
NEMA Overload Relays
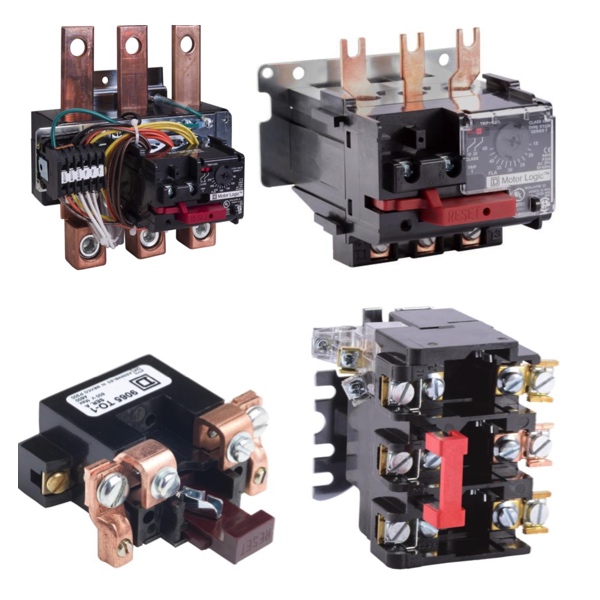
Protecting motors from overload conditions is the function of NEMA overload relays. These devices are quite similar to thermal overload relays, which detect and respond to excessive motor currents. Both types of relays work by interrupting power supply to the motor when necessary. Although neither type can prevent a motor from being subjected to extreme operating conditions, they will help limit how long such conditions go on.
To choose the right NEMA overload relay, several particulars of the motor must be considered: its power, size, and type. The relay itself must be proportionate to the motor and sized to protect it reliably. That's because when an electrical motor is operating near its capacity, heat develops inside it; if that keeps happening over time (as will happen if the protection system isn't working properly), the motor will eventually fail.
Products
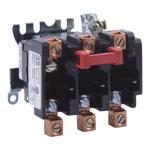










More Information about NEMA Overload Relays
The National Electrical Manufacturers Association (NEMA) provides guidelines for overload relays, defining their types and how they are used to protect electrical motors. Two fundamental types of overload relays exist: thermal relay and the combination starter or bilateral relay. They serve the same purpose, which is to shield an electric motor from operating conditions that could damage it.
A range of application considerations determines which type of NEMA 1 or NEMA 6 relay is needed. Thermal overload relays are applied primarily in continuous service where excessive heat would develop in the motor windings if its protection roam exceeded its rating for any length of time. Thermal Relay Operation A thermal overcurrent relay will disconnect power to a motor when it carries more than its rated current for a period wasted in overheating while serving an intermittent demand sporadically subjecting the motor run section to a nastily cooked appearance resulting from working too long under harmful conditions without being allowed adequate rest periods during operation as normally available with switches.
FAQs
Do NEMA overload relays use contactors to provide overload protection and protect motors from overheating?
Yes, NEMA overload relays use contactors to interrupt the motor circuit when an overload condition is detected, thereby providing overload protection and preventing motors from overheating.
Motor Control Basics
Motor control allows operational control of electrical motors in various environments.
Motor control circuits provide a safe way to operate electrical motors. Back when motor control circuits were in their infancy, it would have been common to see a simple disconnect switch that would be used to turn on and off a motor. Depending on the size of the motor and how much voltage was required, operating this disconnect would have been dangerous, with a very high possibility of arcing or electrocution. Not to mention that when the disconnect was actuated, the large amount of inrush current would have damaged the motor over time.
In today's motor control circuits, there are a few common pieces of hardware.
A circuit breaker is used to protect the motor and any hardware downstream. A contactor and an overload relay are connected together and function in tandem to allow for remote and safe operation of the motor. The contactor functions much like a relay, allowing for a smaller electrical circuit to remotely close the motor contacts, starting the motor. The overload relay is designed to protect the motor in the case of a prolonged overcurrent event. These two devices are wired in series, so that if the overload relay detects an overcurrent event, the contactor will open the motor contacts, shutting off power to the motor.
The other two most common types of motor control hardware are a soft starter and a Variable Frequency Drive (VFD).
Both of these devices function in a similar way to the motor circuit with some added functions. The soft starter is designed to reduce large inrush current to the motor upon startup. This “soft starting” of the motor will prolong its life and allow for safer operation. The VFD performs the soft start functions, but also allows for speed control of the motor. This speed control is critical in many different environments and has made VFDs one of the most common and safe to use motor control circuits today.