
Sensor-Actuator Cable Assemblies

Sensor cable assemblies are specialized products designed to facilitate secure connections between sensors and devices like sensor actuators or controllers. These assemblies usually consist of sensor cables with connectors at either end, and they come in various lengths to suit different needs. The choice of cable length is crucial, as it can impact the performance and installation process of the sensor system.
Cable assemblies often include features like cable shielding to protect the signals being transmitted. Shielded cables are especially important in industrial environments where electromagnetic interference can disrupt data transmission. The type of shielding can also make the cable assemblies suitable for harsh environments where they might be exposed to elements like dust, oil, or high temperature.
One of the key aspects to consider when choosing a sensor cable assembly is the type of connector. Connectors play a significant role in ensuring a secure connection and fast installation. For example, M8 connectors are often used in industrial applications for their reliability and robust construction. Connector coding is another factor that ensures the right connections are made, reducing the chance of errors during installation.
Products
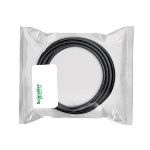
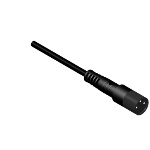
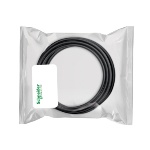
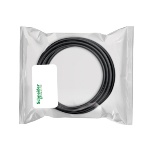
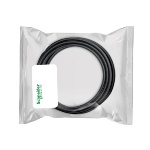
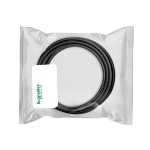
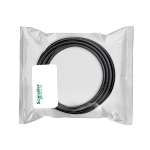
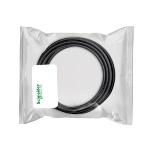
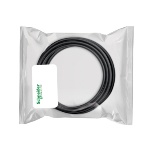
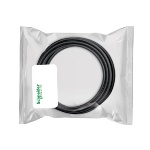
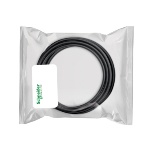
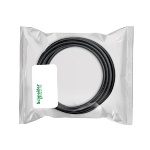
More Information about Sensor Cable Assemblies
In terms of applications, sensor cable assemblies are commonly used in various industrial settings. They can be used for power transmission as well as for sending signals from sensors to programmable logic controllers or other devices. Whether it's for measuring temperature, speed, or any other parameter, these cable assemblies are designed to offer high flexibility and reliability.
Manufacturers like Phoenix Contact offer a range of sensor cable assemblies designed for specific industrial applications. These often come with features like high flexibility and durability, making them suitable for challenging conditions such as those found in drag chain applications or other high-movement scenarios.
Sensor cable assemblies are an integral component in a variety of systems, offering the benefits of fast installation, secure connections, and optimum performance. When selecting one, it's important to consider factors like length, shielding, and connector type to ensure it meets the specific requirements of your application.
Analog vs Digital Control Signals: The Basics
Digital Signals
Digital signals are represented in either a true or false. There is no gray area with digital signals. An example of this might be a light switch. A light switch is either on or off. Another example of this might be a motor that is running or not running. Digital signals can be generated with both AC and DC circuits with varying voltages, currents and resistance. Some practical examples of using digital signals in an industrial environment might be if a pump is running or not running or a whether a valve is open or closed.
Analog Signals
Analog signals convey information in the form of a range. A light switch might be on or off as a digital signal, but a dimmer switch would be an analog signal. It can be on or off, but it can also be somewhere in between. A practical example of using analog signals in an industrial environment would be if there is a need to measure the level of a tank; whether it's full, empty or somewhere in between. Analog signals can take many different forms with some of the more common being a 4 to 20 milliamp signal or a 0 to 5 or 0 to 10 volt signal.
Communication
Communication in a device can either be sent or received. Whether that data is sent or received depends on the type of information. Is there a need to monitor the status of something? If so, an input needs to be received about that information. Is there a need to control something? If so, an output needs to be sent about what needs to occur. Receiving inputs and setting outputs are both things that can be accomplished by using both digital and analog signal types. Therefore, the signals are referred to as analog outputs (AO), analog inputs (AI), digital inputs (DI) or digital outputs (DO).