
Phoenix Contact IO
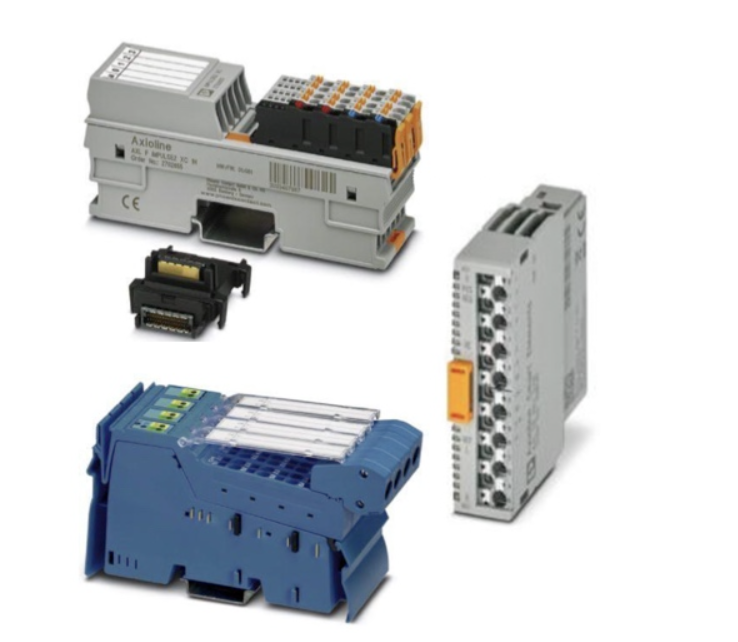
Input/Output (I/O) is central to every PLC. Input is the energy or information that enters a system and is usually related to sensors, switches, potentiometers, and so on. Output is the energy or information that leaves a system and is usually related to lighting devices, electric motors, alarms and so on. Both digital and analog I/O are fundamental in automation technology. Digital I/O is binary in nature and can either be ON or OFF. Digital input devices are push-buttons, light switches and proximity switches. Digital output devices are relays, motors starters and lights. Analog I/O is a time-varying signal and has a range of values. An analog input into the PLC can increase or decrease in very small increments and the PLC can produce an analog output that acts the same way. Analog input devices are pressure sensors and temperature sensors. Analog output can be used to control the power output on a generator or the position of a needle on an analog pressure meter.
Products












More Information about Phoenix Contact IO
Phoenix Contact Remote I/O Systems are suitable for all common bus systems and networks. Acquire input and output signals directly in the control cabinet, systems or machines. Phoenix Contact Axioline Smart Elements are system-independent modules without bus communication. The individual element only supports the I/O function. Phoenix Contact Inline system consisting of PLCs, bus couplers and I/Os for the control cabinet, provides an automation and I/O system that can be used in a large number of projects. The open bus concept provides a number of options in various networks.
Understanding Remote IO
Programmable Logic Controllers (PLCs) are devices that can process multiple points of data ranging from analog and digital signals, both input and output. PLCs read and send data to and from the IO sections of the PLC device. The IO sections can be separate IO cards or they can be integrated into the same hardware as the PLC, like a SCADAPack. Either way, it is important to understand that the PLC is what actually reads and interprets the data and sends out commands. The actual IO is simply the pathway that leads to the PLC.
It is common to see the PLC located in one area, while all of the IO cards or IO hardware are in another. Sometimes the IO hardware will be physically closer to the actual instrumentation that is being monitored and controlled, while the PLC is located closer to a control room. However, it is still necessary for the PLC to receive the data that is being collected by the IO hardware. This is typically done via some ethernet communication protocol. By using a protocol such as Ethernet IP or Modbus TCP, the IO portion on the hardware and PLC can send and receive high amounts of information back and forth.