motors offer a variety of desirable features. Overload protection and adjustable speed control are typical. And for them, both types of features can come in handy in a broad range of applications.
Products
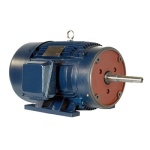
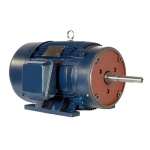
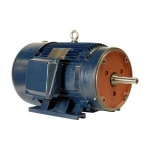
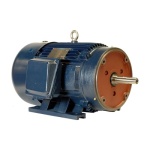
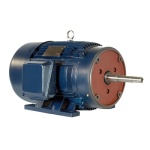
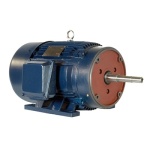
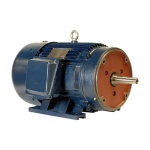
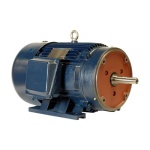
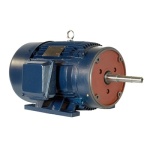
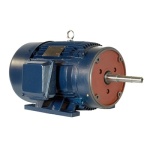
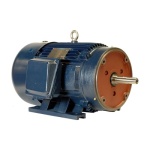
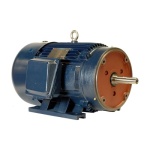
FAQs
Can totally enclosed fan cooled centrifugal pumps made of cast iron be installed in commercial pools?
Yes, totally enclosed fan cooled centrifugal pumps made of cast iron can be installed in commercial pools, provided they are designed to withstand the pool's specific environmental conditions and chemical exposure.
Are a motor shaft, pump impeller, pump casing and drive end all parts of a close coupled pump motors pump motor?
Yes, a motor shaft, pump impeller, pump casing, and drive end are all integral parts of a close coupled pump motor, working together to facilitate efficient fluid movement and mechanical operation.
Motor starters safely start and stop a motor in industrial applications. They are designed with a contactor, overload and circuit protection. They are used when basic motor control is required, where torque on the motor is not a concern and speed control is not needed. Theadvantages of motor starters include: lower cost, allows for remote operation, allows for monitoring of motor state (with the use of auxiliary contacts) and they are safe and efficient. The disadvantages include: high inrush current that can cause fuses to blow and breakers to trip if the inrush is too high, and the starter will allow a full torque to start the motor which can cause the motor to ramp up to full speed very quickly potentially causing the motor to wear and degrade prematurely.
Soft starters protect motors from inrush current by gently ramping up the motor to full speed. They provide all of the same functions as a traditional motor starter. The advantages of soft starters include: they are less expensive than a VFD when only startup control is needed, they are a smaller system than a VFD where space is a concern and they prevent unwanted torque upon startup, prolonging the life of the motor. The disadvantages include: they are more expensive than a traditional motor starter and they do not allow for full speed control.
Variable Frequency Drives (VFDs) allow for the slow ramp up of a motor during startup and the slowing down of the motor during shutdown. They also allow for full speed control during the entire run cycle of the motor. VFDs provide the same functions as both the traditional motor starters and soft starters. The advantages of VFDs include: full speed control (start, stop and in-between), more custom control and monitoring, energy savings due to efficient motor usage and less wear and tear on the motors. The disadvantages include: they are more expensive and larger than other motor control options and they generate heat that may require fans or AC units.