
SCADAPack PLCs
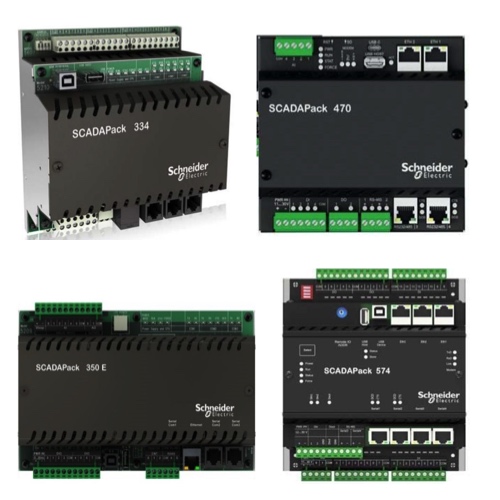
Programmable Logic Controllers (PLCs) are computer control systems that detect the state of all input devices connected to it, make a decision based on a user-created program and then, output commands to any devices connected to it. PLCs monitor, control and communicate automated processes and act as the physical interface between devices and a SCADA or HMI system. PLCs are best suited for simpler processes and smaller automation projects that do not require rapid scalability. They are ideal for both simple and high-speed machine control and can be found in assembly equipment, motion control and dispensing systems.
Remote Terminal Units (RTUs) are devices used for remote monitoring and control of automation devices and systems in industrial environments. They serve a similar purpose to PLCs, but to a higher degree. An RTU is considered a self-contained computer with a processor, memory and storage. It can control multiple processes without requiring user intervention or input from a more intelligent controller. RTUs interface with Distributed Control Systems (DCS) and Supervisory Control And Data Acquisition (SCADA) systems.They can monitor a field’s analog and digital parameters through sensors and data received from connected devices and systems, and send the data to central monitoring stations.
Subcategories
Products






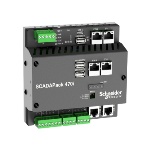



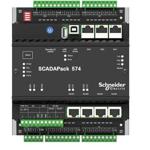
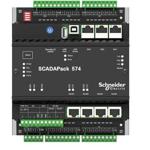
More Information about SCADAPack PLCs
SCADAPack™ Smart RTUs combine the communication and monitoring capabilities of an RTU with the processing and data-logging power of a PLC. They are ideal for remote processes that require automatic supervision and autonomous control. They are designed for the harsh conditions associated with remote sites in applications such as oil and gas and water and wastewater facilities.
SCADA: Learning the Basics
Supervisory Control and Data Acquisition (SCADA) systems are a combination of both hardware and software that allows monitoring of various devices that provide information about specific environments or processes. This information is transmitted through logic controllers, or other smart devices, and is sent to software interfaces known as an HMI, where the information is displayed in a way that individuals can read and interpret the data. SCADA is not only used for monitoring, it is also used for control. Through SCADA, it is possible to manipulate, move, or change the state of certain devices on the network. For example, it is possible to initiate a command through the HMI software that will energize or de-energize a solenoid valve, thus changing its state. In most scenarios, there are dozens, hundreds, or even thousands of points throughout a location or multiple locations that are being monitored and controlled through SCADA. SCADA systems can be found in many different industries such as telecommunications, water and wastewater, energy, oil and gas refining and transportation. These systems can be used to monitor and control only a few simple points, or can be used in massive energy plants where tens of thousands of data points are being interpreted and controlled every minute.
Hardware used in SCADA systems include:
- PLCs, which can act as a bridge between the hardware and software, as well as providing data transmission and network communications.
- Field monitoring and control devices, such as limit switches, temperature transmitters, pressure transmitters, solenoid valves, chemical monitoring devices and motor starters.
Software used in SCADA systems include:
- HMI or Human Machine Interface software receives data throughout the system and organizes it in a way that can be easily interpreted. It can also provide control based on the information it receives.